Manufacturing Metrics You Can Improve with On-Demand Labor
Sure, on-demand labor sounds like a great solution for finding workers when you need them. But what business goals can you achieve with on-demand labor?
At Veryable, I’ve had the chance to study businesses using our on-demand labor platform and the innovative ways they’ve solved problems in their facilities with the help of on-demand workers. These businesses are improving on a wide variety of metrics, and each business has unique goals and processes. However, I’ve had several conversations with our team to find commonalities that we feel are worth sharing.
In this article, you’ll learn common manufacturing metrics across five main categories and how you can improve them with on-demand labor. You’ll know how you can affect service, inventory, productivity, quality, and safety metrics in your operations by bringing in workers on demand.
If you're in logistics or distribution and not manufacturing, read this article instead.
Types Of Metrics You Can Impact Through On-Demand Labor
- Service
- Inventory
- Productivity
- Quality
- Safety
Service
Customers, and their orders, are the lifeblood of your business. In some circles this is referred to as “Delivery”, but the intent is to measure how well you’re servicing customers. It is hard to win a new customer but it is harder to keep them with poor performance in this area.
The table below shows common service metrics that can be used to keep up with how well you’re performing and identify areas for improvement.

On-time delivery (OTD)
This metric is the percentage of orders you are delivering on-time. Having a high OTD percentage can help ensure customer confidence, stabilize a relationship, and differentiate your business to position yourself for incremental growth.
While it is easier to measure performance against your commitment date, it is better to measure OTD against the requested date from the customer. This is a more accurate way to understand the ability of your business to satisfy the demand of your customer and the market. Although this varies from industry to industry, your facility should aim for a minimum of 95%. Businesses are able to differentiate themselves and really stand out at the 98% OTD level and above.
Actual lead time
Actual lead time measures how long it takes to order, manufacture, test, and ship your product. This is an important metric to compare against competitive lead times in the market. Actual lead time can tell you if you have the opportunity to reduce lead times to become more competitive, or if your current lead times are out of sync with what the market demands.
Great manufacturing companies know that working to continuously reduce actual lead time is important because it enables growth and positively impacts service, inventory, and productivity metrics.
Past-due backlog
The past-due backlog metric highlights the sales value of your backlog that is late. This is a great metric to plot over time to establish a baseline.
It’s important to understand what makes up your past-due backlog. Many companies will plot a line showing the average age of orders in their backlog and overlay this onto a bar graph of the number and value of orders. This way they can see at a glance how many people they’re making angry (number of orders) and how mad they’re going to be (value and age of orders).
This should be used to drive an understanding and action plan for getting better. Since you don’t get revenue until you make the sale, this is an easy target to attack to stay on top of facility forecasts and financials.
How can on-demand labor impact service metrics?
On-demand labor can help recover or maintain these metrics in many different ways. Incremental capacity can be added to a current shift or to build out second, third, or weekend shifts to improve service levels by completing the work faster.
Finding on-demand workers to perform support tasks is a great way to increase throughput in bottleneck operations or to increase output of your highly skilled workforce. Check out our blog on reducing cycle times for more detail on how to leverage this as a competitive advantage.
Inventory
Inventory is a key performance indicator that requires almost constant attention. Too much inventory and your cash is tied up and lead times are extended; too little inventory and you can starve your operations.
The mix needs to constantly be monitored and optimized to be effective for both your facility and your customers. The chart below shows some common metrics used to help keep your inventory at the right level for your business.

Inventory value
Inventory value highlights the cash value that is tied up in raw materials, work in process, and finished goods inventory. At each stage, there are incremental labor costs included in the inventory value of that item. Each of these buckets has unique levers you can pull to impact that value.
Raw material is typically controlled by ordering practices, while work in process is a function of how work is released to the floor, how work centers are scheduled, and how labor is allocated. Understanding your inventory mix is critical if you want to try and optimize how you use your inventory value.
Inventory accuracy
Having what you need when you need it is important to running your operation. Inaccuracies in raw materials, work in process, or finished goods have rippling effects in your scheduling system and therefore impact your service performance. That is why inventory accuracy is an important metric to track.
One way to improve inventory accuracy is through cycle counting. There are different ways of doing this, but the idea is the regular auditing of part numbers and quantities to ensure that inventories are accurate. If you find an inaccuracy, you should double check it and then update your inventory records so you can immediately act to fix what’s causing the inaccuracy.
It is important that your business understands where these disconnects occur so you can fix the underlying problems. You should target 99% accuracy during these cycle counts. In certain circumstances when this can consistently be demonstrated for an extended period of time, you may be able to replace physical inventory, saving money and time.
Inventory turns
The inventory turns metric is a measure of how frequently a facility is converting its inventory into revenue over a 12-month period. Similar to other inventory metrics, this is good to baseline and improve upon, but a deeper dive is required to understand where action should be taken.
Inventory turns can be compared to cycle times to determine if you are on track. For example, if your raw materials turned over 3 times in one year, then you held raw materials for 122 days on average. If your cycle time is 30 days, then that means you are holding about four times as much as you really need.
Main drivers that impact inventory turns are ordering practices, work in process levels between work centers, utilization of equipment, schedule attainment, and obsolescence.
How can on-demand labor affect inventory metrics?
Many inventory functions are controlled by how material is ordered, released, and transacted on the shop floor. On-demand labor can have a huge impact on how quickly inventory can be converted to revenue.
Increasing the throughput with incremental operators or expanding shifts will increase the speed at which your business can move all of your inventory. These same actions can be targeted at specific work centers to shrink the inventory buffer permanently and allow new orders to flow through more quickly.
On-demand labor can also help with cycle counting to make your systems more accurate without pulling your key employees from operations.
Productivity
Productivity is a KPI that probably has more metrics to look at than any other. Each operation, team, and strategy has a unique way of defining and understanding what it means. Since productivity is fundamentally the ratio between inputs and outputs, we want to look at some high-level ways to check your plans, processes, and equipment.

