Kanban for Manufacturing: Cards, Boards, and Supermarkets Explained
When you need to know what to produce, how much of it to produce, and what order to produce it in, you have a couple ways to approach the problem. You can push through orders and create piles of inventory, or you can pull orders continuously to keep your production flowing smoothly.
Kanban helps you do the latter, while making it easy to see what’s going on and prioritize your production queue. This pull production system has been a part of leading companies’ toolboxes for decades, and it’s still kicking today.
At Veryable, we believe in pull-oriented production systems as the best way to meet customer demands without unnecessary waste and friction. In fact, our on-demand labor marketplace enables companies to make operational improvements with the same goal of demand-oriented production that pull systems have. We won’t focus on our company here, though.
In this article, you’ll learn what kanban is, how it works, whether it’s right for you, and what you need to get started.
What is kanban?
Kanban is a pull production system that creates a connection between each physical widget and its replenishment signals. It is a visually simple way to manage and track production that flows smoothly.
The kanban system is a time-tested Lean tool that was invented by Taiichi Ohno as part of the Toyota Production System. It has helped many companies manage their production and reduce WIP inventory over the years, and is still commonly used today.
There are six rules in the Toyota Production System for implementing kanban:
- Never pass on defective products
- Take only what is needed
- Produce the exact quantity required
- Level the production
- Fine-tune production
- Stabilize and rationalize the process
These rules should guide you as you implement the “how” outlined below.
How does kanban work?
The kanban tool set consists of cards, boards, and supermarkets. Nothing gets produced without a card, and cards don’t move until a widget is pulled down the line to fill an empty space, or until the finished product is pulled to ship to the customer.
Kanban cards
Kanban cards are attached to each widget (or bin) and follow them through the production process until the very end. Each card indicates the type and number of widgets to be produced in each production run.
When a finished product (or bin) is pulled for shipment to the customer, its kanban card is passed back to the beginning of the process at the heijunka box to signal that a new production run is needed.
You might also hear of “two-bin kanban systems.” This is when you have two bins at a workstation holding parts. We’ll use screws in our example.
When the first bin is empty, the worker rotates that bin and its associated kanban card with the second bin, which is still full of screws. Another worker comes and gets the empty bin and uses its kanban card to see how many and what type of screws they should refill the bin with.
Heijunka boxes
A heijunka box is a place to collect the kanban cards for items needing replenishment. It helps managers and workers visualize the production schedule by making it clear what needs to be made and when.
A worker at the first step in the production process would only have to walk to the heijunka box and grab the next kanban card to know what to produce next.
While heijunka has long been part of the kanban approach, it is only a step in your journey and should not be the ultimate goal, as we explain in our blog on the problem with heijunka.
In short, you can use a heijunka box, but don't rely too heavily on the idea of smoothing out production to the point that you smooth it out over long horizons. Heijunka is best used on the micro level to keep your line running smoothly.
Kanban supermarkets
The kanban supermarket sits at the end of each production line, at the point where no more decisions must be made about the order of production. This can be right before final assembly, or it can be the point where packing begins.
Widgets are placed in the supermarket with their kanban cards. When a worker pulls a widget from the supermarket, they send the kanban card back to the very start of the production process.
You can view the supermarket as the origin of the kanban cards. Because this is a pull system, the trigger for more production is the demand signaled by the product being pulled toward the customer.
Is kanban right for you?
If you’re already thinking Lean and implementing a pull system, then kanban aligns with your goals.
The closer you are to single piece flow, the easier it will be to implement kanban. This doesn’t mean that you should give up just yet if you are still battling WIP inventory. In fact, this system will help you manage that by clearly showing where batches are piling up and requiring your production to level out so that nothing moves without a card.
It is also a good idea to implement kanban when you use the same parts across multiple products, because the supermarket system works great for making sure you’re only producing the parts you need while making final assembly easier.
Alternatives to kanban
There are some alternatives to kanban which are also pull-oriented production systems. The most notable of these are constant work in progress (CONWIP) and drum-buffer-rope (DBR).
CONWIP is like a single-card kanban system in which cards are not specific to widgets, but rather indicate the quantity that can be produced at any time. It is a way of limiting the amount of work in progress without strictly limiting it to specific product variations as they are pulled from the final workstation. The backlog is prioritized outside of the CONWIP card system, and the next item to be produced is assigned to a card right before the card enters the system.
