Throughput: What It Is and Why It Matters In Production
In today’s fast-paced market, throughput—the rate at which a system or process produces and delivers finished goods—is a critical KPI directly linking operational performance to revenue generation. While metrics such as cycle time, equipment uptime, or scrap rates provide insight into specific process elements, throughput offers a comprehensive measure that addresses the fundamental question for all stakeholders: How much finished product can be shipped reliably within an hour, a shift, or a day?
An increase in throughput accelerates cash flow, enhances customer satisfaction, and strengthens market position. Conversely, declining throughput leads to growing backorders, diminished customer confidence, and reduced competitiveness. Ultimately, throughput serves as a vital indicator of operational health and business success.
In this article, we’ll dive into what throughput is, why it matters, and how you can improve it to drive greater efficiency and profitability.
What Throughput Really Measures
At its core, throughput is a straightforward calculation:
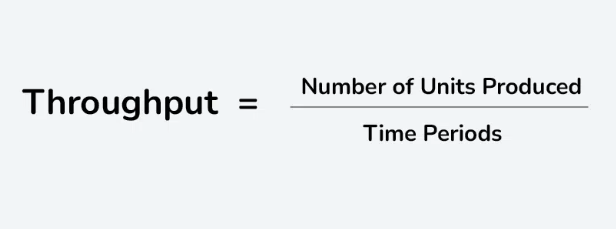
However, consistently achieving high throughput is far from simple. It requires a holistic approach where equipment reliability, workforce availability, seamless material flow, efficient plant layout, and disciplined scheduling all intersect to keep production moving.
A facility might boast a strong Overall Equipment Effectiveness (OEE) score, yet still fall short of revenue targets if finished goods stall—whether pallets accumulate in front of a shrink-wrapper or labor shortages cause bottlenecks at critical workstations. Throughput captures this broader reality by reflecting not just isolated efficiencies, but the true rate at which quality product reaches customers.
Maximizing throughput demands operational alignment across people, processes, and technology—ensuring every link in the production chain supports steady, reliable output.
Why Throughput Matters More Than Ever
In today’s market, where customers expect shorter lead times and supply chains operate on just-in-time inventory models, throughput has become a critical driver of business success. The speed at which quality products move through production and out the door directly impacts a company’s financial health and operational agility.
Higher throughput accelerates cash flow by converting work-in-progress (WIP) into revenue more quickly. The faster products are completed and shipped, the sooner invoices can be issued and payments received—improving liquidity and supporting ongoing operations.
At the same time, increased throughput reduces holding costs by minimizing the amount of inventory sitting idle on the floor. Leaner inventory lowers storage expenses, decreases risk of obsolescence, and frees up valuable space for higher-value activities.
In essence, throughput is no longer just a production metric—it’s a strategic lever that enables manufacturers and distributors to stay competitive, financially resilient, and responsive in an increasingly dynamic market.
What Drives—and Disrupts—Throughput
Achieving and sustaining high throughput requires a clear understanding of the operational levers that influence how efficiently products move through your production process. When these drivers are well-managed, they create the foundation for optimized output, faster cash cycles, and consistent delivery performance. But when any one of them falters, throughput suffers—often leading to delays, lost revenue, and strained customer relationships.
Below are the four key drivers of throughput, along with the most common obstacles that prevent operations from reaching their full potential.
1. Workforce Availability and Flexibility
- Driver: Having the right number of skilled workers, at the right time, is fundamental to keeping production moving. A flexible labor model like Veryable's ensures you can scale capacity in response to demand fluctuations, cover absences, and prevent labor-related bottlenecks.
- Obstacle: Labor shortages, rigid schedules, high turnover, and absenteeism can stall production at critical points. Without the ability to adjust staffing in real time, throughput becomes inconsistent and unpredictable.
2. Equipment Reliability
- Driver: Reliable machinery keeps production flowing without interruption. Proactive maintenance and real-time monitoring reduce downtime, ensuring that equipment is operating at optimal capacity.
- Obstacle: Unplanned breakdowns, aging assets, or delayed repairs can halt production altogether. Even high-OEE environments lose throughput if machines are frequently offline or underperforming.
3. Material Flow and Supply Chain Coordination
- Driver: Smooth, uninterrupted movement of raw materials and components is essential for sustaining production velocity. Coordinated supply chains and efficient material handling keep WIP moving and minimize idle time.
