Understanding the Hour-by-Hour Board: A Lean Tool for Efficiency
In the world of Lean manufacturing, continuous improvement is the name of the game. Lean principles aim to optimize processes and reduce waste, ultimately leading to increased efficiency and improved quality. One invaluable tool in the Lean toolbox is the Hour-by-Hour (HbH) board. This visual management tool plays a pivotal role in tracking performance, enhancing communication, and facilitating real-time decision-making within the manufacturing environment. In this blog, we'll dive into the background and the numerous benefits of the Hour-by-Hour board as a Lean tool.
The Background of the Hour-by-Hour (HbH) Board
The Hour-by-Hour board, also known as the Hourly Production Board or the Hourly Tracking Board, is a visual display board prominently placed within the manufacturing facility. It was initially developed as part of the Toyota Production System (TPS), which forms the foundation for Lean manufacturing practices. The core idea behind the HbH board is to provide real-time visibility into key performance indicators (KPIs) and production metrics on an hourly basis.
Benefits of the Hour-by-Hour (HbH) Board
1. Real-Time Performance Monitoring: The HbH board offers an at-a-glance view of current production performance. Tracking metrics such as production output, quality, and downtime on an hourly basis, allows teams to quickly identify issues or deviations from the plan. This real-time monitoring enables faster corrective actions, preventing small problems from escalating into larger ones.
2. Enhanced Communication: Communication is a cornerstone of Lean manufacturing, and the HbH board fosters transparency and collaboration. It serves as a focal point for daily production meetings, where cross-functional teams gather to discuss progress and address any challenges. This open communication ensures everyone is on the same page and working towards shared goals.
3. Data-driven decision-making: The HbH board empowers teams to make informed decisions by displaying historical data alongside current metrics. It helps identify trends and patterns, making it easier to implement improvements over time. Data-driven decision-making is a fundamental aspect of Lean, and the HbH board facilitates this process.
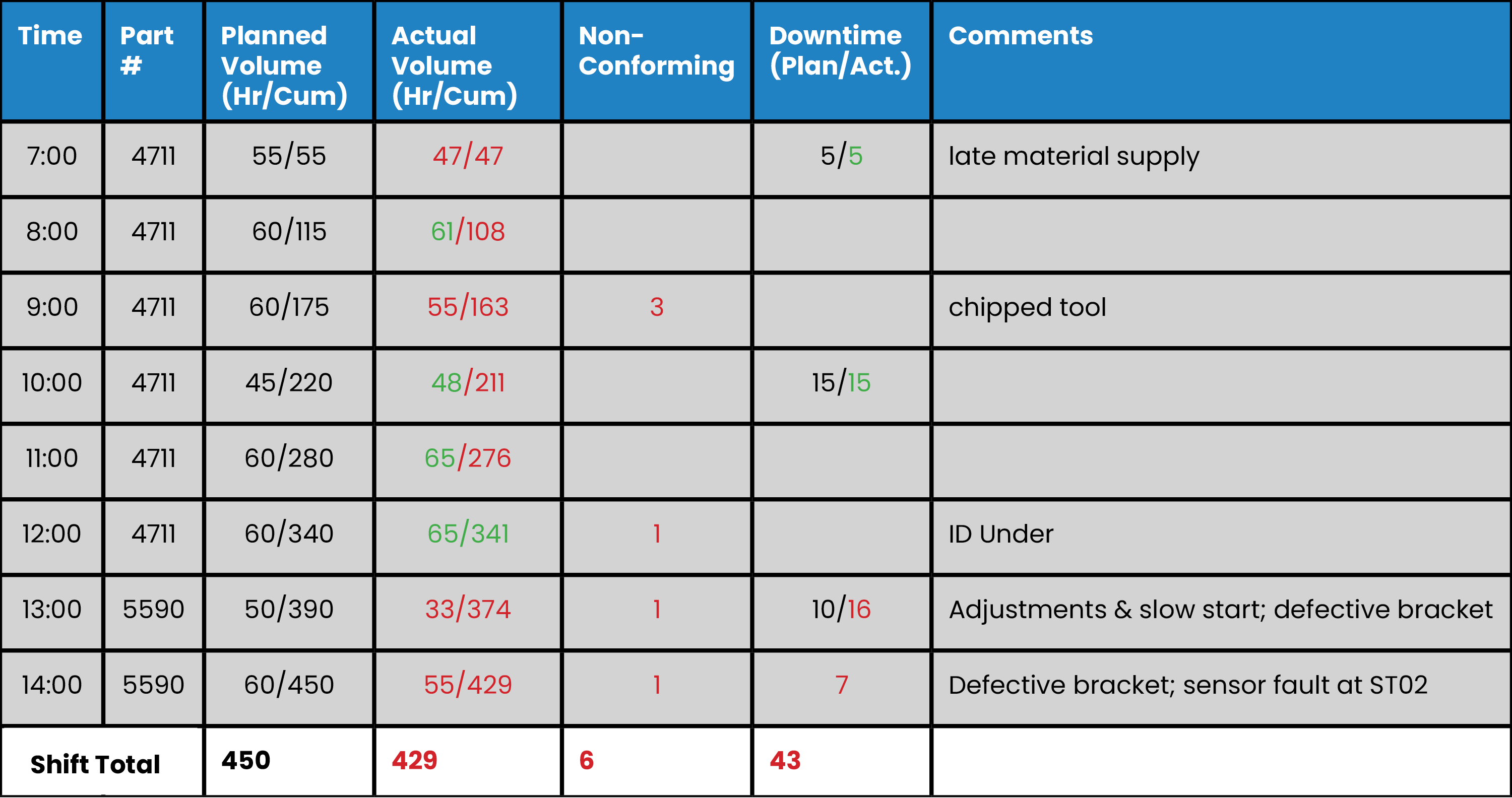
4. Improved Accountability: When performance metrics are displayed for all to see, it encourages a sense of ownership and accountability among team members. Knowing that their work is being monitored hourly motivates employees to meet or exceed targets consistently. This accountability can drive a culture of continuous improvement within the organization.
5. Reduced Waste: Lean principles aim to eliminate waste in all its forms, including wasted time, materials, and resources. The HbH board helps identify the root causes of downtime, quality issues, and other forms of waste, enabling teams to address them promptly. As a result, waste is minimized, and processes become more efficient.
