Creativity Over Capital: Addressing The Skilled Labor Gap
Reshoring and demand growth is happening at a time when the existing skilled workforce is approaching retirement. As experienced workers begin to age out of the workforce, there’s a lack of up-and-coming talent with the required skillset and experience to replace them. Manufacturers are already feeling the impact of this, both in terms of capacity constraints and increased costs for hiring and retaining workers. Many look to increased incentives to attract talent, or even capital improvements to reduce the need for workers, but a simpler and often overlooked approach is available. Eliminating waste by reallocating lower skilled work can help your organization better utilize your existing workforce, and help you upskill the next generation of workers to take their place.
High Demand and Low Supply
With an increasing number of businesses experiencing a skills gap, competition for workers is increasing. This competition is driving up wages and benefits, making it challenging for some companies to attract and retain the talent they need. Adding to the difficulty is the transition in employee priorities away from traditional incentives and towards additional flexibility, autonomy, and work-life balance. Legacy methods for recruiting and retaining employees are less and less effective for tomorrow’s workforce, and employers need to look for alternatives to remain profitable in the future economy.
Impacts on the Production Floor
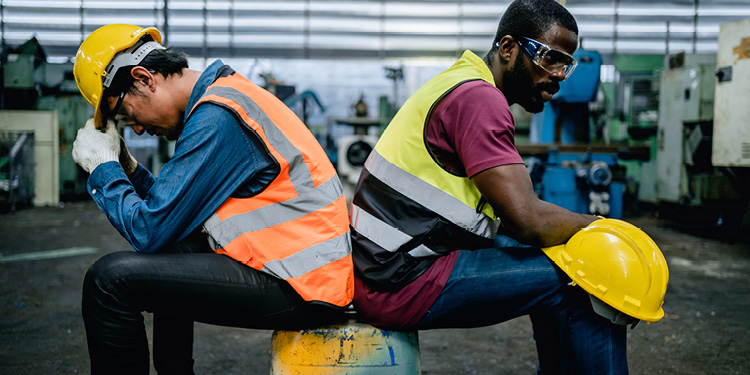
Operations leaders realize the impact of skilled labor constraints in both increased cost and lost production capacity. Without the ability to fully staff all positions, supervisors and planners are turning to longer shifts and mandatory overtime to compensate. That’s not only an expensive way to fill the gap, but it also leads to employee burnout and turnover, which only amplifies the issue. In some cases, the inability to fully staff production shifts can lead to lost production, reducing sales volume and impacting profitability.
Solving Constraints
Many manufacturers overlook the most obvious solution to their labor constraints, fully utilizing their existing workforce. While most feel their workers are already fully utilized or even over burden, closer observations will reveal that at least some of the tasks completed by highly skilled workers are low skilled or non-value added. The key to solving the skilled labor gap is reallocating less skilled and easily trainable tasks, unburdening your skilled workers, and effectively increasing their capacity. Resolving these constraints will lead to increased throughput in your processes, and improved performance for both you and your customers.
In one example, a plant had too few skilled operators to fully staff all production lines and shifts. While production equipment sat idle, this plant fell behind on customer orders. To resolve this constraint, the team focused on unburdening the limited number of machine operators to run additional production lines. Through time studies and observations, the team discovered that nearly half of the work done by machine operators during a typical shift could be completed by another member of the production team or eliminated completely. Tasks like refilling material, monitoring equipment, and clearing basic jams were reallocated, allowing machine operators to focus on higher priorities like tooling set-up, quality checks and autonomous maintenance. Reallocating the less skilled tasks created additional bandwidth for operators, allowing them to run multiple production lines simultaneously. This plant then took things a step further by creating an operator assistant role to relieve machine operators of the less skilled tasks, and act as an upskilling opportunity to train the next cohort of machine operators. By the end, this plant increased their capacity by 4X in bottlenecked areas, first by offloading tasks to double the utilization of their existing machine operators, then by doubling the number of operators through the upskilling program.
Stories from the real world
In this video we cover how several businesses have been able to find skilled workers to support production, and improve key operational metrics by tapping into their local market and building an on-demand labor pool.
