What is Poka-Yoke? (Definition, Examples, and Benefits)
Have you ever gone through the steps of a process and thought, “Wow, that was easy”? If you have, there’s a chance that poka-yoke was involved. There’s a common refrain that good design goes unnoticed. Maybe that’s why you haven’t heard of poka-yoke until just now.
At Veryable, we’ve interacted with thousands of operations leaders who use our on-demand labor platform to flex their labor capacity. This often wouldn’t be possible without a little poka-yoke on the part of these companies to make their work approachable and repeatable.
In this article, you’ll learn what poka-yoke is, how it’s used, and what benefits your business could see from using this tool.
Poka-Yoke definition
Poka-yoke is a Japanese term that means “mistake-proofing.” It is a Lean tool that originated from the Toyota Production System.
Implementing poka-yoke involves designing a process in such a way that mistakes are avoided entirely or made visible for quick correction. Poka-yoke can also be called a forcing function or a behavior-shaping constraint. It is essentially defensive design applied to processes.
Example of poka-yoke in action
A great example of poka-yoke is when you have to put your car in park and push in the brake before you can start it. This is so that you don’t start the car and immediately begin rolling by accident. A simple step added to the process of starting your car makes this costly mistake practically impossible.
Over time, you will build the habit of depressing the brake pedal before starting your car. You might even continue doing this after you get a new car, whether or not it relies on the same forcing function. This is the power of poka-yoke!
Poka-yoke in manufacturing
Poka-yoke has also been applied in the manufacturing environment to keep error rates low, improve safety for workers, and improve efficiency for businesses.
There are multiple ways to implement poka-yoke in your processes. The inventor of poka-yoke, Shigeo Shingo, identified three main types of poka-yoke:
- Contact
- Fixed-value
- Motion-step
We will cover each of the three methods in more detail below.
Contact method poka-yoke
The first type of poka-yoke you could implement would be the contact method. This method is best when there is something physical you need to check on the product to ensure there are no defects, or when the physical design of a process can prevent errors.
To implement a contact poka-yoke to check for errors, you would add a step in your process wherever you need to inspect a physical aspect of the product that could cause a critical error.
To prevent errors, you could use a physical tool such as a jig that makes a process easier to repeat without error.
You can see the contact method at work in products that they physically prevented from being used in the incorrect way. A USB cable is a good example of this, as you can see when you try to plug it in the wrong way three times in a row. It is very difficult to plug a USB cable into the wrong port.
Fixed-value method poka-yoke
The fixed-value poka-yoke method involves warning a worker when a specified number of actions has not been met. This would be applicable in a situation where the number of actions is clearly defined and each is critical to the end result of the process.
One example of this would be an assembly step that requires six screws. If the worker does not drill all six screws, this part would not be secure. Using the fixed-value method, you would have a system in place where the worker can see when not all of the screws for each unit have been used yet so that they can finish the product and avoid an error. This could be accomplished with a timed release of only the needed parts, for example.
Motion-step method poka-yoke
The motion-step poka-yoke method requires implementing a process checklist and ensuring that all steps (and only those steps) are followed.
This is best accomplished by guiding the worker using digital work instructions or a similar system to ensure adherence throughout the process, which will avoid mistakes and the need for rework.
Benefits of poka-yoke in manufacturing
There are many benefits of poka-yoke for businesses and workers. We will cover four main benefits in detail below.
Reduced waste
With well-designed processes that aim to avoid mistakes and quickly spot any errors, waste reduction is inevitable. Poka-yoke delivers on this goal by building quality into your processes, which reduces the need for rework by reducing defects.
Reduced training time
Because poka-yoke focuses on avoiding mistakes in a process, it makes the work hard to do wrong. That means it will take less time to train workers, because the process will have instructions or steps built into it that do away with the need for reliance on memory or special training.
Improved safety
Most if not all hazards in the workplace can be addressed by implementing poka-yoke. By making it physically impossible to start a machine until the operator is in a safe zone, for example, safety is built into the work process. This type of thinking can be applied to your facility in many ways, with the aim of making it difficult (if not impossible) to get injured accidentally.
Higher productivity
With less time spent by workers questioning what step is next, reworking defects, making mistakes, and training, your facility will see higher productivity. Effective implementation of poka-yoke affects your top and bottom line by driving out errors, ambiguity, and other waste to net you a more efficient production process.
Is poka-yoke right for you?
If you see that your workers are doing a lot of rework, or your processes are producing errors left and right, then you probably have an opportunity to introduce poka-yoke.
It’s not always clear how to do this, but often the easiest place to start is by creating a checklist. Then you can move into changing the physical design of the process, or implementing guiderails (physical or digital) that will show workers when they’re off track.
We can help you with your poka-yoke implementation and other Lean initiatives through our Lean Center of Excellence. Our team includes operations experts with decades of combined experience in leading improvement initiatives.
