Strategic Moves: Important Considerations for Manufacturing Plant Relocation
In the ever-evolving manufacturing sector, business leaders frequently grapple with the decision to expand or relocate their plants. Whether driven by the imperative to optimize operations, respond to market shifts, or outgrow existing spaces, the decision to move involves a meticulous evaluation process, evoking a range of emotions from company leaders, including excitement, anticipation, and a hint of anxiety.
Industries spanning aerospace, agribusiness, automotive, and advanced manufacturing recognize site selection as a critical element of their short- and long-term investment strategy. Supply chain reliability emerges as a top priority, making the choice of location a pivotal decision. So, what are some of the key considerations when contemplating a move?
Key Factors in Site Selection
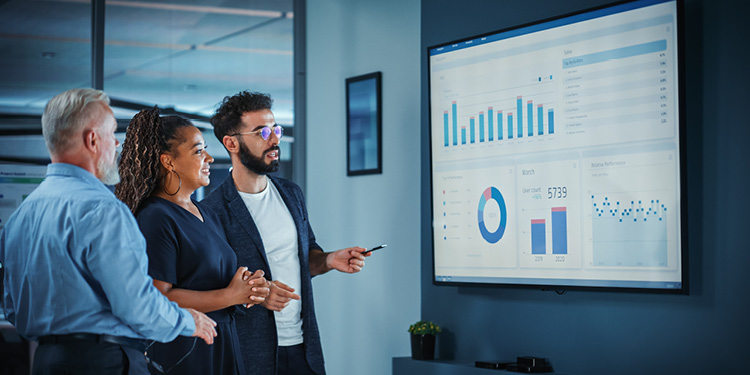
While industry-specific nuances may exist, common considerations permeate site-selection processes across various sectors. Optimal access to markets—be they local, national, or global—while minimizing delivery costs and ensuring the availability of a skilled workforce for current and future operations often determine a location's attractiveness.
The factors influencing delivery costs are multifaceted, with a focus on selecting the right location to support just-in-time and just-in-sequence supply lines. For instance, if an airport is present, considerations arise regarding its capacity to handle large cargo planes or the necessity for runway expansion. Similarly, the availability of direct rail connections and access to major interstate routes for truck transportation are crucial. In the realm of shipping by water, considerations extend to the accessibility of ports by land, rail, and ship. Against this backdrop, a state's endorsement of a pro-business climate and its efforts to attract and retain manufacturers become key factors.
The ongoing shifts in mobility and electrification within the transportation industry intensify the competition between states. The strategic positioning of joint venture partners or suppliers nearby can transform an entire region. To emphasize a site's appeal as a preferred manufacturing location, a state's economic development team may showcase attributes such as low electricity costs, renewable energy leadership, incentive programs, and growth-minded initiatives.
The attractiveness of a location is often contingent on its available workforce and the state's ability to address both current and future needs of companies. Questions regarding vocational training, the availability of degrees in engineering functions, and state investments in education to bolster the workforce play a pivotal role in the evaluation process.
Beyond Industrial Needs in Site Selection
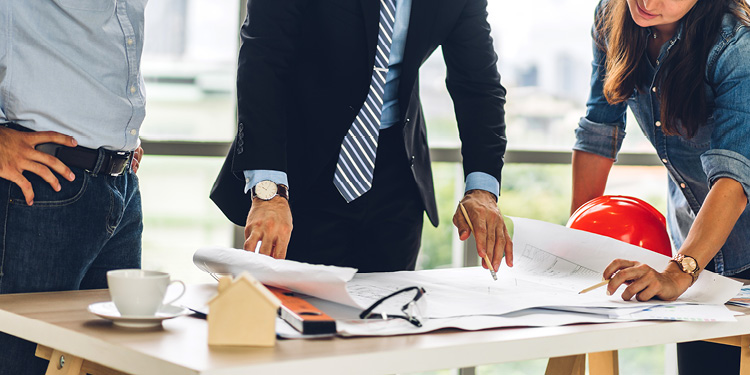
Housing and placemaking, encompassing infrastructure, quality health systems, public transportation, social services, and recreational and cultural activities, are integral aspects companies consider during the vetting process. A holistic suite of programs fostering talent through training, recruitment, and quality-of-life initiatives carries substantial weight in the final site selection.
Insights into workplace culture, including an analysis of collective bargaining dynamics, state statutes on right-to-work, and wage and hour regulations, are crucial considerations for manufacturers. These factors also come into play during the due diligence review of potential merger or acquisition targets and partners, influencing the viability of entering into a financial arrangement.
Unionized Employees?
