Creativity Over Capital: Changeover Reduction
The most overlooked opportunity for increasing production capacity in manufacturing plants is planned downtime. Because changeovers and maintenance are planned, we tend to accept them as normal or something that must be done. After a closer look, you may realize that these planned events are the largest contributor to your production losses. Attacking planned downtime will not only reduce inefficiencies in your operations, but more importantly let you claw back some valuable production time to increase your capacity and help grow your business.
Consider a plant that is running fifteen shifts per week and has two planned downtime events during that time. Each shift equates to about 7% of available production time. With some changeovers, cleaning or maintenance tasks taking a full shift or more, production losses add up quickly. Because changeovers are done outside of normal production, they often lack a formal process or standard work, leading to even more inefficiencies. These factors combined to make changeover reduction one of the highest impact improvement opportunities in your plant, and it’s common to see a 35-40% reduction in planned downtime with focused improvements, leading to increased uptime and overall equipment effectiveness (OEE).
Changeover time is measured from the last good part produced before the changeover begins, to the next good part produced after the changeover is completed. Tasks external to the changeover process can be completed while the equipment is still in operation; however, internal tasks must be completed with the equipment offline directly contributing to downtime. Distinguishing between internal and external tasks is a crucial step for changeover reduction, and a common strategy is to convert internal tasks to external tasks wherever possible. Then focus on optimizing the remaining internal tasks to reduce the overall length of the event.
The Veryable Solution
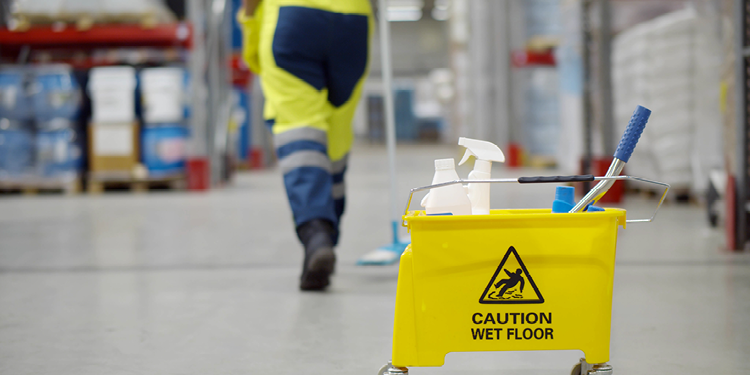
A great way to optimize internal tasks is to reallocate less skilled work to a back-up or assistant role, allowing your highly skilled mechanics and tool setters to complete their tasks in a shorter time. There are several tasks occurring during a changeover that can be performed by Veryable operators including cleaning, mopping, transporting material and tools, lubricating and other easily trainable items. Freeing your experienced crew to focus on more critical assembly, set-up and quality tasks will get your equipment back online quicker, helping regain uptime for production.
Because Veryable allows for flexible scheduling, you can choose the start time and length of an Op to fit what you need. Predicting when a production run will end and a changeover will begin is difficult, and rarely coincides with shift start and end times, so this flexibility is extremely helpful to stay on track. Veryable operators can be used as needed for a split shift or to overlap shifts helping you complete pre-work or ensure continuity during the changeover event. Additionally, this flexibility allows you to immediately start your next production run at the conclusion of the changeover, without waiting for the start of the next shift. Getting your equipment back online helps you regain production time and effectively increases your capacity.
Changeover reduction is one of the many ways continuous improvement, lean, and operational excellence leaders can employ creativity over capital to improve overall equipment effectiveness and grow your business.
To learn more, check out the other articles in this series:
Creativity Over Capital: Addressing The Skilled Labor Gap
Creativity over Capital: Growing Your Business without Capital Investment
Creativity Over Capital: Fleet Optimization for Beverage Distributors
To get started with on-demand labor, create your free business profile or contact your local team.
Previous Posts
Old Roles, New Realities - Who Owns Agility?
The Future of Manufacturing and Logistics
Create a free business profile today to explore our platform.
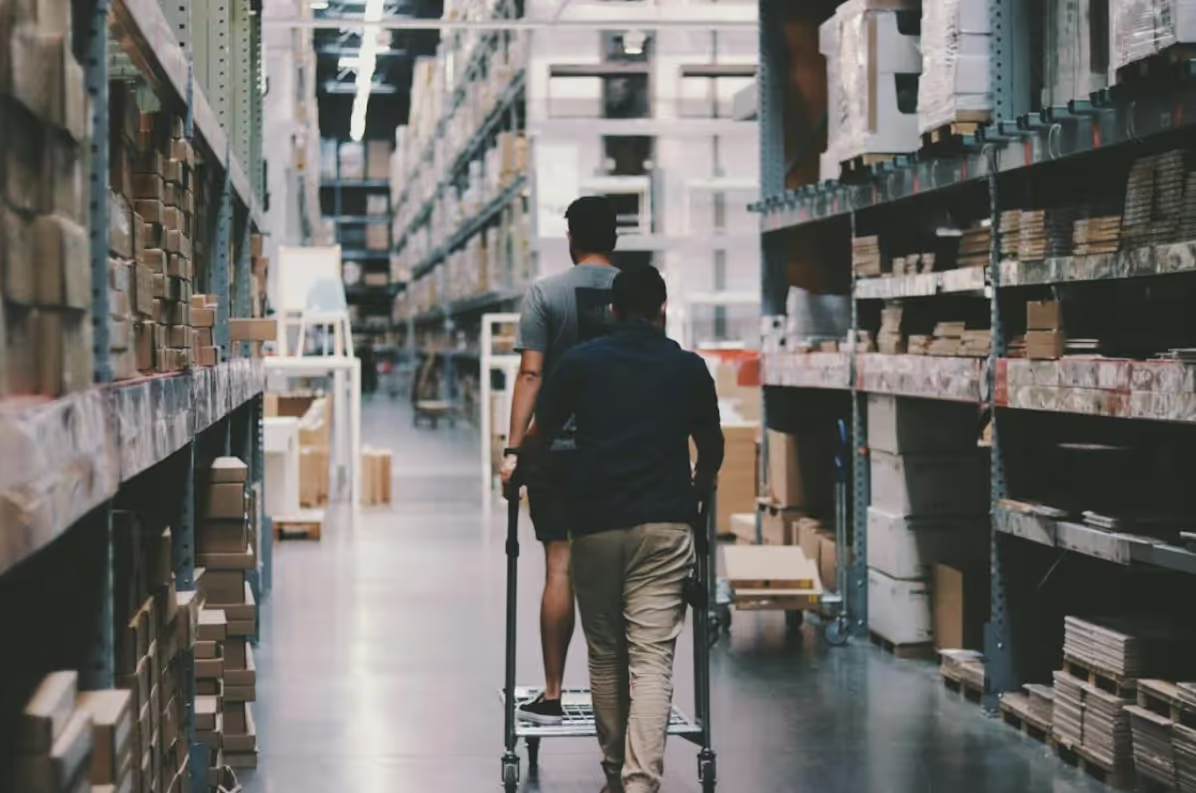