Now is the Time to Take it Back
Supply Chain Resilience amidst the Coronavirus
Now is the time for US manufacturers to take back what’s been given away. The current Coronavirus related global supply chain disruptions are exposing what we all already knew: we have drastically over-rotated on Chinese buy and left our supply chains vulnerable and unstable. Every company I have spoken to in the last month is feeling the impact and currently scrambling to rebalance their spend – this is the time to reclaim volume and US manufacturers must rise to the occasion. Put yourself out there and get that volume back. Get aggressive and reassert yourself as the top supplier again. You can do it. A lot has changed in the last 20 years and now is the time to usher in that previously elusive US manufacturing renaissance.
The Scales are tilting back toward Localization
As we've discussed previously, US manufacturing jobs peaked 40 years ago in 1979 at around 20M. Since that peak, the US has lost 7M (approximately 35%) of those jobs, while China has added nearly 50M manufacturing jobs over the same span. For every one manufacturing job lost in the US over the last 40 years, China gained 7.
The historical rationale was pretty straight-forward: labor arbitrage is a powerful cost-out lever. In the early 2000s, China’s average hourly wage was approximately $0.70/hour. Moving factories to China and shifting spend generated significant cost out...at least for a while. And at least on paper.
However, looking back on the original business cases usually paints an ugly picture. Many businesses have never actually realized the promised benefits. Actual profits have lagged projections. Business cases were wrong, or at best optimistic. In light of this reality, many manufacturers have begun rethinking their supply chain strategy over the last couple years and begun to decrease their exposure to China. Many have entered a dead sprint on this front in the first few months of 2020.

What has Gone Wrong?
For the purpose of simplicity, we can attribute the problem at hand to two intertwined failure modes – one strategic and one tactical. The strategic failure is ignoring the importance of supply chain resiliency. The tactical error is not planning for total landed costs. Both are the result of bureaucratic complacency.
Supply chain resiliency is something easily taken for granted. We’ve underestimated how fragile global supply chains actually are, and we’ve gotten greedy. We’ve continued to milk the same play over and over until hardly any safety net remains. The 20% local buy moves to 10% then to 5% in the absence of other, more creative cost-out ideas. What’s left of the local buy becomes insufficient to respond when something breaks in the global supply chains…as evidenced by the worldwide scramble we’re currently witnessing.
The landed cost error occurs at the tactical level by only comparing specific direct costs, i.e., material cost deflation or labor arbitrage in isolation. The reality is that there are other, quite significant direct and indirect costs that always create an offset. Freight, tariffs, holding costs, qualification costs, cost of quality, etc. often cancel out the entire value proposition. It’s not uncommon to see premium air freight alone hit 5% of sales. Not only are we losing jobs, we’re paying just as much in freight. It’s time to stop the nonsense.
The Automation Myth
The embarrassment around failed outsourcing strategies is why a great myth has been imposed upon an entire generation – that automation is responsible for the decline in US manufacturing jobs. Anyone close to the action in manufacturing sector knows this is not the case and some brave souls have started to tell the truth about it. Productivity in the manufacturing sector over the last couple decades has essentially grown at the same rate as the rest of the economy. The most effective levers in the manufacturing sector are still good old fashion Lean deployment, advancements in engineering, and brawn. Automation and robotics are not new and advancement in this area is not all that prevalent across the sector.
The automation narrative is attractive because it’s blameless. ‘How can you fault inevitable technological advancements for the decline in jobs? Get with the times, Luddite!’ Perhaps if the American public knew we’ve been betrayed by bureaucratic negligence and fed myths, we might not remain gracious servants to the institutions we’ve trusted.
Take it Back, Now
If history has taught us anything, it’s that the will of the American people can overcome any obstacle. Times of crisis are when heroes emerge and fortunes are made. This is the time for small businesses to step up and reclaim the work. This is the time for OEMs to award their spend locally. This is the time to be aggressive and ramp up productive capacity. The work has not been automated away – it’s been sent away with little benefit to show for it. Let’s go get it back now and let Veryable help you.
Previous Posts
Old Roles, New Realities - Who Owns Agility?
The Future of Manufacturing and Logistics
Create a free business profile today to explore our platform.
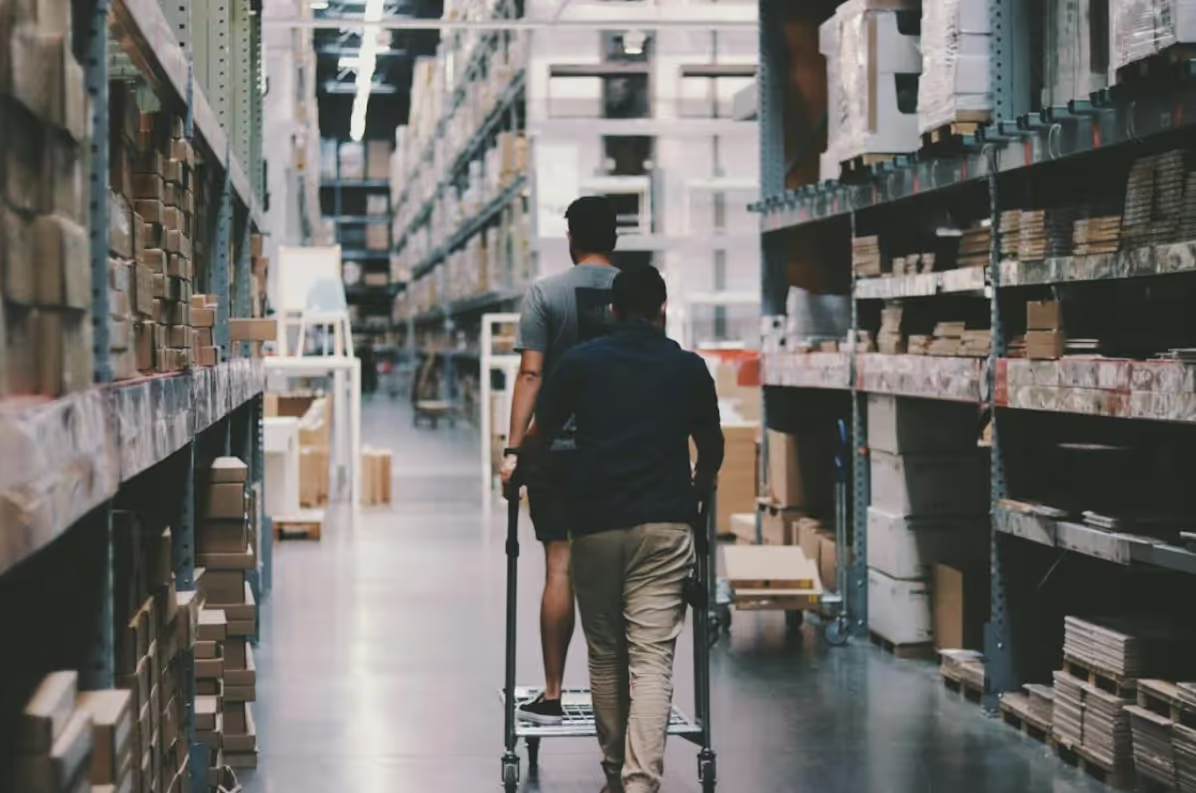