- Obstacle: Disorganized layouts, late deliveries, or poor communication with suppliers can cause raw materials to sit idle between stages, leading to missed targets and reduced throughput.
4. Process and Scheduling Discipline
- Driver: Standardized processes, clear schedules, and consistent execution allow teams to operate efficiently with minimal variation. Accurate forecasting and disciplined production planning help maintain predictable throughput.
- Obstacle: Frequent changeovers, process deviations, and unclear production priorities introduce variability that slows output. Even small inefficiencies—if persistent—can compound into major throughput losses.
Additional Throughput Challenges
In addition to these core drivers and their direct obstacles, other operational issues can undermine throughput:
- Quality Issues and Rework: Defective products and inconsistent quality divert time and resources to rework, reducing available capacity and delaying shipments.
- Limited Visibility and Real-Time Data: Without accurate, up-to-the-minute visibility into labor availability, inventory levels, and production progress, teams miss opportunities to proactively address bottlenecks and reallocate resources.
By focusing on these drivers—and systematically eliminating the barriers that hold them back—manufacturers and distributors can unlock higher, more reliable throughput. Veryable supports this effort by delivering flexible, on-demand labor capacity that empowers your operation to adapt in real time and keep product moving—hour by hour, shift by shift, day after day.
Typical Throughput Benchmarks
Throughput benchmarks vary widely by industry, product type, and production environment. However, understanding general performance ranges can help you assess where your operation stands and identify opportunities for improvement.
1. Discrete Manufacturing (e.g., automotive, electronics)
- Typical Range: 20–200+ units/hour, depending on complexity and automation level
- Highly automated lines with standardized products often achieve higher throughput, while custom or manual assembly lines trend lower.
2. Food & Beverage Processing
- Typical Range: 50–1,000+ units/hour
- Fast-moving consumer goods (FMCG) operations prioritize speed and volume, with throughput heavily influenced by packaging speed and line balancing.
3. Warehousing & Distribution
- Typical Range: 100–600 orders/hour (for outbound fulfillment)
- Throughput depends on picking methods, order complexity, layout efficiency, and labor availability. Facilities using automation or flexible labor often achieve higher rates.
4. Job Shops & Custom Fabrication
- Typical Range: 5–50 units/hour
- Lower throughput is expected due to the high variability in product type, routing, and setup time. Optimization efforts focus on reducing changeovers and improving flow.
5. Packaging & Assembly Lines
- Typical Range: 100–800 units/hour
- Consistent materials and repeatable processes allow for higher throughput, especially when supported by lean practices and modular labor capacity.
How to Use Benchmarks Wisely
While benchmarks provide useful context, the most meaningful comparison is against your own historical data. Tracking your throughput over time helps you pinpoint trends, diagnose inefficiencies, and measure the impact of operational changes—especially when introducing flexible labor models like Veryable.
How Veryable Helps Manufacturers and Distributors Maximize Throughput
Throughput is the truest measure of production performance—and one of the most difficult to optimize without flexibility. Traditional labor models often constrain throughput by limiting a company’s ability to scale capacity in real time. Veryable solves this challenge by giving manufacturers and distributors access to an on-demand labor marketplace, enabling a level of operational agility that fixed staffing models simply can’t match.
Here’s how Veryable helps maximize throughput across the key drivers of production:
1. Workforce Flexibility On Demand
Veryable allows businesses to build a flexible extension of their core workforce. Operators can be added exactly when and where they’re needed—whether to respond to unexpected demand surges, cover absenteeism, or keep a critical bottleneck staffed. This means you can maintain consistent production flow without relying on overtime or overstaffing.
2. Real-Time Labor Scalability
As order volumes shift, Veryable gives you the power to adjust labor capacity in real time. Instead of letting WIP pile up or delaying shipments, you can ramp labor up or down as needed—ensuring that throughput remains steady even in volatile environments.
3. Smoother Scheduling and Fewer Bottlenecks
With access to a pool of pre-vetted, skilled workers, your scheduling becomes more dynamic and less prone to disruption. This added flexibility reduces delays caused by labor gaps and keeps production running at optimal speed.
4. Reduced Downtime and Idle Resources
Veryable’s platform empowers teams to proactively address bottlenecks by matching labor to constraints as they emerge. When key equipment is back online or materials arrive unexpectedly, you can quickly deploy workers to boost available capacity and avoid idle time.
