Understanding OEE: A Key Metric for Operational Excellence
In today’s fast-paced manufacturing and distribution landscape, Overall Equipment Effectiveness (OEE) stands as a cornerstone metric that encapsulates the true productivity of your equipment. Unlike isolated measurements, OEE provides a holistic view by combining availability, performance efficiency, and quality output into one comprehensive KPI.
OEE answers the essential question for operations leaders: How effectively is your equipment converting scheduled time into quality products? High OEE means your machinery is running when it should, operating at optimal speed, and producing defect-free goods—directly translating to increased capacity, lower costs, and stronger customer satisfaction.
Conversely, low OEE highlights hidden losses—whether from unplanned downtime, reduced speed, or quality issues—that erode production capability and impact your bottom line. By tracking and improving OEE, manufacturers and distributors can pinpoint inefficiencies, prioritize improvements, and ultimately drive greater operational excellence.
In this article, we’ll break down what OEE measures, why it’s crucial for your business, and practical steps to boost your equipment effectiveness and overall profitability.
Understanding the OEE Formula
Overall Equipment Effectiveness (OEE) is a comprehensive metric that quantifies how efficiently a manufacturing asset or production line is performing relative to its full potential. At its core, OEE is calculated as the product of three key factors:
OEE = Availability × Performance × Quality
Each component represents a critical aspect of equipment effectiveness and highlights specific areas for operational improvement:
- Availability measures the percentage of scheduled production time that the equipment is actually running. It accounts for downtime caused by equipment failures, setup and adjustments, or any other events that prevent the machine from operating as planned. Maximizing availability means minimizing unplanned stoppages and ensuring equipment is consistently ready to run.
- Performance assesses how fast the equipment operates relative to its designed maximum speed. Even when equipment is running, it may not be operating at peak efficiency due to slow cycles, minor stops, or suboptimal operating conditions. Performance quantifies this speed loss, emphasizing the importance of maintaining optimal run rates.
- Quality reflects the proportion of products manufactured that meet quality standards without requiring rework or resulting in scrap. High quality means that a large majority of output is sellable, reducing waste and the costs associated with defects or returns.
For example, consider a production line with 90% availability, 95% performance, and 98% quality. When these factors are multiplied together, the resulting OEE is approximately 83.8%. This figure provides a unified view of equipment effectiveness that goes beyond simple output numbers, revealing inefficiencies that might otherwise remain hidden.
By analyzing each element individually and as part of the overall OEE, manufacturers can pinpoint whether losses are driven primarily by downtime, speed reductions, or quality issues—enabling targeted strategies that improve productivity, reduce costs, and enhance delivery reliability.
Why OEE Matters for Manufacturing Operations
Overall Equipment Effectiveness (OEE) offers manufacturers a powerful lens into the true efficiency of their production processes by precisely pinpointing where productivity losses occur. Rather than relying on aggregate output figures or isolated metrics, OEE breaks down inefficiencies into three distinct categories—downtime, reduced speed, and quality defects—providing actionable insights into the root causes of lost production capacity. This granular visibility enables companies to transition from reactive firefighting to a proactive, data-driven approach focused on continuous improvement.
Beyond its diagnostic capabilities, OEE serves as an invaluable benchmarking and performance management tool. By consistently measuring and tracking OEE over time—and comparing scores across different production lines, shifts, or facilities—manufacturers gain clarity on operational trends and variability. This empowers leadership to set realistic, measurable performance targets, prioritize investments, and allocate resources effectively. As a result, operational excellence moves from an abstract goal to a quantifiable and attainable standard.
The financial implications of improving OEE are significant and immediate. Enhancements in equipment availability, performance, and quality directly translate into reduced waste, higher throughput, and greater profitability—often without the need for costly capital expenditures. Even modest improvements of a few percentage points in OEE can yield substantial returns by maximizing the utilization of existing labor, materials, and machinery. In today’s competitive market, leveraging OEE as a strategic KPI helps manufacturers optimize asset performance, shorten lead times, and strengthen customer satisfaction—ultimately driving sustainable growth and long-term success.
Setting the Benchmark: What’s a “Good” OEE Score?
World-class Overall Equipment Effectiveness (OEE) is generally recognized as 85% or higher—a level that represents near-perfect performance across availability, performance, and quality. However, achieving and consistently maintaining this benchmark remains a significant challenge for most manufacturing and distribution facilities.
In reality, many well-managed operations report OEE scores ranging between 60% and 70%. This range reflects common operational realities, including unplanned downtime, minor speed losses, and quality issues that are difficult to eliminate entirely. Reaching world-class OEE requires not only robust systems and processes but also disciplined execution and close alignment among cross-functional teams.
