On-Demand Labor for the Automotive Industry
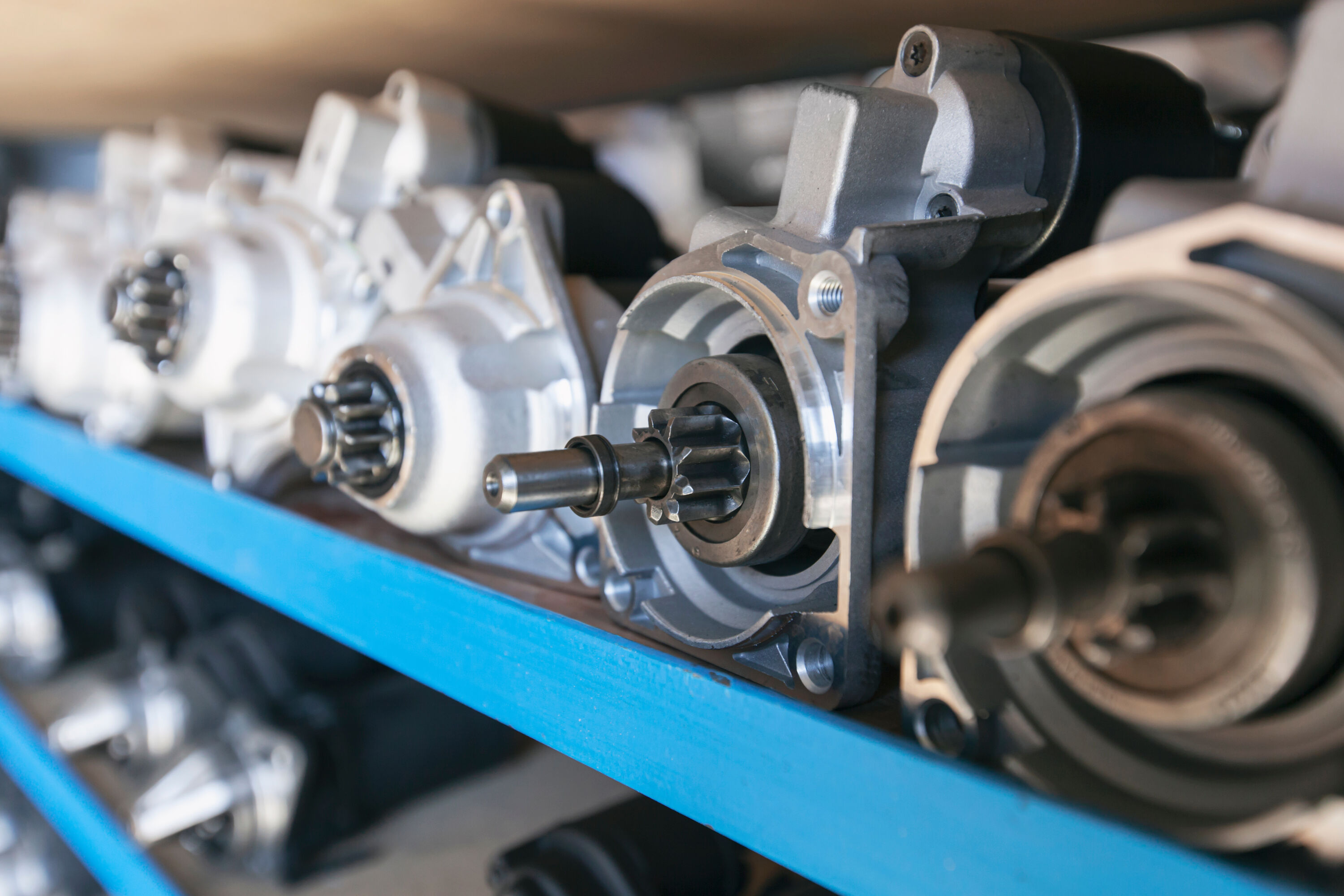
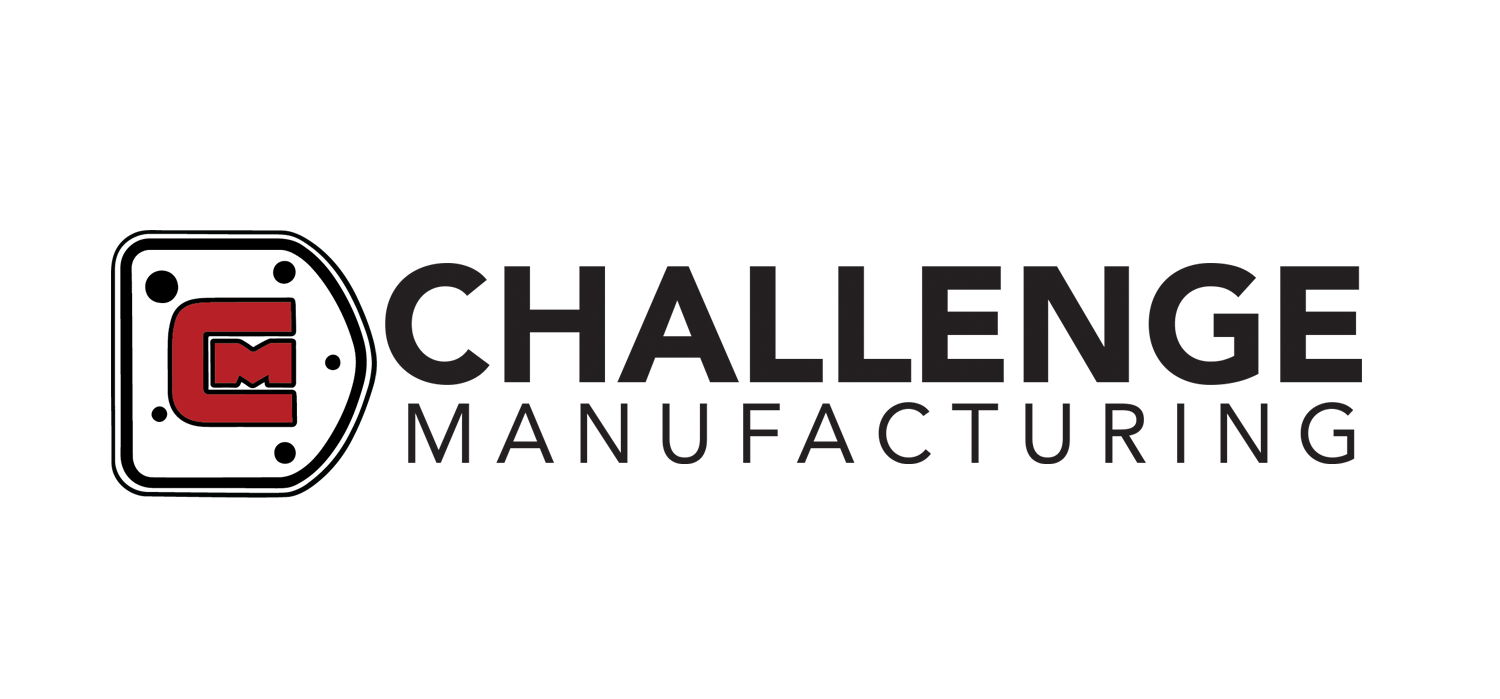
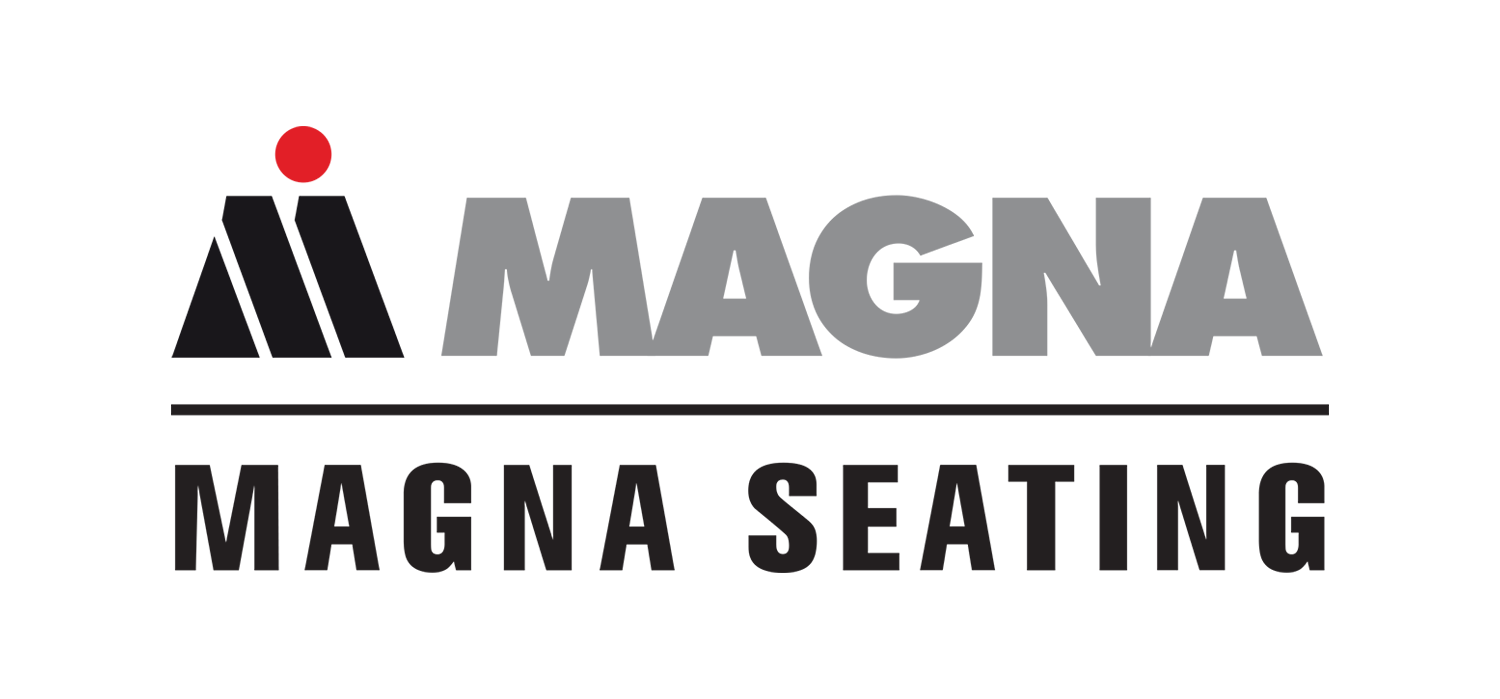
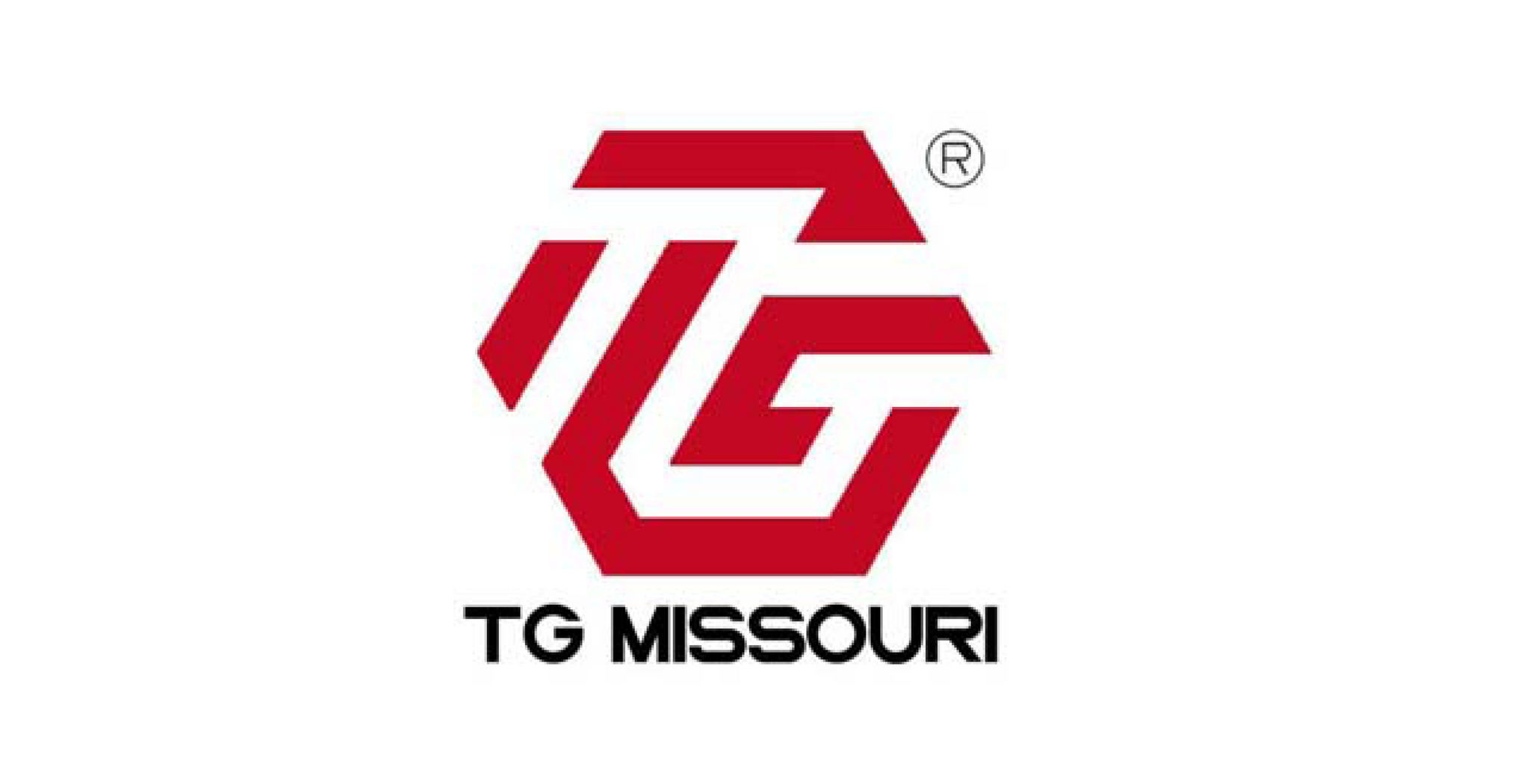

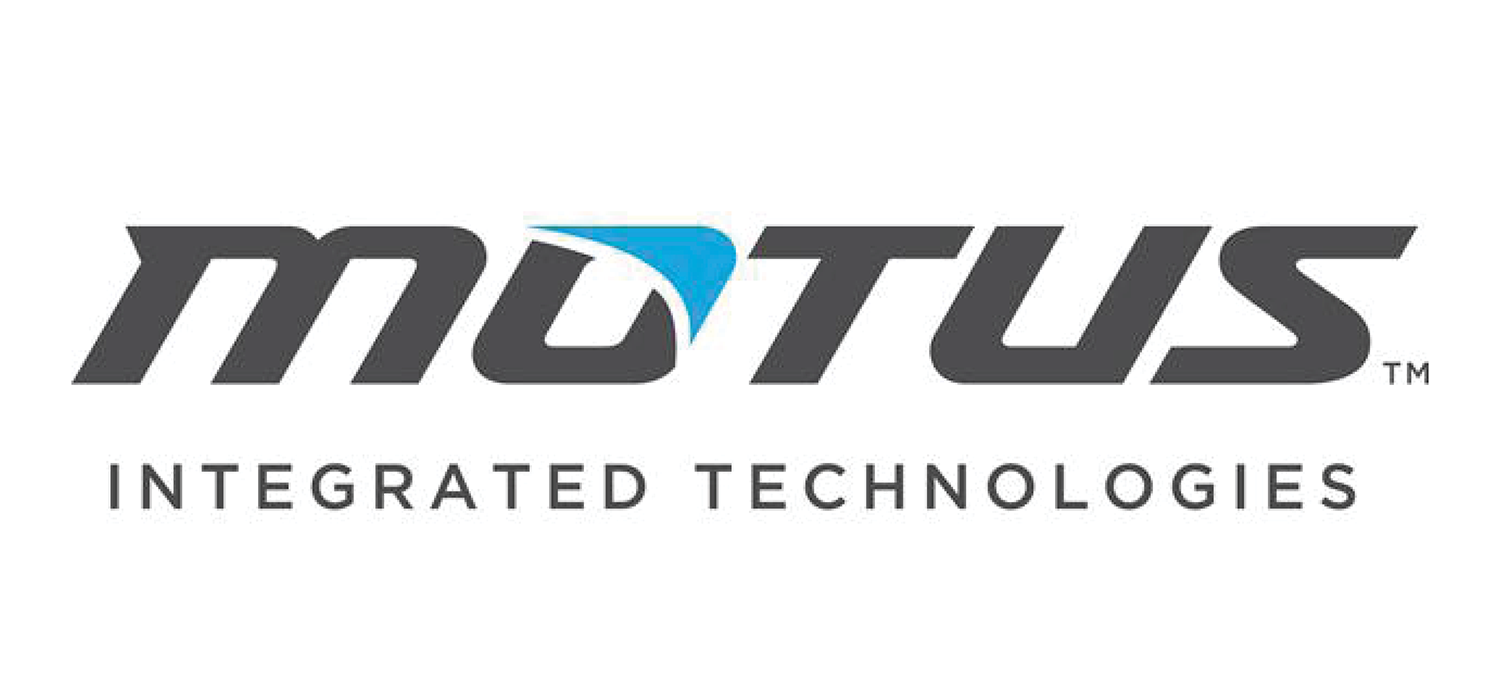
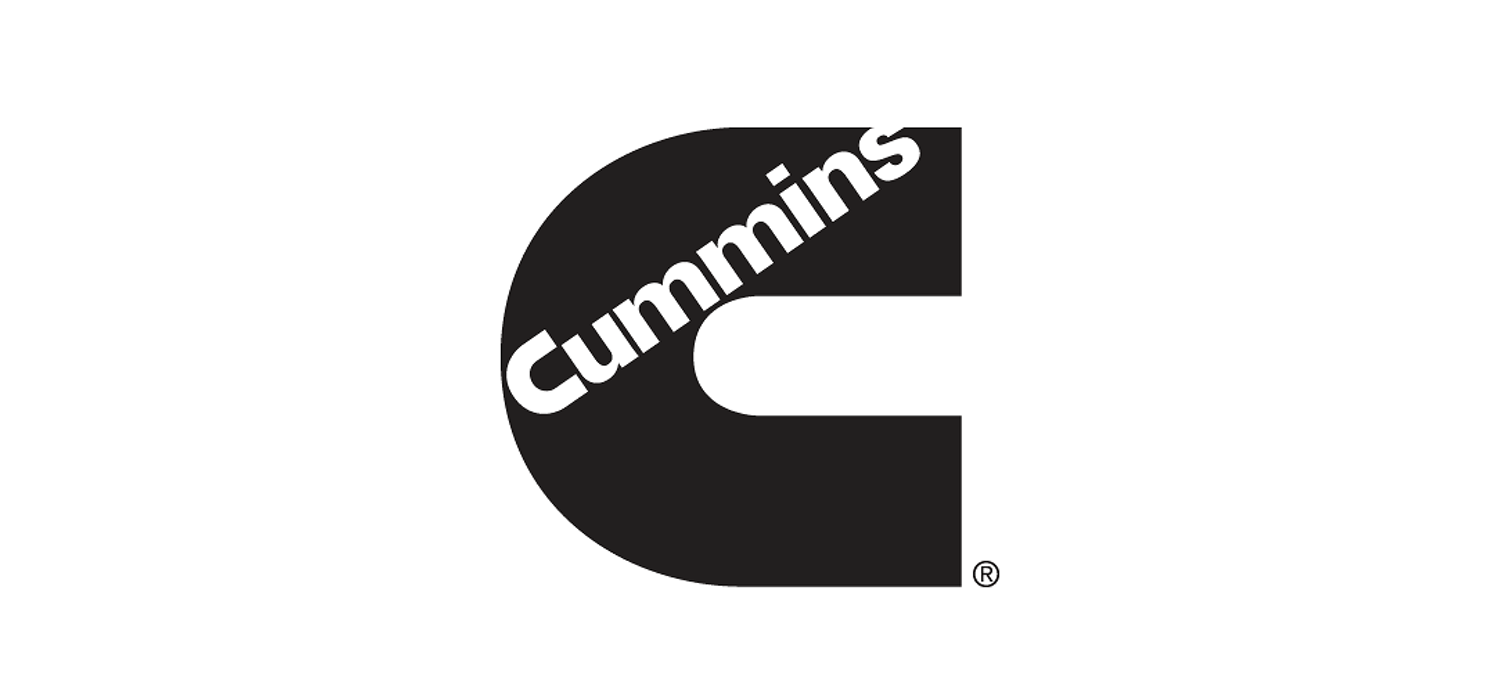
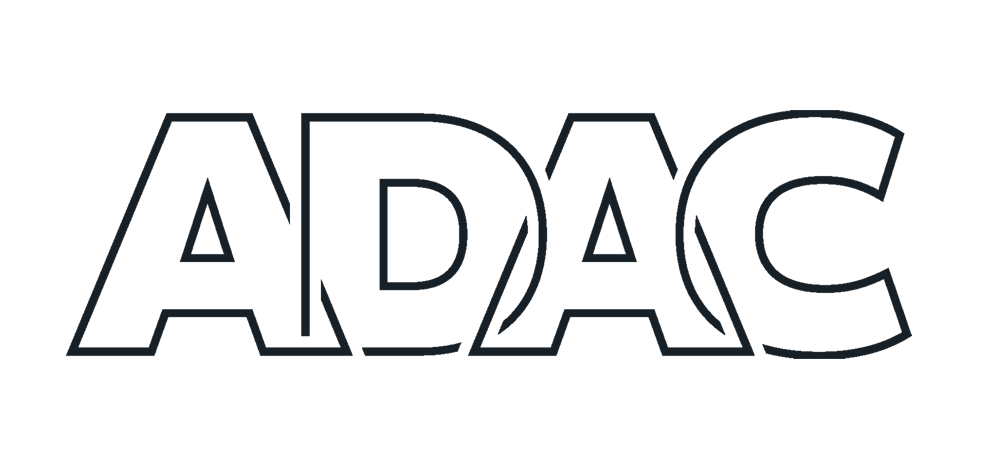
The automotive industry has quickly become the fastest growing segment at Veryable, as automotive part suppliers and