The 80/20 Rule for Operational Improvements in Manufacturing
It’s important to know which actions will drive results, especially when there’s so much noise. Being able to narrow down your to-do list to what matters is a crucial skill for doing work that matters in today’s world. At Veryable, we’ve seen that an outdated labor approach contributes to many issues, and we help companies leverage on-demand labor for a breakthrough in efficiency.
In this article, you’ll learn about the 80/20 rule, how seemingly small changes can produce big results, and how to apply this thinking to your operation.
What is the 80/20 rule?
The 80/20 rule, also known as the Pareto Principle, is an observation of the common situation in which 80% of outcomes will come from 20% of actions. It has been observed in yields from crops, the distribution of wealth in an economy, the output of workers in a facility, and many other scenarios over the years since its conception.
Where does the 80/20 rule show up in manufacturing?
There are many ways to apply the Pareto Principle in your operations. If you look closely, you will likely see it in the workers, the machinery, the materials, and the products. Often, 20% of your products will produce 80% of your sales. The same goes for the output you get from your best workers, the problems you experience with your machinery, and the defects you get from working with certain materials. You should examine your operations for anywhere you can identify where the 80/20 rule applies, because that’s where you should be focusing your efforts. These high-leverage zones will produce greater results with less effort.
For example, you might notice that products coming out of a certain workstation have more defects than ones coming from other stations. That should tell you that it’s a good place to start applying your efforts, rather than trying to implement a standard fix across all workstations.
How to apply the 80/20 rule to make operational improvements
It’s great news for us that someone has already applied this rule in the manufacturing environment. The application of the 80/20 rule to manufacturing as a form of quality management by Dr. Joseph Juran became the precursor for the Six Sigma methodology and put the “define” step in the DMAIC framework.
You too can apply the 80/20 rule to your operation in a few key ways:
- Improving quality
- Streamlining value flow
- Optimizing labor allocation
Improving quality
The easiest way to apply the 80/20 rule to your operation is with quality management. If you watch where the defects are coming from in your process, you will likely identify one or two steps where most of the problems occur. Identifying where 80% of the problems come from will allow you to apply changes to the 20% of process steps where they arise. This ensures you are not wasting effort by trying to fix the problem somewhere besides the cause of the issues, and gets you closer to the root from the start. This also creates the advantage of focus by applying attention to a select group of problems that will drive results.
Streamlining value flow
Another way to use 80/20 thinking is to streamline the flow of value through your operation. There is likely about 20% of the feature set that drives 80% of the value to the customer. When you identify the steps that are high-leverage, you can orient your operation around them to ensure you are focusing your efforts on value-add activities. This might mean removing unnecessary steps that lead to extra processing so that your operation is leaner. Or it could mean creating parallel lines for this important step to increase throughput. You could also streamline value flow by prioritizing the 20% of products that result in 80% of your revenue. By focusing on the products that bring the most revenue into your company, you can be sure your time is spent wisely when the times call for tightening down and running a leaner operation.
Optimizing labor allocation
Applying the 80/20 rule will show you where you should apply your workforce, because it gives you a clue about where to start when you want more throughput. If you have a bottleneck to address, you can first determine whether it is one of your high-leverage steps or not. If it’s high-leverage, increase the throughput by adding workers or machinery. If the bottleneck is not high-leverage, consider moving specialized workers off this work and leveraging flexible labor to cover this task.
How flexible labor helps you focus on what matters
With a fixed capacity, you’re limited in what you can accomplish when it comes to operational improvements. You can only move your headcount up or down over long horizons, which means you can’t optimize your labor to do the high-leverage work needed to meet customer demands in their time frames. With on-demand labor, you can instantly flex your labor capacity to match your daily needs. This means you can apply the 80/20 rule aggressively to ensure you’re focused on high-leverage work, and that you’re only maintaining the lean headcount needed to meet demand.
Learn how you can run a leaner, faster operation with on-demand labor.
Previous Posts
Old Roles, New Realities - Who Owns Agility?
The Future of Manufacturing and Logistics
Create a free business profile today to explore our platform.
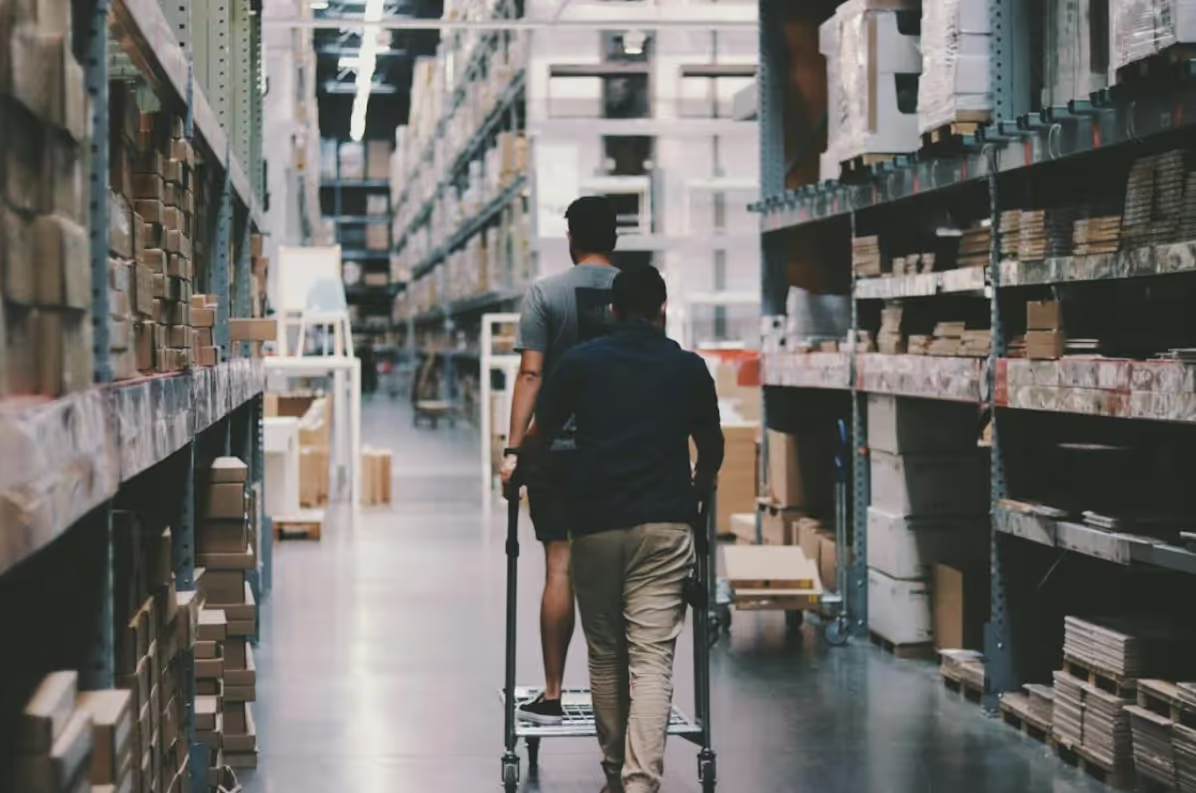