What is Lean Manufacturing?
You’ve probably heard of Lean before. It’s the thing everyone is talking about, but nobody seems to be able to explain when you ask them about it. Is it a book? Can you do it without a teacher? Do you have to join a club to learn its secrets?
This article will clear up what Lean is, what Lean manufacturing is, and how it can be applied to your business for powerful results.
Early in my career, I had the honor of working with some of the greatest Lean practitioners in the business when I toured Toyota operations and learned from their sensei (teacher). I then led transformation and deployment efforts across a variety of businesses, and Lean became a part of how I solve problems from then on. As a VP of Operations for Veryable, I get the opportunity to walk the shop floors of our business users and help them see these same opportunities to dramatically improve their businesses.
Veryable provides a tool for finding on-demand labor, which is useful when following Lean principles.
By the end of this article, you will know what the Lean methodology is, the principles Lean is built on, and why it is important for your manufacturing business.
What is Lean?
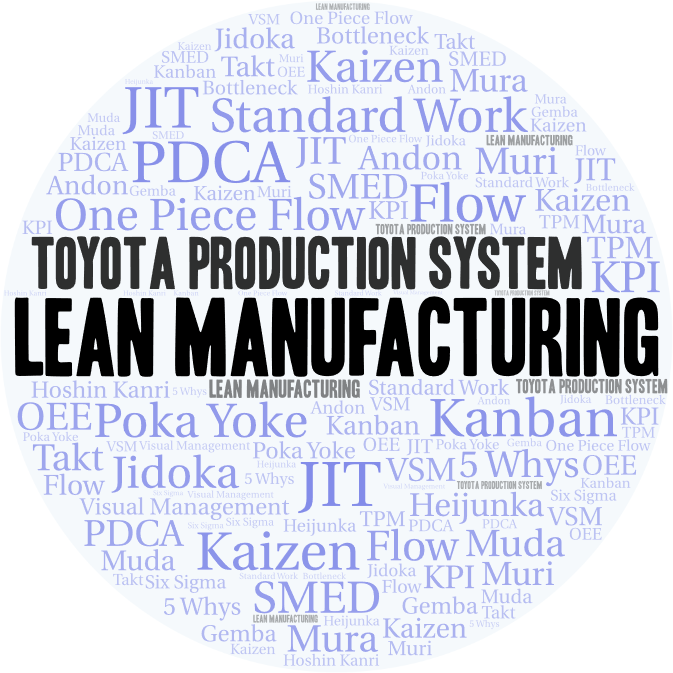
Lean is a way of thinking, first and foremost. It is built out of a respect for people and their abilities to solve problems. Lean is a methodology and mindset focused on creating more value for the customer while minimizing wastes.
When Lean is applied to manufacturing, it is called Lean manufacturing. Lean actually originated in manufacturing, when it came out of the integrated production processes developed by Henry Ford. It was perfected out of necessity after World War II with the Toyota Production System. Since then, the tools and concepts have been studied, implemented, and translated beyond manufacturing. Lean practices have become popular in logistics, distribution, services, healthcare, government, and many other industries.
With the dramatic impact this methodology has had, it is easy to see why leaders want to learn more about it and understand if it is right for their operations.
What are the core concepts of Lean?
To sustain the improvements made possible by the many tools built around Lean, you must focus on the core concepts and principles to create a compatible culture in your company.
- The first core concept of Lean is creating more value for the customer. From a customer’s perspective, the value of any product or service depends on whether it is something that they want and whether it is offered at the right price, at the right time, and with the right quality. The important distinction here is that value is defined by the customer, not internally by your business.
- The other core concept of Lean is the focus on minimizing wastes. Waste in this context is any activity that consumes resources but creates no value for the customer. Those wastes will fall into one of two buckets: that which is currently unavoidable and that which can be eliminated immediately. In Lean methodology, there are eight distinct wastes: defects, overproduction, waiting, neglect of human talent/intellect, transportation, inventory, motion, and overprocessing. Reducing these wastes is your top priority if you want to create more value for the customer with what you have.
Why should your business use Lean?
When practiced correctly, Lean is a mechanism to dramatically improve three business fundamentals: speed, cost, and quality.
Speed Improvements with Lean
Lean focuses on eliminating any activities that do not add value to the final product. Value-added activities are a small percentage of the total lead time to get through a process. By eliminating the wasteful activities that do not add value, you increase the speed of your business processes. This has a massive impact on cash flow and how quickly you can sell and replace inventory, which can be a competitive advantage.
Cost Improvements with Lean
By eliminating the wastes that do not add value to your product you are also eliminating the resources that those wastes consume. For example, workers wasting time on an activity that does not add value means the cost of their wages is being wasted on that activity.
Eliminating wasteful costs can expand your margins, make you more competitive in the market, or free up equipment and labor to fuel additional growth for your business.