manufacturers across the country are ditching the old way of doing things, and leveraging a new labor paradigm that allows them to adjust their capacity instantaneously and at the click of a button to address fluctuating and unpredictable customer demands. Our on-demand marketplace for warehousing, logistics, and manufacturing labor connects businesses with high-quality workers at the click of a button, enabling businesses to create a flexible extension of their fixed workforce called a labor pool. Building your labor pool enables higher productivity and a competitive edge. For workers, Veryable provides immediate access to work, the ability to control their own schedule, opportunities to build new skills, and best of all, next-day pay. Gain the capacity you need, exactly when you need it. When you build a labor pool with on-demand labor, you’ll have both the confidence and the unlimited flexible capacity to take on anything that comes your way. That's how you reach new levels of efficiency and productivity and gain an edge on your competition. Veryable is about more than labor, it is the operational strategy - developed by ops leaders and for ops leaders, that is driving businesses forward. As we continue to enhance our approach to better meet the specific requirements of the automotive industry, our commitment remains steadfast in delivering unparalleled solutions for operational streamlining, increased productivity, and enhanced on-time delivery rates. Make. Your Way
MFG Day 2023
In this years virtual webinar we sit down with team members from ADAC Automotive, Antolin, Feniex Industries, Metal Flow Corporation, as well as industry veterans and Veryable team members Derek Ochodnicky and Ty Morgan to talk about their experiences and passion for the Automotive industry.
