How Consumer Packaging Companies Can Win Q4 With Operational Flexibility
For consumer packaging manufacturers, Q4 isn’t just another quarter — it’s the ultimate pressure test. As retailers roll out aggressive promotions and brands accelerate seasonal launches, demand for packaging surges across multiple channels. Add in the explosive growth of e-commerce and the need for faster fulfillment, and the result is a volatile, high-stakes operating environment where delays at any stage — from line feeding to final shipment — can ripple across the entire supply chain.
The pace is relentless. Order volumes climb sharply, product mixes change frequently, and customer expectations around speed, accuracy, and presentation are higher than ever. Lead times shrink as retailers compress delivery windows, while SKU complexity and customization demands continue to rise.
In this climate, success hinges on how quickly and precisely you operation can respond. Whether you're producing limited-run seasonal SKUs, scaling late-stage customization for omnichannel distribution, or replenishing high-velocity retail displays, real-time capacity adjustments are no longer a luxury — they’re essential. The manufacturers who outperform during peak season aren’t just planning ahead — they’re dynamically flexing resources to meet demand as it evolves, shift by shift and line by line.
The Problem with Seasonal Hiring & Temp Agency Labor
Many packaging manufacturers still lean on seasonal hiring cycles or fixed third-party labor contracts to prepare for peak periods. While these approaches might have worked in the past, they weren’t designed for today’s highly variable, high-velocity market conditions—where order volumes shift daily, lead times tighten, and demand signals change without warning.
The result? Static labor strategies that fail to align with dynamic production needs.
1. Slow Ramp-Up = Lost Throughput
Traditional seasonal hiring is slow by design. Between sourcing, background checks, and onboarding, it can take weeks to get workers trained and productive. By the time they’re up to speed, your peak may already be passing. During that lag, packaging lines fall behind, QA queues build up, and ship dates start slipping—hurting both client satisfaction and future order volume.
2. Fixed Headcount Drains Agility
Overhiring in anticipation of peak demand locks you into high labor costs before volume materializes. And when demand shifts—whether due to retailer pullbacks, supply delays, or SKU mix changes—you’re left with idle workers who can’t easily be reassigned across workflows. That inefficiency directly impacts margins.
3. Overtime Leads to Errors
When your core workforce is stretched thin, overtime becomes the default lever. But extended hours quickly lead to fatigue, slower cycle times, and higher error rates—especially on detailed tasks like kit assembly, labeling, or final inspection. Not only do costs rise, but product quality can also take a hit at the exact moment your brand visibility is peaking.
4. Bottlenecks in Critical Processes
Q4 pressure reveals weak points in packaging operations—from line feeding and component staging to shrink wrapping, palletizing, and shipping. These workflows depend on precise handoffs and balanced throughput. Without the ability to add capacity to the exact function where bottlenecks emerge, production backs up, rework piles on, and WIP inventory stalls just when you need maximum velocity.
A More Agile Approach
Your packaging operation has evolved — leaner inventory models, tighter turnaround times, and greater complexity across SKUs. But if your workforce model is still stuck in the past, it’s going to drag everything else down.
Veryable’s on-demand labor model gives packaging manufacturers the flexibility to align labor with actual real-time demand — not forecasts that typically miss the mark. With access to thousands of high-performing, pre-vetted operators in just clicks, you can scale capacity by line, shift, or department on a daily basis. No long hiring cycles. No overcommitting. No sunk labor costs.
Instead of reacting to volume spikes or getting buried in overtime, your team moves proactively — keeping throughput high, protecting margins, and delivering on-time — at all times.
Before Peak: Build Capacity Without Overcommitting
As Q4 ramps up, brands begin pushing inventory and accelerating seasonal orders. With Veryable, you can bring in operators for specific roles — like kitting, assembly, labeling, or staging — without committing to full-time headcount or tying up budget before revenue lands.
This allows you to:
- Accelerate dock-to-line cycle times
- Prep promotional SKUs and retail bundles faster
- Add support where it’s needed, without carrying excess labor
The result? You stay lean, nimble, and margin-aware — even in the face of early volume surges.
During Peak: Scale in Real Time to Keep Lines Moving
When every shift counts and your packaging lines are under pressure, flexibility is everything. Veryable makes it possible to deploy additional capacity with less than a day’s notice — to the exact work areas that need it.
This helps you:
- Relieve bottlenecks in QA, packing, and material handling
- Flex shifts and schedules without overextending full-time staff
- Prevent late orders, excessive overtime costs, and FTE burnout
The result? you keep production flowing at full velocity and meet customer expectations without compromise while simultaneously controlling costs.
After Peak: Scale Down Smoothly Without Disruption
Post-peak, many manufacturers face the same challenge: too much labor and not enough work. Veryable allows you to scale back efficiently, so you’re not paying for idle time — while still maintaining enough capacity to support rework, returns, restocking, and final shipments.
You avoid abrupt layoffs, protect team morale, and keep your operation right-sized as volume normalizes — all while controlling cost-per-unit through the finish line.