Units produced per plan
Measuring units produced per plan is one of the simplest ways to understand if what went awry was the plan or the execution of that plan. Usually, the mistake was a combination of flaws in both the plan and execution, but unless you look at this in discrete buckets you won’t begin to understand the scope or the scale of the problem.
You can use this metric in daily (or better yet hourly) buckets to determine performance against a plan, the reason for a miss, and what the plans are to fix those misses. Over time this creates engagement in the process and, if done correctly, can create permanent solutions that improve performance.
Efficiency
There are many ways to look at efficiency, but for our purposes, it is comparing actual hours logged for an operation against a standard amount of time that it should have taken. This can be used for setup of a machine or for running individual parts.
Both setup and run time are components of the standard cost of a part. Outperforming these times results in a lower unit cost and incremental margin. Underperforming can have the inverse effect, chipping away at profitability.
Utilization
Utilization measures what percent of available time a machine is running, and making parts. This is important for a variety of purposes. It can tell you how efficiently you are running a piece of equipment while it is available. It can also highlight bottleneck operations which should trigger adding available machine time with incremental shifts. Call-ins can compound an issue in a bottleneck operation, where you can never get that time back. If utilization is high and operations are running 24/7, this may warrant moving load off of that machine or adding capital.
How can on-demand labor affect productivity metrics?
No one is more experienced in your processes and the underlying opportunities than the skilled employees who live and breathe them daily. On-demand labor can support your experts and allow your facility to leverage your skilled full-time employees to participate in or lead continuous improvement plans to identify and solve productivity issues.
Another way to surface these opportunities is to bring in fresh operators through on-demand labor for their ideas. If you use piecework pay, they are incentivized to optimize processes for speed, allowing you to capture, standardize, and translate them across your operations.
Quality
Quality is expected from your customers and poor performance can be extremely disruptive to their business and your relationship with them. The way you slice and dice data can get extremely technical and nuanced to your industry and product. Since we can’t know exactly what works best for you, we highlight some common metrics that are used across most operations in the table below.

External defects
Once non-conforming material reaches your customer it is considered an external defect. Defects can be presented in parts per million (PPM). While safety-critical industries hold much tighter requirements, general expectations are PPMs below 1,000, which is about a 0.1% rate of defects.
Immediate containment is the first step you should take to make sure you are not continuing to produce bad parts. It is important to understand the root cause of the defect so that it does not happen again. There are a variety of different quality tools that can be used to drill down to that appropriate level.
First pass yield
First pass yield is a straightforward way of looking at the percentage of parts that pass the first time through. Parts that fail the test will then require some sort of rework, which drives incremental cost into the part or can disrupt the flow of parts through the line. This creates a bottleneck and hurts output from the line. A low first pass yield is an indicator of unstable processes and indicates a source of external defects.
Scrap as a percentage of sales
The scrap as a percentage of sales metric is a ratio of the total cost of the scrapped parts (including material, labor, and overhead) to the total revenue of the same period. This is another good baselining metric to understand where your current performance is and inform improvement actions.
Understanding assignable causes will allow you to fix them and improve control levels around them. The Lean concept of poka yoke, or mistake proofing, is the ultimate goal. To implement poka yoke, you design processes to remove the possibility of creating the same defect again. Quality defects and scrap should target zero, but for most industries 1% is approaching best in class performance.
How can on-demand labor affect quality metrics?
In the event that your business has to deal with a return, on-demand labor can be brought in to help sort, inspect, or contain issues within your operations keeping your experts focused on solving the root cause.
To prevent quality issues, you should implement controlled processes, standard work instructions, and in-process testing as part of your training for full time and on-demand labor. You should also check to make sure quality is part of the rating system for operators when evaluating on-demand labor options to use, so you know you can expect quality work from the workers you select.
Safety
We all want to go home in the same physical shape that we came to work in. We are all responsible and accountable to those around us to make that happen. Here are some common metrics associated with workplace safety and why they are important.