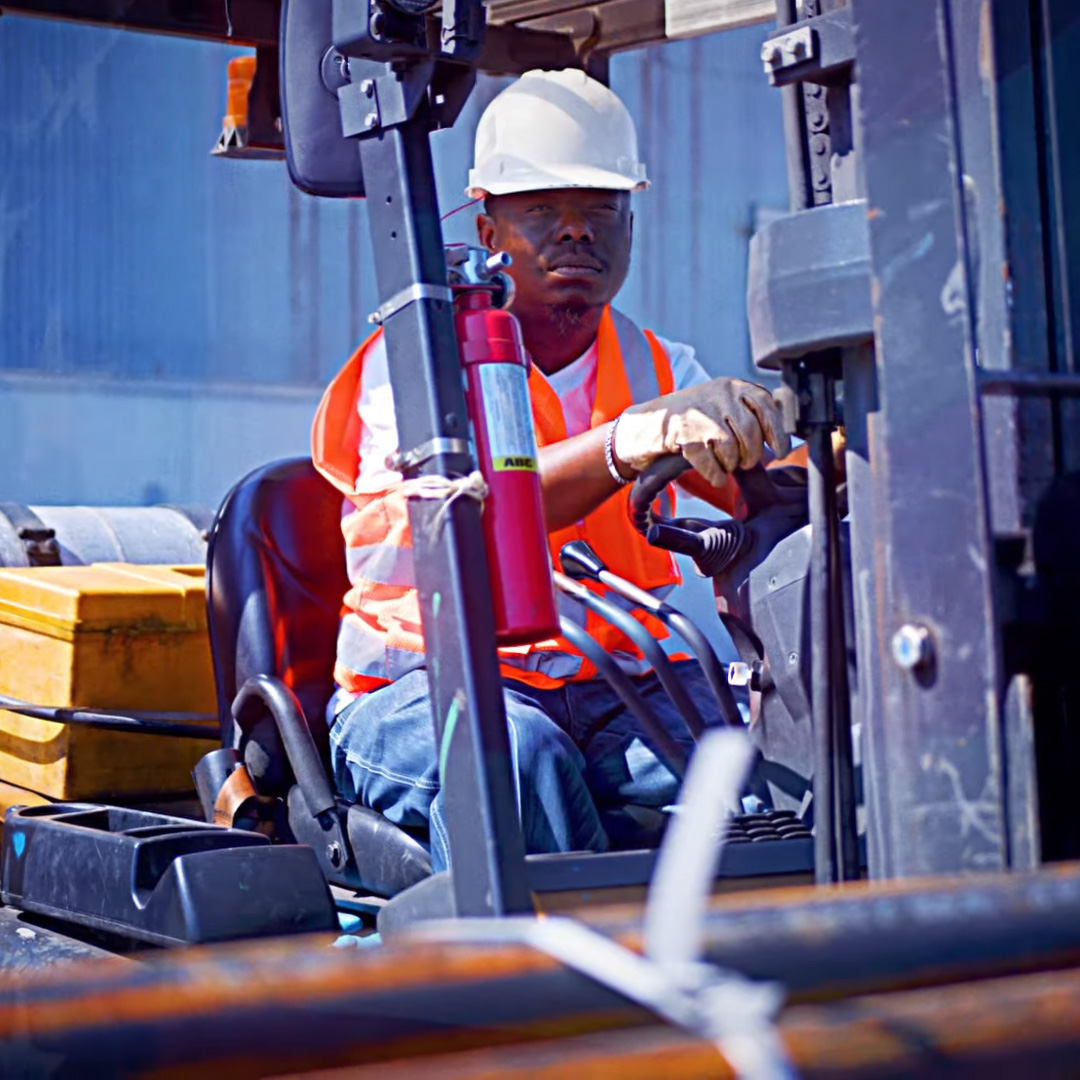
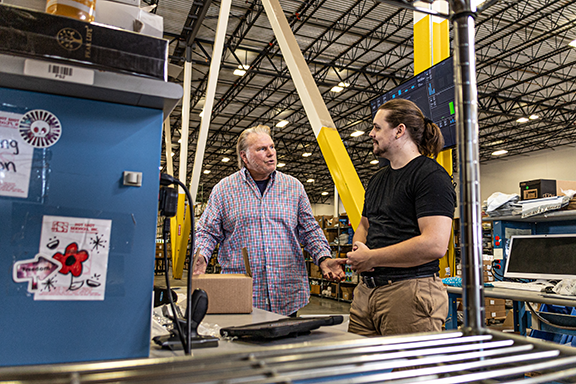
What Can You Do with Veryable?
Respond quickly to changes in demand rather than relying on guesswork. Find workers fast, pay only when they work, and unlock your potential with infinite flexibility.