Quality Improvements with Lean
Lean emphasizes focusing on quality at the source and making sure that production is done right the first time, every time. By doing this, you eliminate the downstream cost of rework and reduce the odds of low-quality products escaping to the customer. This can protect customer confidence in your company and avoid undue production and labor costs.
The Five Principles of Lean
Lean methodology is founded on five principles captured and popularized in Lean Thinking by James Womack and Daniel Jones. The five principles are guidelines to help you align your business with the core concepts of lean.
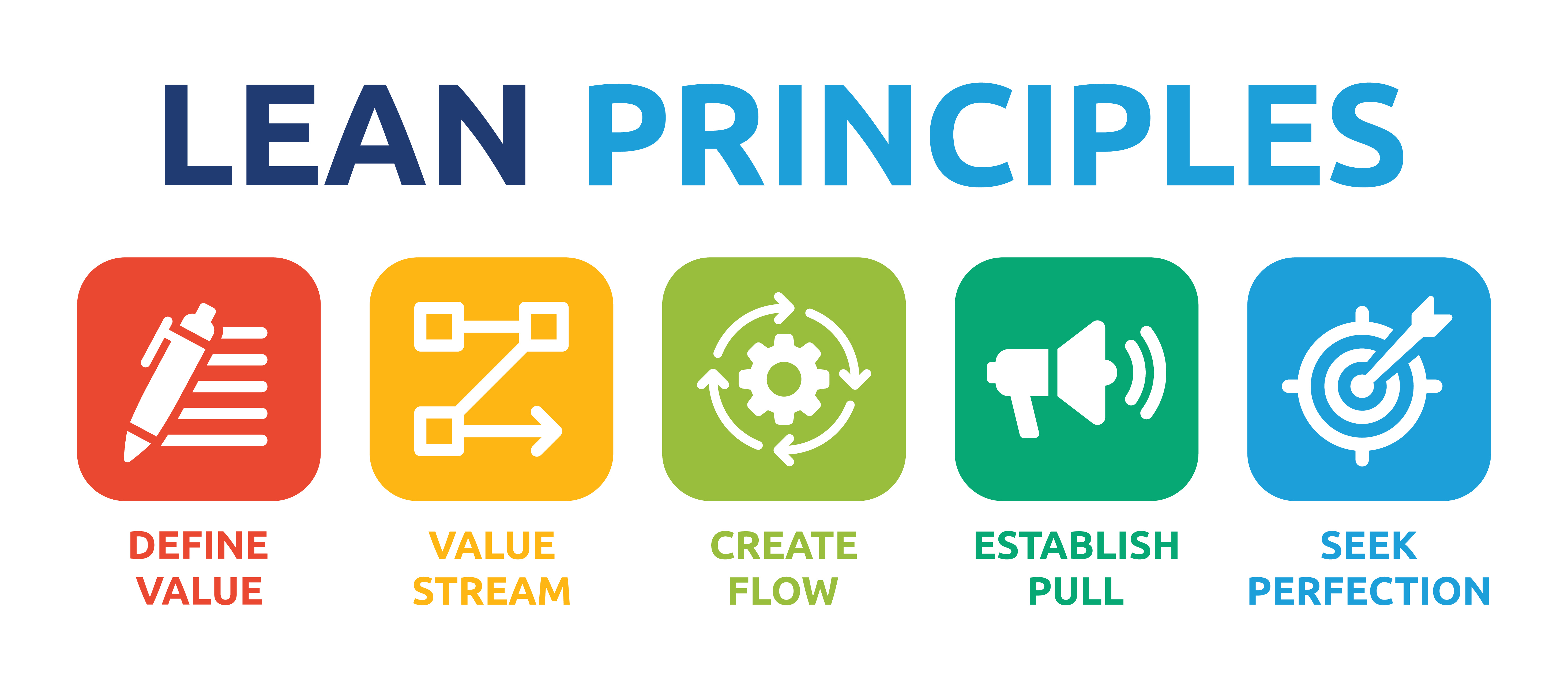
1. Specify value from the standpoint of the customer
Ultimately, the value a customer sees determines what the customer will pay. Understanding what the customer wants helps you differentiate between value-add and wasteful activities. Artisan chairmakers might disagree, but if the customer will never see the underside of a chair and you spend time painting it with an intricate design, this would be considered a wasteful activity in the Lean manufacturing framework.
2. Map the value stream
A map of your value stream is a visual representation of all of the steps and actions required for material and information to flow from raw material to customer use. You can create this using flowchart software, a whiteboard, or even a sheet of copier paper. The point is to externalize this information so you can easily see where you’re currently at. From there you can eliminate waste and design your future state.
3. Create flow
Waste is inevitable if the value stream stops moving, because starting and stopping introduces costly complications and lost time. That is why Lean emphasizes stringing value-added activities together and keeping a product moving between steps without stopping. Creating flow enables waste elimination and dramatically reduces the overall lead time.