Common Work Performed by Veryable Operators in Packaging
- Kitting & assembly
- Packaging line support
- Quality inspection
- Shrink wrapping & labeling
- Material handling
- Order prep and staging
- Rework and returns processing
To learn more about what kinds of work Veryable operators can perform, and how much you'd need to pay them to be competitive in your market, click here.
Real World Example:
A packaging company operating in the health & beauty sector needed to prepare for a major Q4 push tied to national retail promotions. Historically, they relied on temp agencies to scale up but were frustrated by the inflexibility, poor worker quality, and fees.
They turned to Veryable’s on-demand marketplace and built a bench of pre-vetted workers to support everything from kitting and assembly to quality checks and end-of-line packaging. By gaining the ability to flex headcount daily to align with demand, they were able to:
- Cut overtime by 52% while simultaneously taking on 17% higher volume than prior year
- Maintain a 99.2% on-time delivery rate during their busiest six weeks
Conclusion
In consumer packaging, Q4 is the season where operational performance makes or breaks customer relationships. It’s not enough to plan ahead — execution must be fast, flexible, and flawless. Yet traditional staffing models leave manufacturers boxed in: slow to adapt, burdened with fixed costs, and vulnerable to volatility.
Veryable empowers packaging operations to break out of that cycle. By building an on-demand labor pool, you can scale your workforce with precision — adding capacity exactly where and when it’s needed, and pulling back just as efficiently. This isn’t about filling shifts; it’s about unlocking a level of operational agility that traditional staffing simply can’t deliver.
The result? Higher throughput & OEE, reduced costs, and better service at every stage of the season. Whether you’re ramping up for promotional SKUs, maintaining flow during peak, or managing post-holiday returns and rework, Veryable gives you the control to outperform competitors — and the resilience to carry that momentum into the new year.
Previous Posts
How 3PLs Can Hit Peak Season KPIs Without Overstaffing or Burnout
The Future of Manufacturing and Logistics
Create a free business profile today to explore our platform.
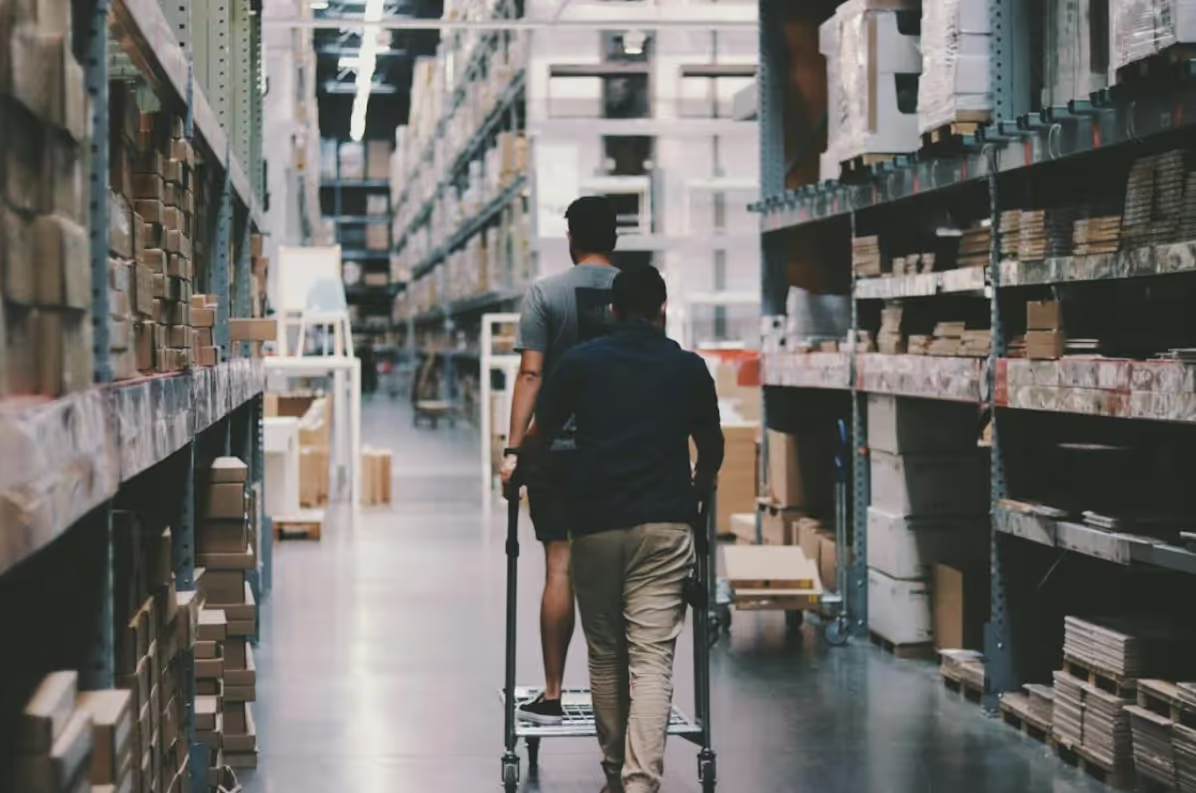