For plants with unionized employees, a thorough review of the collective bargaining agreement is essential. Clauses related to preservation, duty to bargain decisions, and duty to provide notice of plant closure should be carefully examined. Generally, if a new plant location is deemed a "continuation" of the old one, the employer must continue recognizing and bargaining with the union from the old plant. See National Labor Relations Board v. Gaylord Chemical Co., No. 15-10006, 2016 WL 3127087 (11th Cir. Jun. 3, 2016). The National Labor Relations Board and courts often consider a continuity of workforce if transferred employees constitute a significant portion (40%) of the new facility's workforce. Id.
See how RTIC was able to seamlessly move into a new facility across Houston by utilizing Veryable Operators
To streamline the transition during relocation, companies can harness Veryable's on-demand labor platform. Instead of diverting full-time employees from their regular tasks, this approach enables companies to find workers on demand, reducing lead times, avoiding overtime costs, and maintaining on-time, in-full delivery rates.
Rather than immediately hiring additional full-time workers, companies can address immediate needs by bringing in on-demand workers for short-term assistance. Establishing connections with these workers through the platform facilitates seamless integration into the labor pool for future requirements. This approach minimizes the need to replace lost full-time employees and eliminates the necessity for overtime from existing staff.
Curious to learn more? Check out our 12 Step Guide to Manufacturing Facility Moves and explore Veryable's on-demand labor platform here.
Previous Posts
Trump 2.0 Week 23 In Review: Discussing A Potential July Deadline Extension, Negotiations With Key Trade Partners, & GE’s $490M Investment
The Future of Manufacturing and Logistics
Create a free business profile today to explore our platform.
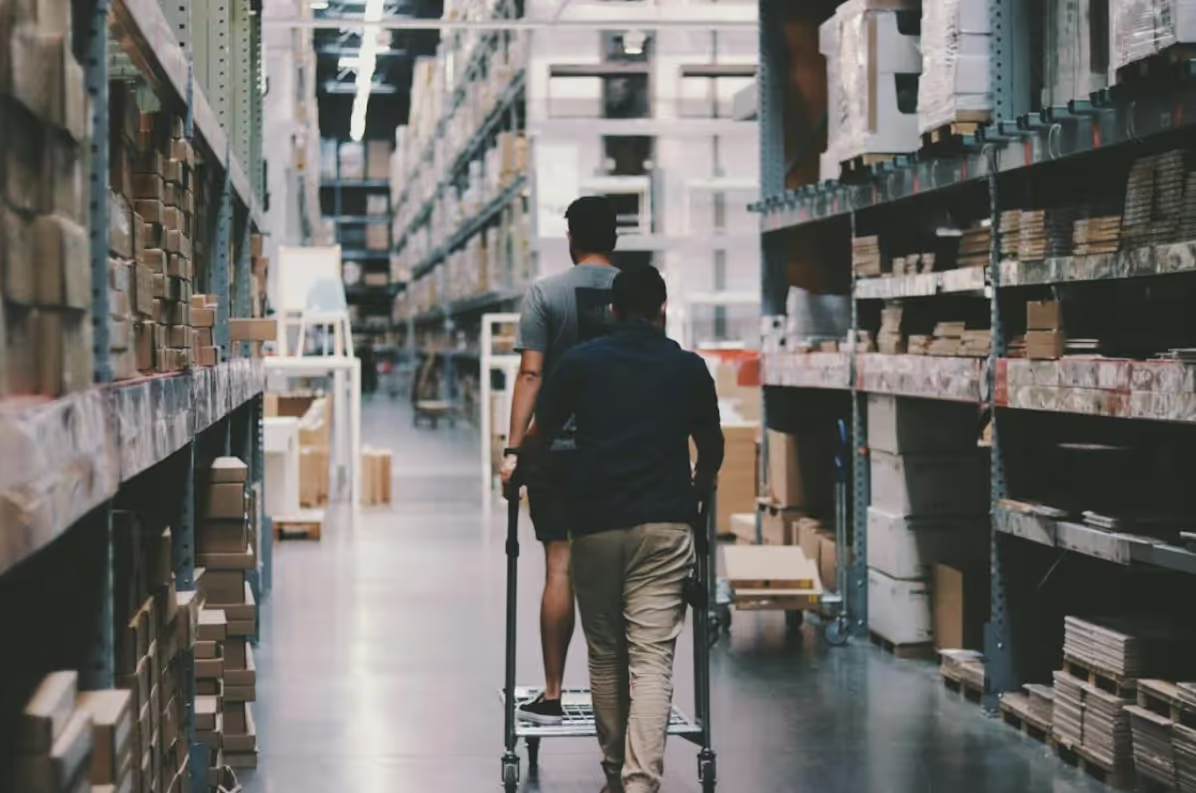