In DBR, there are not necessarily any cards. Rather, this method relies on each workstation watching for empty space after their station, then producing more to keep the buffer at the desired level. Some stations will not have a buffer, since the main goal of the DBR method is to keep the bottleneck of the production process constantly fed so that production continues uninterrupted.
How to get started with kanban
To get started with kanban, you will need to purchase some bins and a rack for your supermarket, buy or build a heijunka board, buy or create kanban cards, and have places at each workstation for the cards so they can move with the items they represent.
You will also need to train your team on how this system works, then monitor as workers implement the system and make it part of their routine. Make corrections as needed and be sure to make rounds regularly on the floor to catch any opportunities for improvement.
If this all sounds intimidating, we feel your pain, because some of us at Veryable have been in your shoes before. Veryable’s team includes many former operations leaders with real-world experience who can walk you through this process.
For more information, visit our Lean Center of Excellence Homepage or our homepage for Continuous Improvement, Operational Excellence, and Lean Professionals.
Previous Posts
The First Step to Faster Fulfillment: Mastering Dock-to-Stock Cycle Times
The Future of Manufacturing and Logistics
Create a free business profile today to explore our platform.
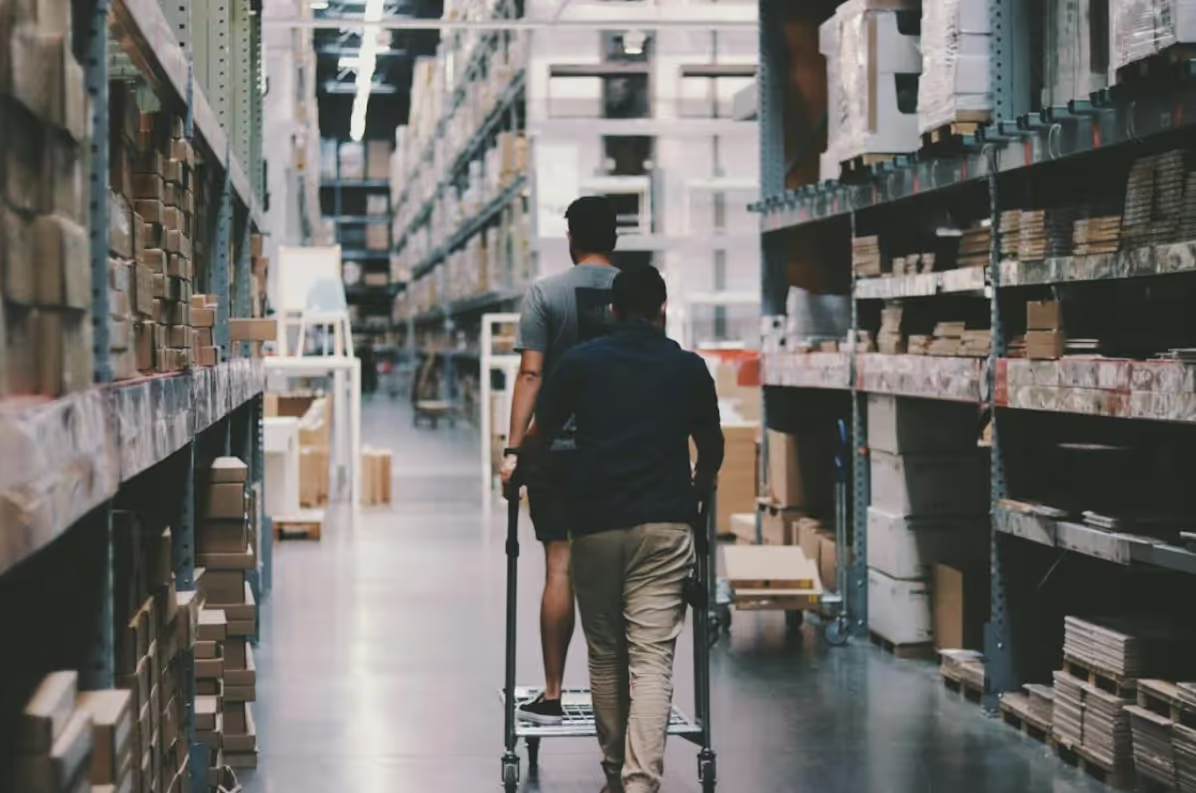