1. Zero cost to scale
2. Fewer administrative burdens
3. Step-level improvements in cost structure
4. Fast response to labor demand volatility
Case Studies
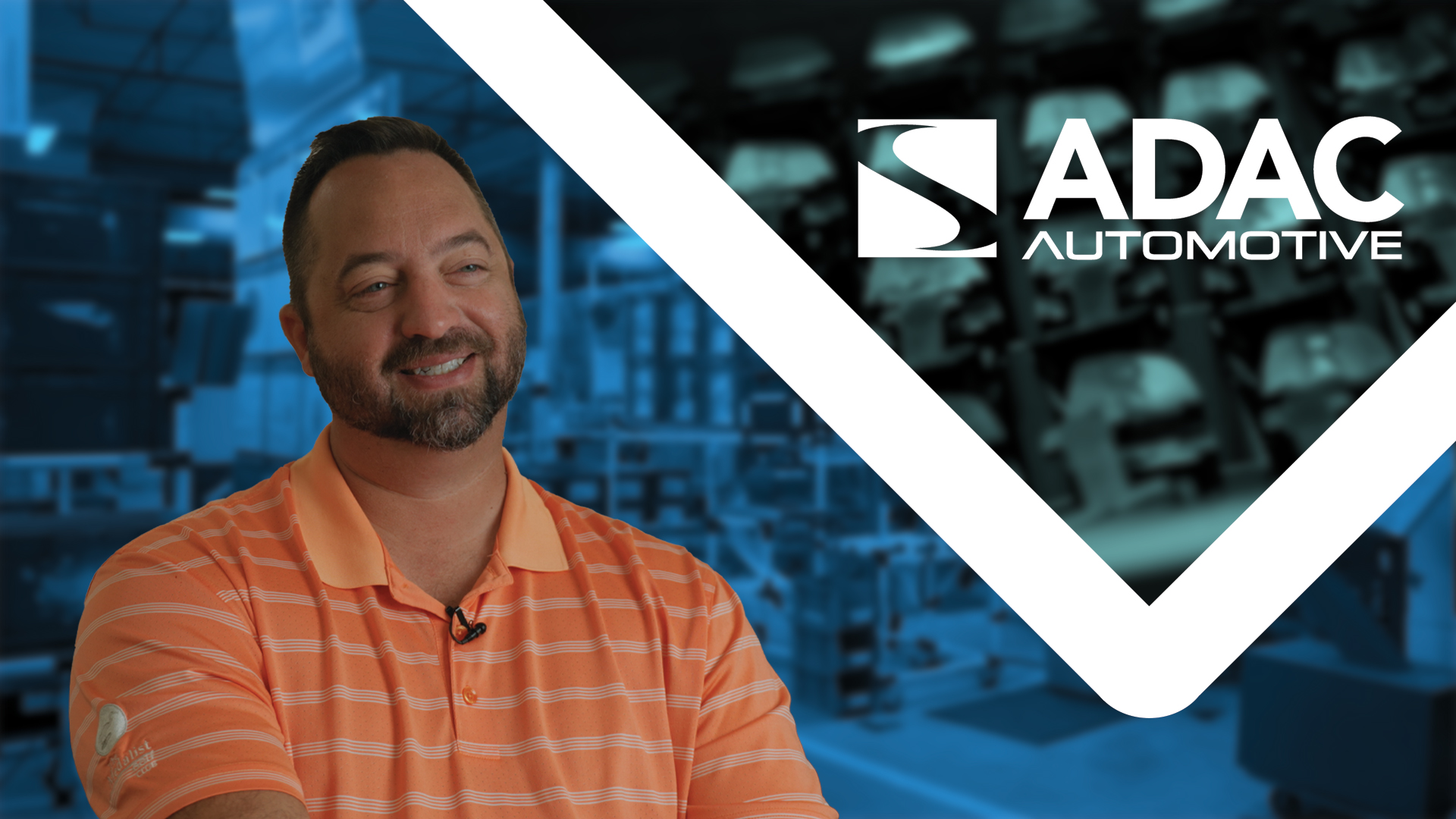
ADAC

Metal Flow
.png)
Intertech Products
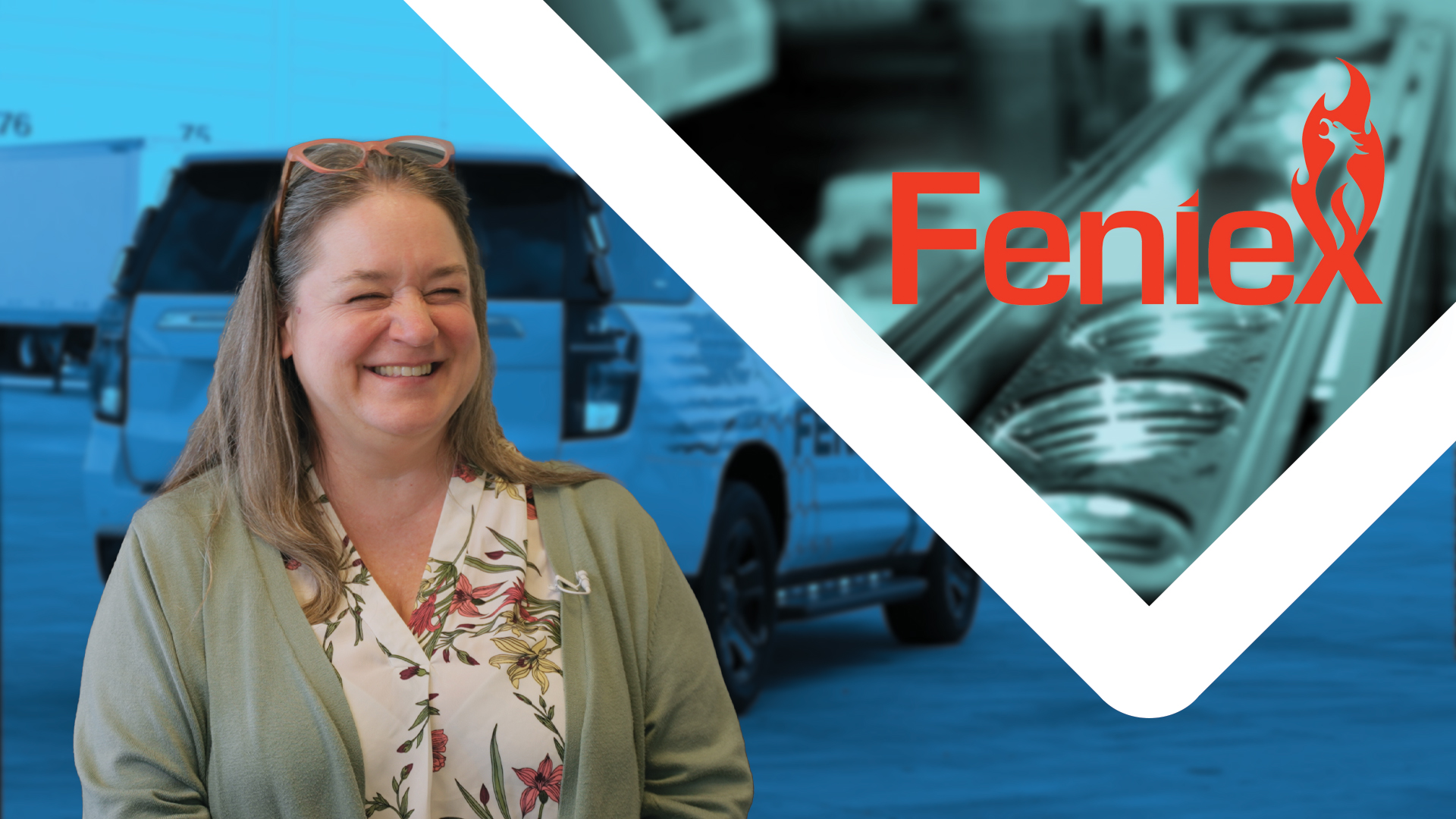
Feniex Industries
Learn More About On Demand Labor