6. Flexibility and Adaptability: Manufacturing environments are dynamic, and the HbH board allows for quick adjustments to the production plan. If unexpected disruptions occur, teams can adapt their strategies in real-time to minimize the impact on overall production schedules.
7. Employee Engagement: Engaged employees are more likely to contribute their best efforts to the organization. The HbH board engages employees by involving them in the decision-making process and providing a platform for their feedback and suggestions. This engagement can lead to improved morale and a more dedicated workforce.
How Veryable can help take action on your Hour By Hour findings
An hour by hour chart is a great way to understand the issues and constraints that impact production. Typical constraints include material availability, material handling, equipment downtime, labor inefficiencies, not enough labor (call ins, turnover, or labor pulled to other areas of an operation), or quality issues. Labor will directly or indirectly impact every aspect of your operation. Those businesses that are flexible and agile to adjust to the daily changes in a manufacturing or logistics operation have the best chance at outperforming their competition on service and cost. Veryable has two platforms that can help you create flexibility within your full time employee base (Workforce Management) and to create the ability to scale labor up and down through our on-demand labor marketplace. This will help you understand where you are overstaffed, where you are understaffed, and allow you to take quick action to resolve it. These tools will enable real time decision making with integrated data and metric tracking making your operation more proactive and less reactive.
Here is a brief overview of these two tools:
Veryable's On-Demand Labor Marketplace
Labor will directly or indirectly touch every aspect of your operational performance. It is also one of the largest expenses on your P&L. Ignoring opportunity or being comfortable doing things the way they've always been done makes it just that much harder to find net improvement elsewhere. Leveraging Veryable’s On-Demand Labor Marketplace to build a flexible extension of your full-time workforce will allow your team to precisely match labor capacity to demand on a daily basis. Adopting this approach gives your operations leaders the resources they need to deliver the maximum return for the business and the most value for the customer.
Veryable's Workforce Management Tool
Veryable’s Workforce Management Tool ties together multiple systems (ERP, WMS, MES, HRIS, etc.) to use real-time data to automate the labor planning process and guide your leadership in making better critical decisions. This eliminates guessing, protects against costly forecasting inaccuracies, and enables performance-based decision making without the burden of manual spreadsheet updates or back-of-the-napkin estimating. This tool can operate as a standalone platform for your full time employees, or you can access Veryable's on-demand marketplace from within this tool to fill any gaps in your operation on short notice. The best part is, you'll be able to view real-time performance data in just clicks for both full time employees as well as Veryable Operators.