Near misses
Near misses are unplanned events that did not result in an injury, illness, or damage despite having the potential to do so. These near misses or observations highlight opportunities to prevent future accidents.
The main objective when responding to near misses is to develop corrective actions that minimize and eliminate the opportunity for them to happen again. As you put these actions in place, it becomes harder and harder to keep identifying new opportunities so an engaged workforce is critical to keep a critical eye and report potential issues.
Sickness rate
The sickness rate metric can uncover underlying problems like heavy workload, bad working conditions, a dangerous environment, and/or low employee satisfaction. A high sickness rate can be an indicator of an unhealthy work environment that can lead to a higher recordable rate and time away from work.
Total recordable incident rate
The total recordable incident rate is the ultimate measure of safety performance. Unfortunately, this is a lagging indicator based on the number of incidents including deaths, illnesses, and injuries that require professional medical treatment.
The equation in the table above allows for the rate to represent the number of recordables per 100 people in that operation. The 200,000 figure normalizes this calculation across companies of different sizes, and was calculated by multiplying 100 people by 40 hours a week and 50 weeks per year.
Obviously, a high total recordable incident rate is something to avoid at all costs.
How can on-demand labor affect safety metrics?
Background checks, a rating system that includes safety ratings, and the ability to remove and block unsafe workers all lead to a safer work experience with on-demand labor. It has also been found that being in a new environment increases situational awareness.
This means bringing in new on-demand workers could help drive new ideas and solutions around solving safety issues because they might be aware of things that others have taken for granted in their routine exposure to the work environment.
Click here to read more on this.
What else can you do with on-demand labor?
Improving metrics is the end result of properly using on-demand labor. But how do businesses achieve these results?
The best way to make use of on-demand labor is to build a labor pool. This is like a flexible extension of your workforce that’s been trained in your operations and can pitch in when you need some extra help. Read more about labor pools and how they work in our thought leadership blog.
To learn more about how Veryable can help you improve the metrics you're responsible for, check out our info for your role page.
To see the real-world results, check out our assortment of case studies.
Previous Posts
Old Roles, New Realities - Who Owns Agility?
The Future of Manufacturing and Logistics
Create a free business profile today to explore our platform.
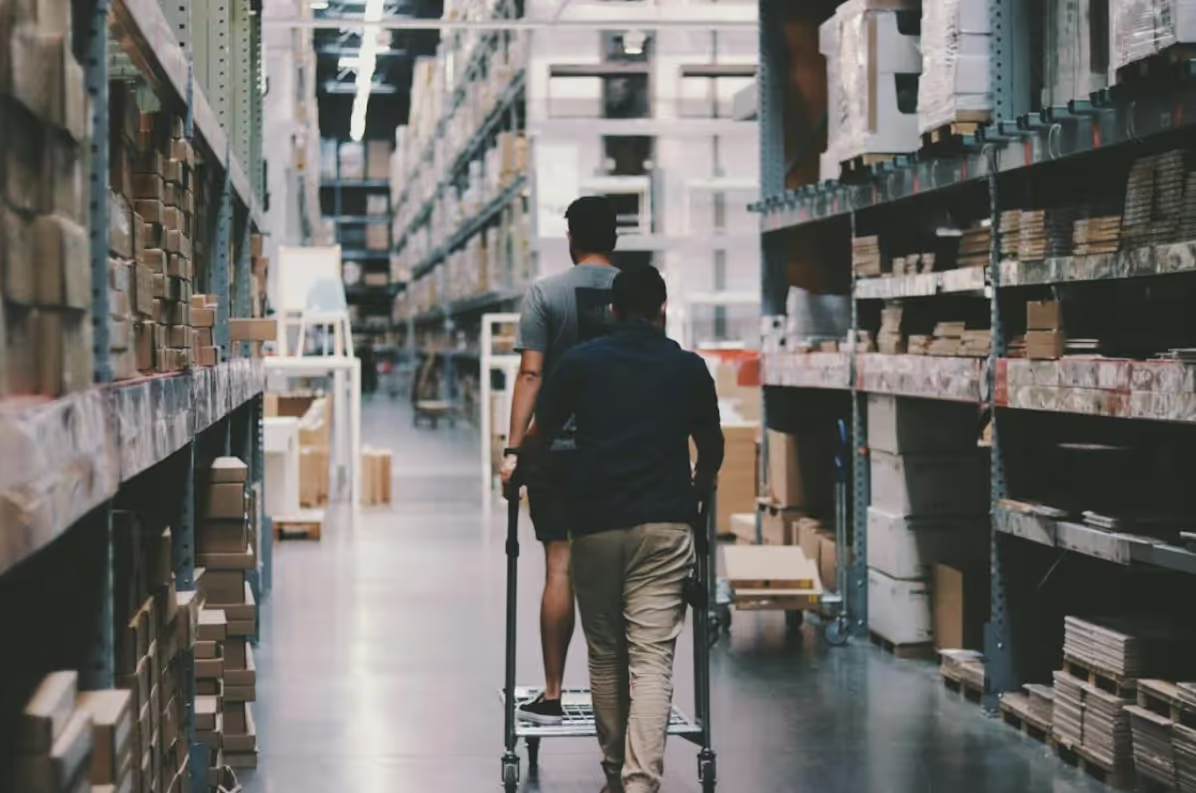