Veryable Tools to help eliminate waste
Veryable's On-Demand Labor Marketplace
Labor will directly or indirectly touch every aspect of your operational performance. It is also one of the largest expenses on your P&L. Ignoring opportunity or being comfortable doing things the way they've always been done makes it just that much harder to find net improvement elsewhere. Leveraging Veryable’s On-Demand Labor Marketplace to build a flexible extension of your full-time workforce will allow your team to precisely match labor capacity to demand on a daily basis. Think of it as Just In Time labor capacity, eliminating wasteful overtime and underutilized labor when there is not enough work. Adopting this approach gives your operations leaders the resources they need to deliver the maximum return for the business and the most value for the customer.
Veryable's Workforce Management Tool
Veryable’s Workforce Management Tool ties together multiple systems (ERP, WMS, MES, HRIS, etc.) to use real-time data to automate the labor planning process and guide your leadership in making better critical decisions. This eliminates guessing, protects against costly forecasting inaccuracies, and enables performance-based decision making without the burden of manual spreadsheet updates or back-of-the-napkin estimating. This tool can operate as a standalone platform for your full time employees, or you can access Veryable's on-demand marketplace from within this tool to fill any gaps in your operation on short notice. The best part is, you'll be able to view real-time performance data in just clicks for both full time employees as well as Veryable Operators.
Together these systems truly optimize every labor dollar spent across your footprint. This enables better visibility to translate best practices, and can act as a roadmap for continuous improvement.
For more information, visit our Lean Center of Excellence Homepage or our homepage for Continuous Improvement, Operational Excellence, and Lean Professionals.
Previous Posts
Creativity over Capital: Growing Your Business Without Capital Investment
The Future of Manufacturing and Logistics
Create a free business profile today to explore our platform.
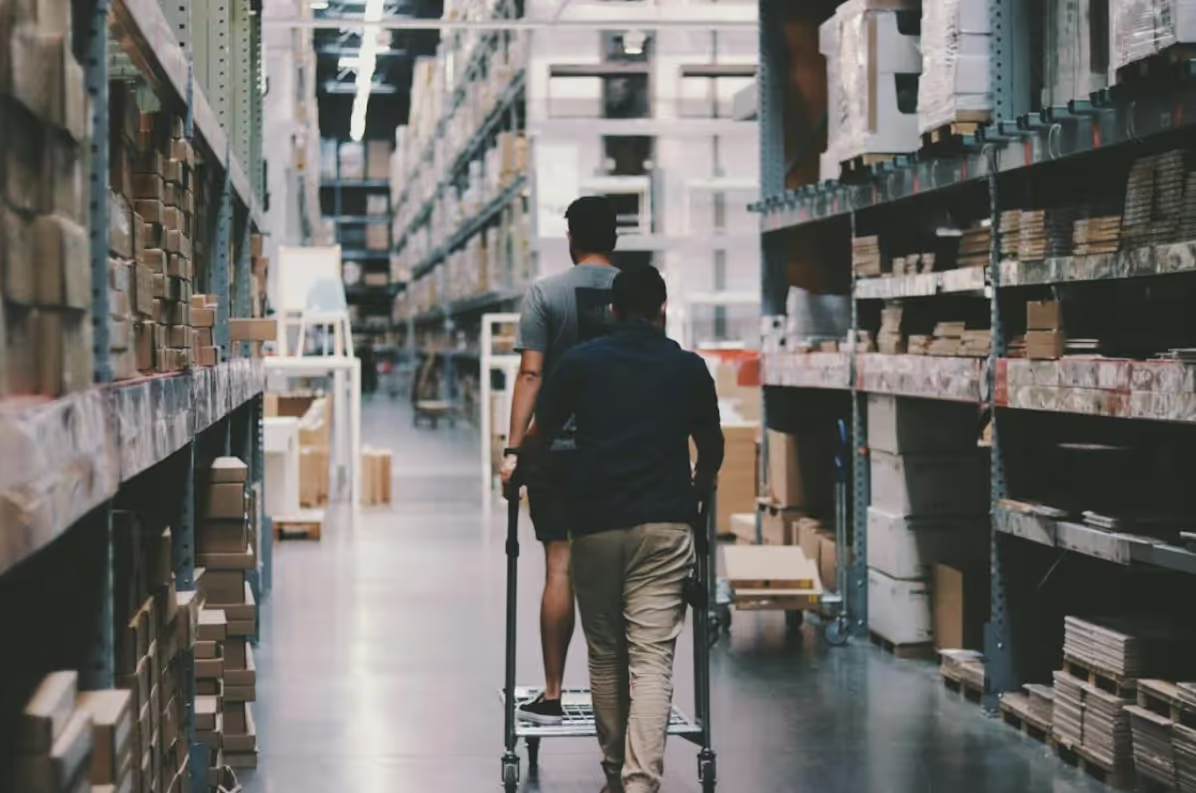