Understanding where your facility stands on this OEE spectrum is critical. If your score falls below 60%, it may indicate significant losses that need immediate corrective action. Scores between 60% and 85% suggest a mix of opportunities—addressing obvious inefficiencies while also refining and optimizing existing processes. For organizations already nearing or exceeding the 85% mark, the focus shifts toward continuous improvement and innovation to sustain and advance their competitive advantage.
By benchmarking your OEE performance realistically, you can set targeted goals, prioritize improvement efforts, and track progress with greater clarity—turning OEE from an abstract metric into a powerful tool for operational excellence.
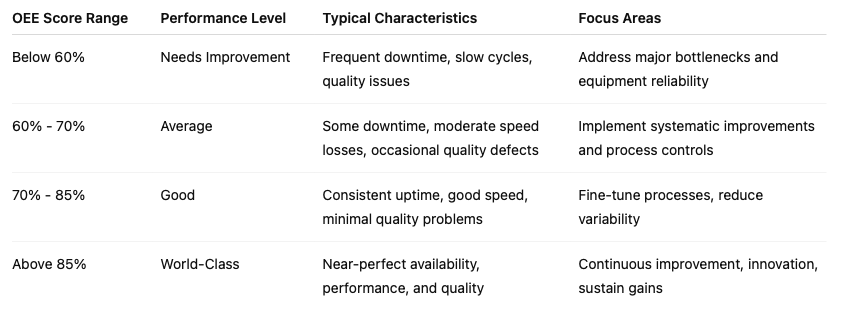
Common Challenges in OEE Implementation
While the concept of Overall Equipment Effectiveness (OEE) is straightforward, successfully implementing an OEE program often presents significant challenges. One of the most prevalent obstacles is the lack of real-time, accurate visibility into equipment performance. Many manufacturers still rely on manual data collection methods that are prone to delays and inaccuracies, limiting their ability to respond swiftly and precisely to production issues. Without timely data, identifying and addressing the root causes of inefficiencies becomes difficult, hindering continuous improvement efforts.
Cultural resistance within organizations can also impede effective OEE adoption. There is often an overemphasis on improving the aggregate OEE score rather than understanding and addressing the specific underlying losses driving that score. This focus on surface-level metrics can lead to short-term or cosmetic improvements that inflate OEE figures without resolving systemic problems, resulting in stagnation or backsliding over time.
Furthermore, many teams struggle with fully grasping the six distinct types of production losses that OEE is designed to uncover. These losses are traditionally grouped into three main categories:
- Availability losses: Unplanned downtime such as equipment breakdowns and planned stops like changeovers or setup times.
- Performance losses: Minor stoppages, brief interruptions, and running equipment below its optimal speed.
- Quality losses: Production of defective units and rejects during startup or stabilization phases.
Effectively identifying and systematically addressing each of these loss types is essential for achieving sustainable improvements in OEE. This requires not only accurate data collection but also a culture of accountability, cross-functional collaboration, and a commitment to continuous operational excellence.
Best Practices for Driving OEE Improvement
Driving meaningful improvements in Overall Equipment Effectiveness (OEE) begins with reliable, real-time data. Manufacturers who invest in automated monitoring and data collection systems gain immediate visibility into equipment performance, enabling faster identification and resolution of issues while eliminating the inaccuracies and delays inherent in manual data entry.
With accurate data in hand, it becomes possible to focus efforts on the most significant sources of waste. Applying Pareto analysis helps prioritize whether downtime, reduced speed, or quality defects are having the greatest impact on OEE—allowing teams to target interventions where they will yield the highest returns.
Equally important is fostering a culture of continuous improvement across the organization. Regular cross-functional reviews of OEE data, clear and measurable goal-setting, and comprehensive staff training on OEE principles empower teams to engage proactively in identifying and addressing inefficiencies.
Preventive maintenance also plays a critical role in sustaining high OEE. Leveraging predictive maintenance tools and proactive scheduling minimizes unexpected breakdowns, maximizing equipment availability and ensuring smoother production flow.
By combining reliable data, strategic focus, a culture of collaboration, and robust maintenance practices, manufacturers can unlock sustained gains in OEE that drive operational excellence and competitive advantage.
Enhancing OEE Through Workforce Agility with Veryable
While equipment effectiveness often receives the most attention, workforce availability plays an equally crucial role in driving Overall Equipment Effectiveness (OEE). Gaps in operator coverage—whether due to absenteeism, inflexible schedules, or skill shortages—can negatively impact all three components of OEE. Production slows, quality suffers, and downtime extends beyond necessary limits.
Veryable’s on-demand marketplace bridges this gap by providing manufacturers with real-time access to skilled operators, assemblers, and support personnel. This flexibility allows you to scale your workforce capacity with the same responsiveness you expect from your equipment. When machines are ready but operators aren’t, availability drops. When experienced workers are overstretched, performance declines. When fatigued teams push through critical tasks, quality diminishes. Veryable helps prevent these scenarios by aligning workforce capacity directly with your production demands.