5. Data-Driven Operational Decisions
Veryable's Workforce Management platform, which can be used in collaboration or on its own, provides visibility into labor utilization and performance trends, giving operations leaders the insights they need to fine-tune scheduling, improve planning, and support continuous throughput improvement.
Conclusion
In today’s high-velocity, demand-driven market, throughput is more than a production metric—it’s a direct indicator of how efficiently your operation turns effort into revenue. It reflects the coordination of people, processes, equipment, and supply chains, serving as a real-time pulse on operational performance.
Achieving higher throughput means faster cash cycles, lower operating costs, and a stronger ability to meet customer expectations. But improving it requires visibility, flexibility, and control across the entire production process. By understanding the drivers, addressing the obstacles, and embracing more agile operating models, manufacturers and distributors can unlock the full potential of their operations—and build the resilience needed to compete and grow in an increasingly dynamic environment.
Veryable supports this transformation by enabling real-time labor flexibility through its on-demand labor model—giving operations the capacity they need, exactly when they need it, to keep throughput moving at speed. Click here to learn more about how on-demand labor fuels faster, leaner operations.
Previous Posts
Trump 2.0 Week 18 In Review: Discussing The “One Big Beautiful Bill”, Notable New Investments in U.S. Manufacturing, and More
The Future of Manufacturing and Logistics
Create a free business profile today to explore our platform.
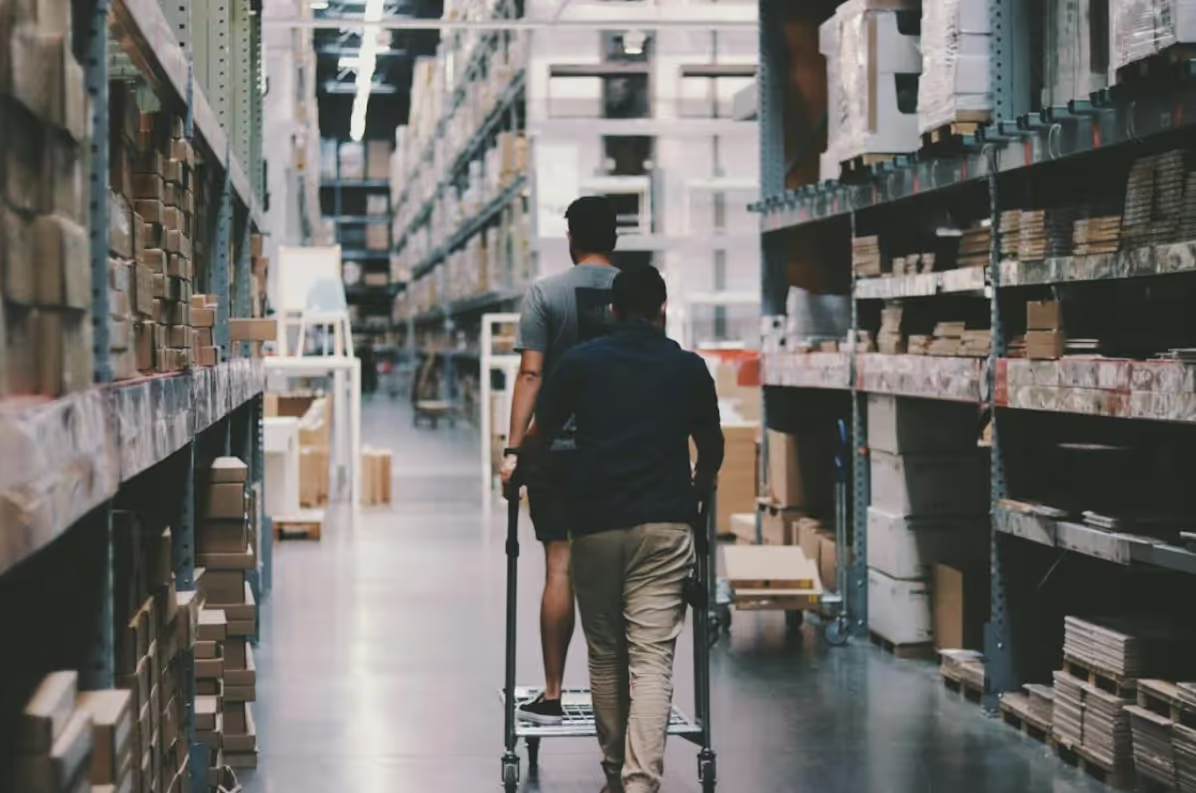