How to Fix Manufacturing Skills Training
The skilled labor shortage has been a persistent problem in manufacturing for some time now. What’s causing this, and how do we fix it?
At Veryable, we help businesses create flexible labor capacity to optimize their operations using on-demand labor. This involves training the on-demand workers quickly to make full use of this model, so we’ve learned quite a bit about skills progression as we’ve walked businesses along the journey to optimizing their operations.
In this article, you’ll learn what you can do to address the skills gap and train tradesmen to work in your facilities with on-demand labor.
What is Skilled Labor?

There are different definitions of skilled labor, which causes confusion when companies, governments, and everyday people try to discuss skilled labor. We’ve simplified this discussion by reducing the number of definitions of skilled labor based on how this idea is commonly discussed.
There are two main categories of skills and training:
- Artisan skills and trades
- Company-specific product or process knowledge
Artisan skills and trades draw attention from the government and organizations attempting to alleviate the skills gap through well-intentioned programs like teaching welding to high schoolers.
Meanwhile, company-specific product or process knowledge often gets more attention from manufacturers. Many believe that their company’s processes are so intricate and complex that they require artisan-level training to complete. Hopefully, this is not the case in your business, because it will severely limit your ability to build labor capacity, much less make use of flexible labor capacity.
The Problem With Most Training Approaches
One contributor to the skills shortage in manufacturing is the perspective of manufacturers that their processes and products all require “artisan skills.” Companies waste a lot of time trying to train workers from zero knowledge straight to artisan before allowing them to engage in the work.
This is like teaching someone to play Beethoven as their first song on piano without any sheet music or explanation of the keys. They’ll be able to repeat a very specific set of steps to make the right sounds, but they won’t have the foundational knowledge they need to improvise or adapt to a new situation.
When companies get company-specific knowledge mixed up with artisan skills or trades, they make it nearly impossible to find workers who can do what they’re expecting because they’re making the barrier to entry higher than it needs to be. The mistake here is thinking that company products or processes should be complicated, thus avoiding the responsibility of making the work clearly understood and repeatable.
To continue the piano metaphor, having unnecessarily difficult company-specific processes is like requiring a piano student to be able to play Beethoven for an audience of toddlers, who would much prefer Twinkle Twinkle Little Star. Lean practitioners would recognize this as overwork and immediately eliminate such a requirement so that they have an easier time finding piano players.
On-the-Job Training vs Artisan Training
On-the-job training gives the worker foundational technical and soft skills.
About 90% of the training in manufacturing should happen on the job. Manufacturing is a hands-on environment, and as long as people are doing the work, the best way for them to learn the tasks required in a manufacturing facility is to do them.
Artisan training requires someone who specializes in the skill to pass on their knowledge. This typically takes weeks, months, or years to accomplish. The time required to learn is the greatest difference between skills which can be taught on the job and artisan skills. The other main difference is that artisan skills require a foundation of other soft and technical skills before a worker can truly gain the benefits of the training and provide value to a company.
To summarize the difference between the two, artisan training requires foundational competencies and lengthy training, whereas company-specific training should not be so difficult it can’t be learned in a few tries.
The Path to Master Craftsman Through On-Demand Labor
Artisan training should come last because it requires foundational competencies. Through on-the-job training, you should teach 90% of the skills needed to work in your facility.

You can achieve this on-the-job training without losing throughput or having to hire additional employees. Many operations leaders think that they have to slow down to train, which causes lost throughput. However, on-demand labor enables you to maintain throughput while training new workers on your processes and keeping your specialized workers fully utilized.
Imagine how much more your machinists and welders could get done if they didn’t have to perform setup and changeover tasks!
Flexible labor can gain valuable experience by supporting your artisan workers. When on-demand workers participate in the actual work and get on-the-job training, this is a low investment way to train new workers on your processes and identify high performers while increasing your throughput.
Veryable has seen multiple examples of Operators on our platform who went from doing support work on their first work opportunity to becoming an artisan worker within the year.
You can start building flexible labor capacity using workers with the skills you need while increasing your throughput and utilization of your artisan workers. Learn more about flexible labor capacity in our blog about the concept of a labor pool.
Previous Posts
Old Roles, New Realities - Who Owns Agility?
The Future of Manufacturing and Logistics
Create a free business profile today to explore our platform.
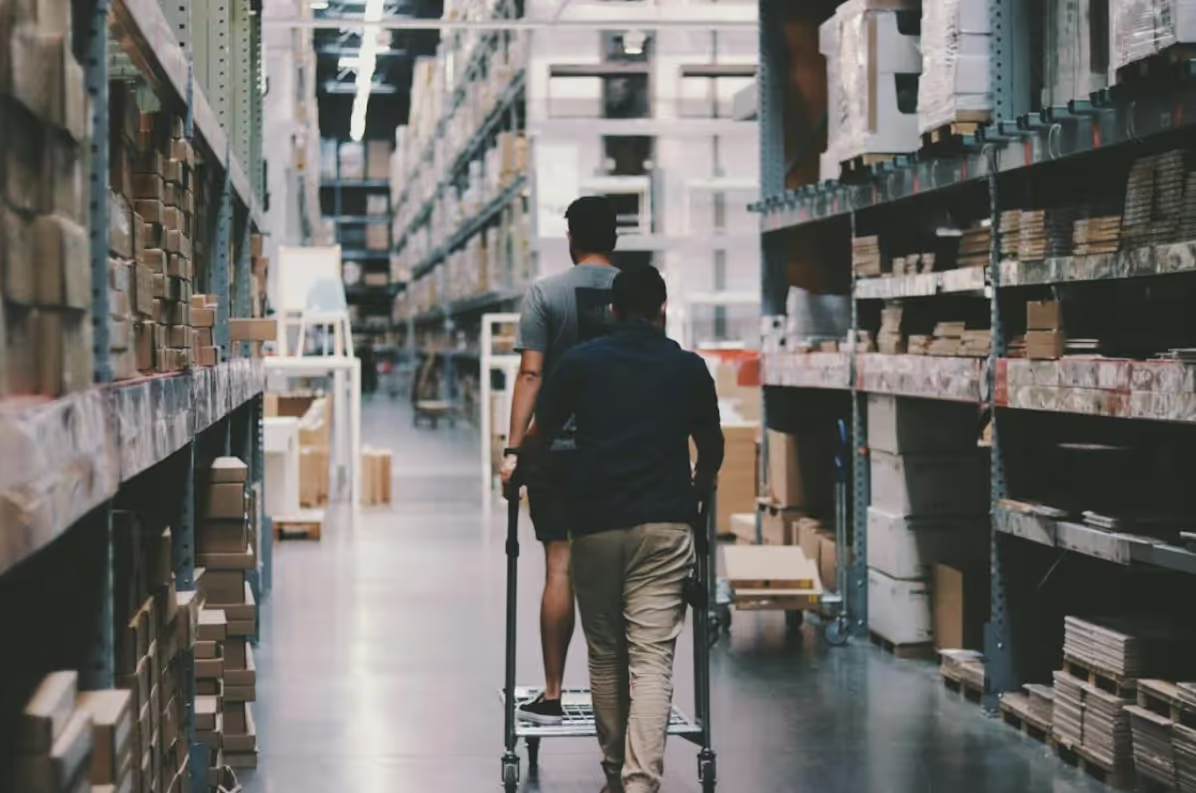