4. Establish pull
Establishing pull means nothing is made until the customer orders it. This eliminates any overproduction and ensures flow is maintained. Establishing pull requires a great deal of flexibility. Traditionally, manufacturers plan far in advance and stock up in preparation for customer demand. Creative thinking, operational tools like on-demand labor, and process improvements can help achieve the needed flexibility.
5. Seek perfection
Buckle up, it’s going to be a long ride. Lean practitioners refer to practicing this methodology as a Lean Journey because there is no destination or end in the process.
The Lean Journey is about making continual improvements by reducing time, costs, space, mistakes, and waste in pursuit of perfection.
Because we can never reach perfection, this process never ends.
How to start with Lean
All of these concepts and principles might have you asking, “Where do I start?”
The answer is: right where you are. Pick a value stream — one product line, for example — and start an experiment with the goal of eliminating waste. As long as you keep in mind the two core concepts of value creation for the customer and waste elimination, you’ll be off to a great start.
As you begin implementing Lean, labor is one area where you might be surprised to find waste. Waste here is often found in the form of waiting and neglect of human talent. Most of the time, workers who are standing around waiting for work are still being paid. This is a waste of the company’s money and the worker’s time, because their talents are not being used.
At Veryable, our mission is to revitalize the manufacturing sector by allowing businesses to “variablize,” or make flexible, labor costs in small increments and incur these costs in direct proportion to output. Put simply, you can pay more workers just while you need more work done and return to your normal labor costs immediately after.
Having a flexible supply of labor enables you to improve flow, establish pull, and reduce lead times, which are often very valuable to the customer when they are shortened.
For more information, visit our Lean Center of Excellence Homepage or our homepage for Continuous Improvement, Operational Excellence, and Lean Professionals.
Previous Posts
Old Roles, New Realities - Who Owns Agility?
The Future of Manufacturing and Logistics
Create a free business profile today to explore our platform.
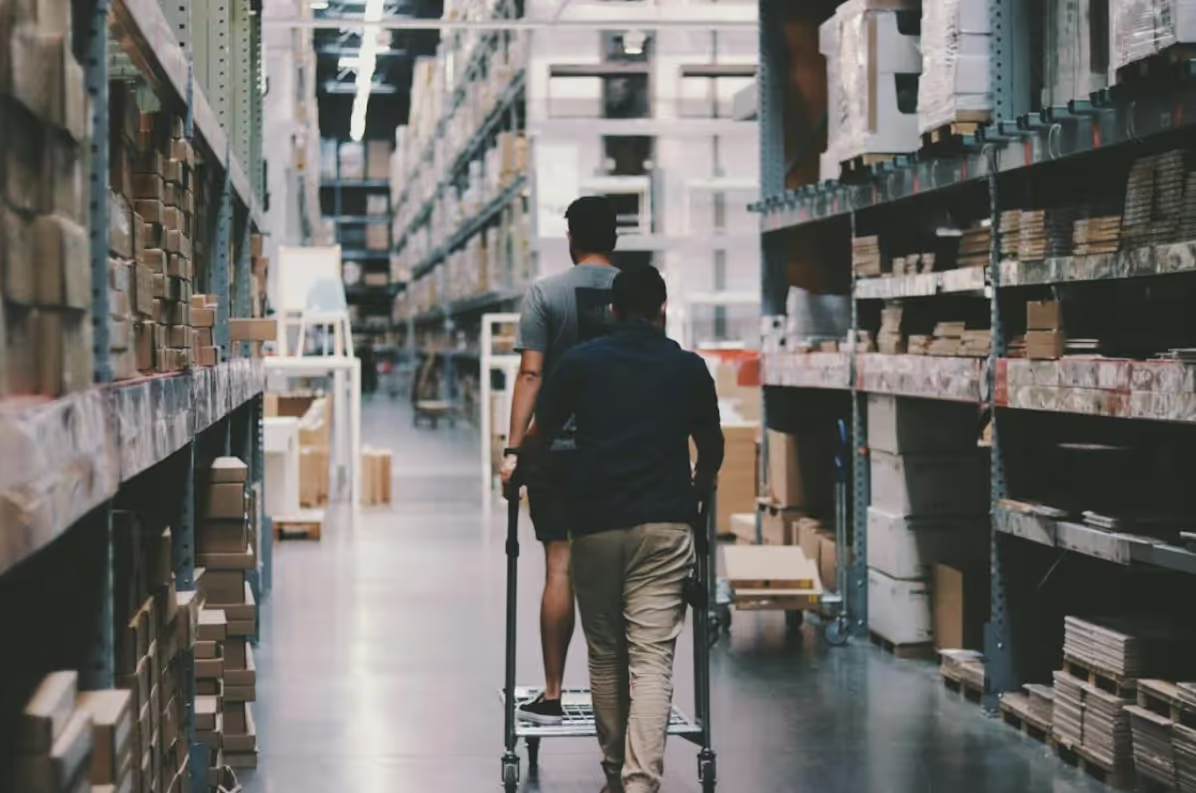