Explore our industry resources for valuable insights.
How Consumer Packaging Companies Can Win Q4 With Operational Flexibility
How 3PLs Can Hit Peak Season KPIs Without Overstaffing or Burnout
The Future of Manufacturing and Logistics
Create a free business profile today to explore our platform.
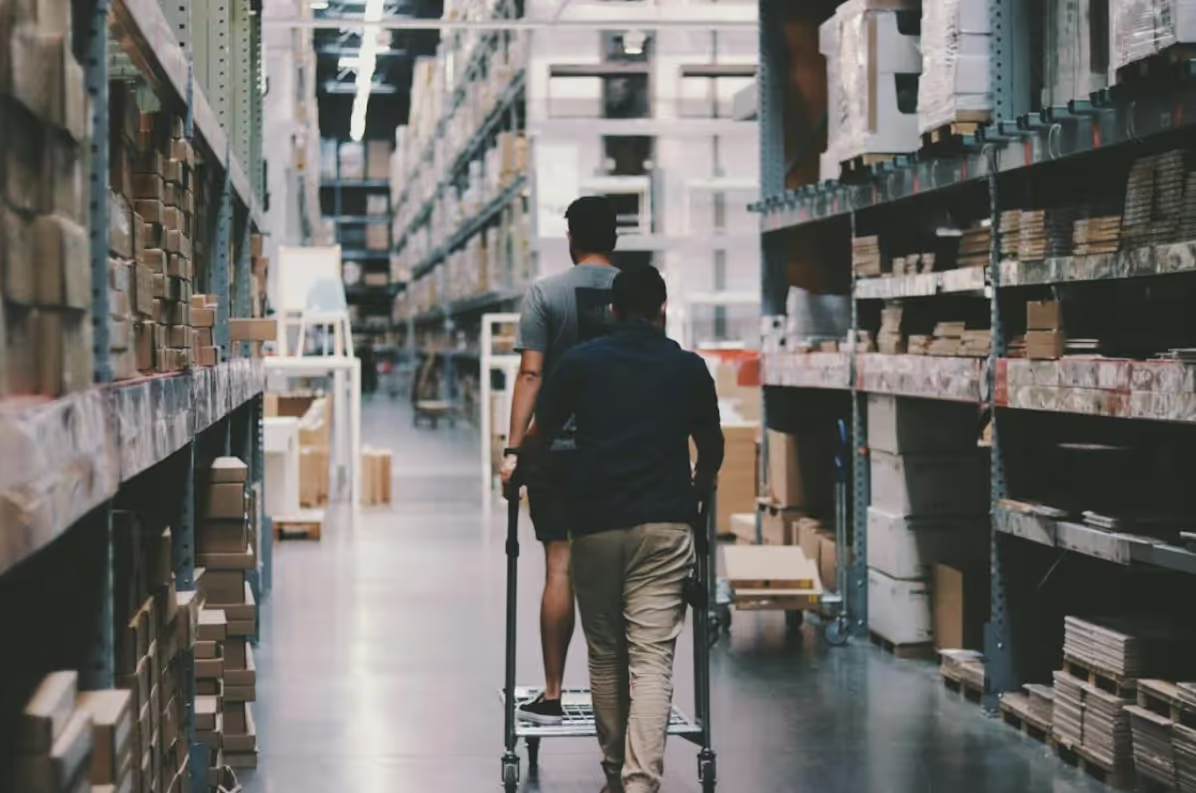