Together these systems truly optimize every labor dollar spent across your footprint. This enables better visibility to translate best practices and can act as a roadmap for continuous improvement.
Conclusion
In conclusion, the Hour-by-Hour board is a powerful Lean tool that offers numerous benefits to organizations. Its ability to provide real-time visibility, enhance communication, and support data-driven decision-making makes it invaluable for those committed to continuous improvement. Embracing the HbH board and integrating it into their Lean practices, companies can unlock greater efficiency and drive sustainable growth in today's competitive manufacturing landscape.
For more information, visit our Lean Center of Excellence Homepage or our homepage for Continuous Improvement, Operational Excellence, and Lean Professionals.
Previous Posts
Trump 2.0 Week 30 In Review: Discussing The China Deadline Extension, The Potential For Even Higher Tariffs on India, and More
The Future of Manufacturing and Logistics
Create a free business profile today to explore our platform.
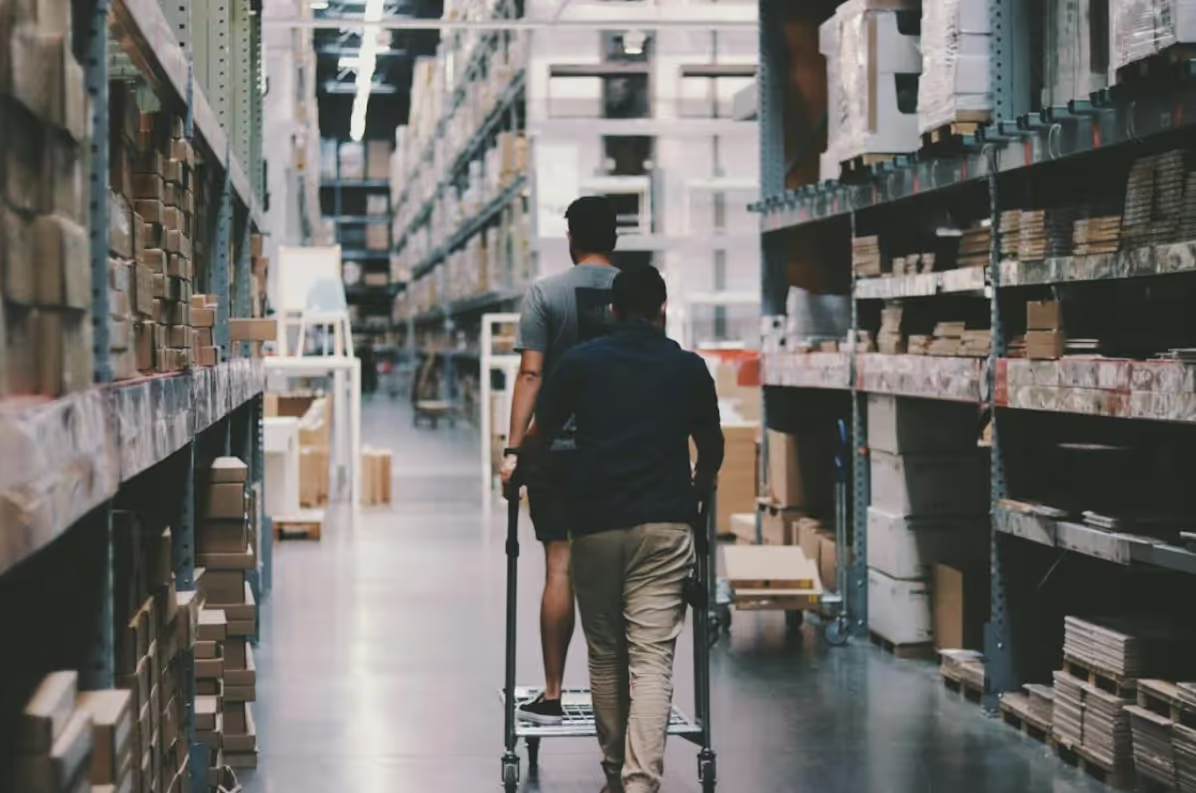