Achieving lasting improvements in OEE requires more than data and diagnostics—it demands operational agility. Veryable supports your efforts by removing the unpredictable element of workforce constraints. You gain the ability to seamlessly augment your team during peak periods, cover unexpected absences, and efficiently manage changeovers without overburdening permanent employees.
With real-time workforce management tools, predictive scheduling capabilities, and a pool of vetted professionals, Veryable empowers you to control one of the most variable factors in manufacturing—your workforce. This enhanced agility helps maximize equipment uptime, maintain optimal performance speeds, and uphold product quality, driving sustained gains in overall operational effectiveness.
Conclusion
In today’s dynamic manufacturing and distribution landscape, Overall Equipment Effectiveness (OEE) is a vital metric that reveals how efficiently your equipment turns scheduled time into quality output. By breaking down availability, performance, and quality, OEE helps leaders pinpoint inefficiencies and focus improvement efforts that drive operational excellence.
Enhancing OEE boosts throughput, reduces waste, and increases profitability—often without significant new investment. Success, however, depends on more than data; it requires operational agility, including the ability to adjust workforce capacity in real time to support production demands. Addressing these challenges enables manufacturers and distributors to improve productivity, satisfy customers, and stay competitive.
Veryable complements these efforts by providing flexible, immediate access to skilled operators, helping manufacturers optimize equipment use and maintain quality. Click here to learn more about how flexible workforce capacity can elevate your OEE and overall performance.
This article covers how manufacturers can optimize changeovers by strategically leveraging Veryable operators: Creativity Over Capital: Changeover Reduction
Previous Posts
How Consumer Packaging Companies Can Win Q4 With Operational Flexibility
The Future of Manufacturing and Logistics
Create a free business profile today to explore our platform.
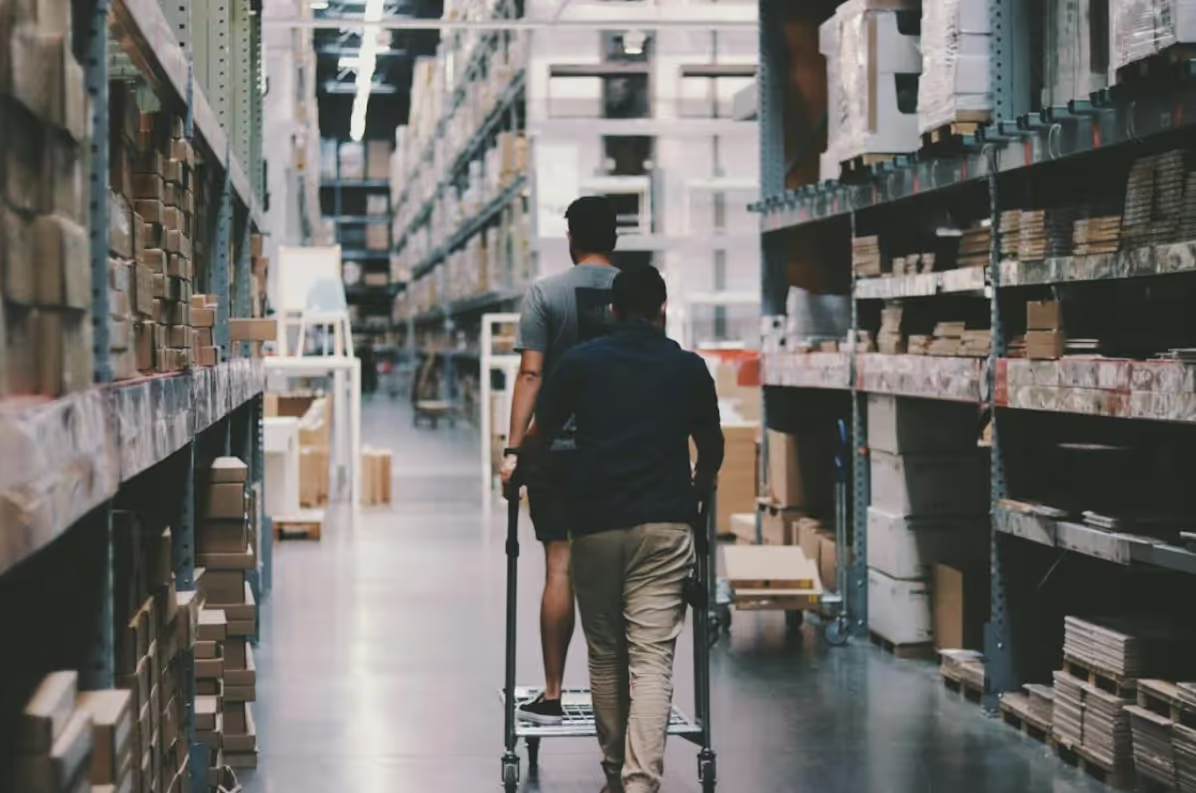