Veryable - A Unique Solution
Veryable is tailor made to address the skills gaps in your operations. Our on-demand labor model provides instant access to a labor pool of skilled operators, without the incumbrances of the typical hiring process, enabling upskilling and full utilization of your existing workforce. Moreover, the operational experts at Veryable will support you to identify and resolve bottlenecks in your value stream, increasing throughput without the need for costly investments in equipment or manpower. Contact your local team to get started.
To learn more, check out the other articles in this series:
Creativity Over Capital: Changeover Reduction
Creativity over Capital: Growing Your Business without Capital Investment
Creativity Over Capital: Fleet Optimization for Beverage Distributors
Previous Posts
Trump 2.0 Week 30 In Review: Discussing The China Deadline Extension, The Potential For Even Higher Tariffs on India, and More
The Future of Manufacturing and Logistics
Create a free business profile today to explore our platform.
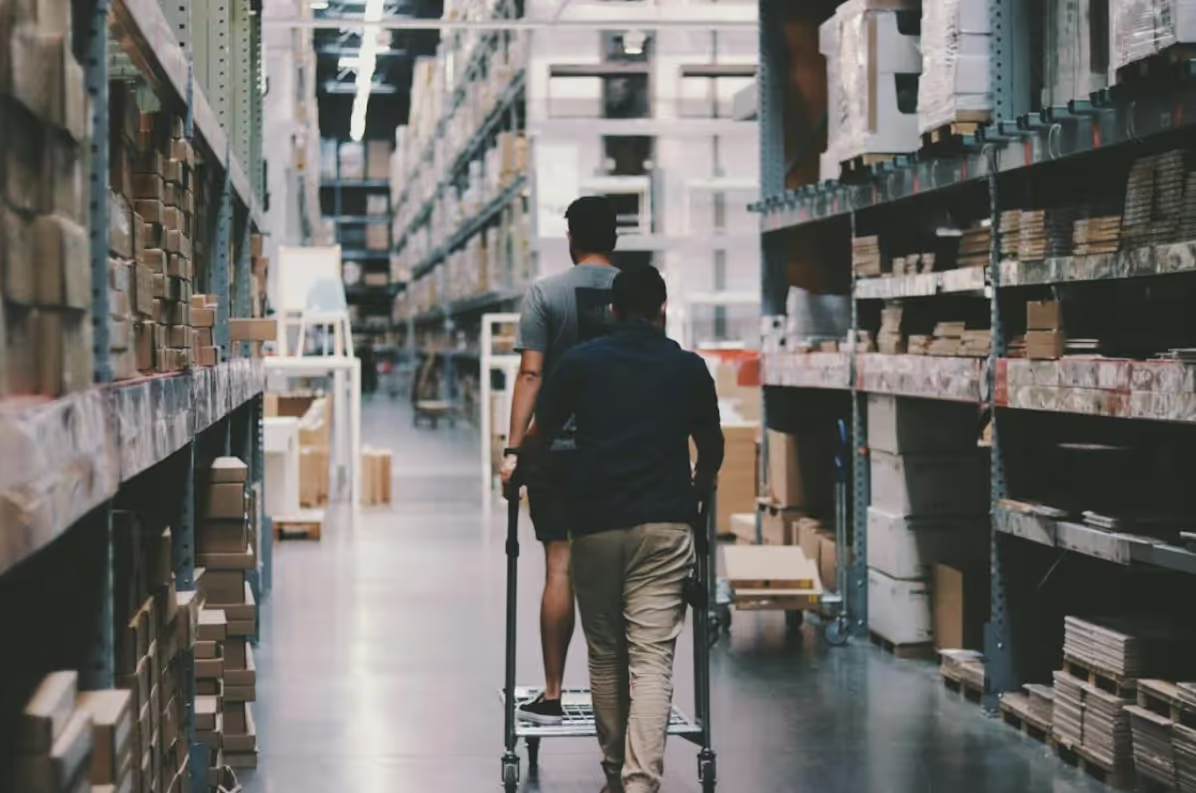