Labor Optimization: Consistent Labor Availability vs Productivity Rate
When thinking through your operation and how to best organize it to complete the work, you’ve most likely weighed prioritizing labor productivity rates versus prioritizing labor availability. This is actually a critical question, and one with implications on customer service that are not fully appreciated across an operation.
Answering the question first starts with identifying your objective - what is the one objective you absolutely must get the most out of in your operation? This could be best-in-class overall equipment effectiveness, high labor utilization, low error rates, or getting the product shipped quickly.
Optimizing for any one objective creates trade-offs all businesses must weigh. For example, optimizing for best in-class overall equipment effectiveness could mean that customer orders are slotted to optimize runtime instead of customer satisfaction, which extends lead times.
At Veryable, we’ve created an on-demand labor marketplace that lets companies build flexible labor capacity to consistently produce without sacrificing labor availability. However, this ability doesn’t remove the question of which goal to optimize for completely. Companies still have to make a choice. Although we do believe in optimizing for a constant productivity rate more than the alternative, even among Veryable users, companies approach this optimization decision differently.
We understand that prioritizing a consistent productivity rate is not for every business, which is why we will walk you through both options.
In this blog, we will explore two critical values to optimize and what it means when one is promoted over the other. You’ll be able to decide which is best for your operation: meeting a consistent productivity rate or having consistent labor availability.
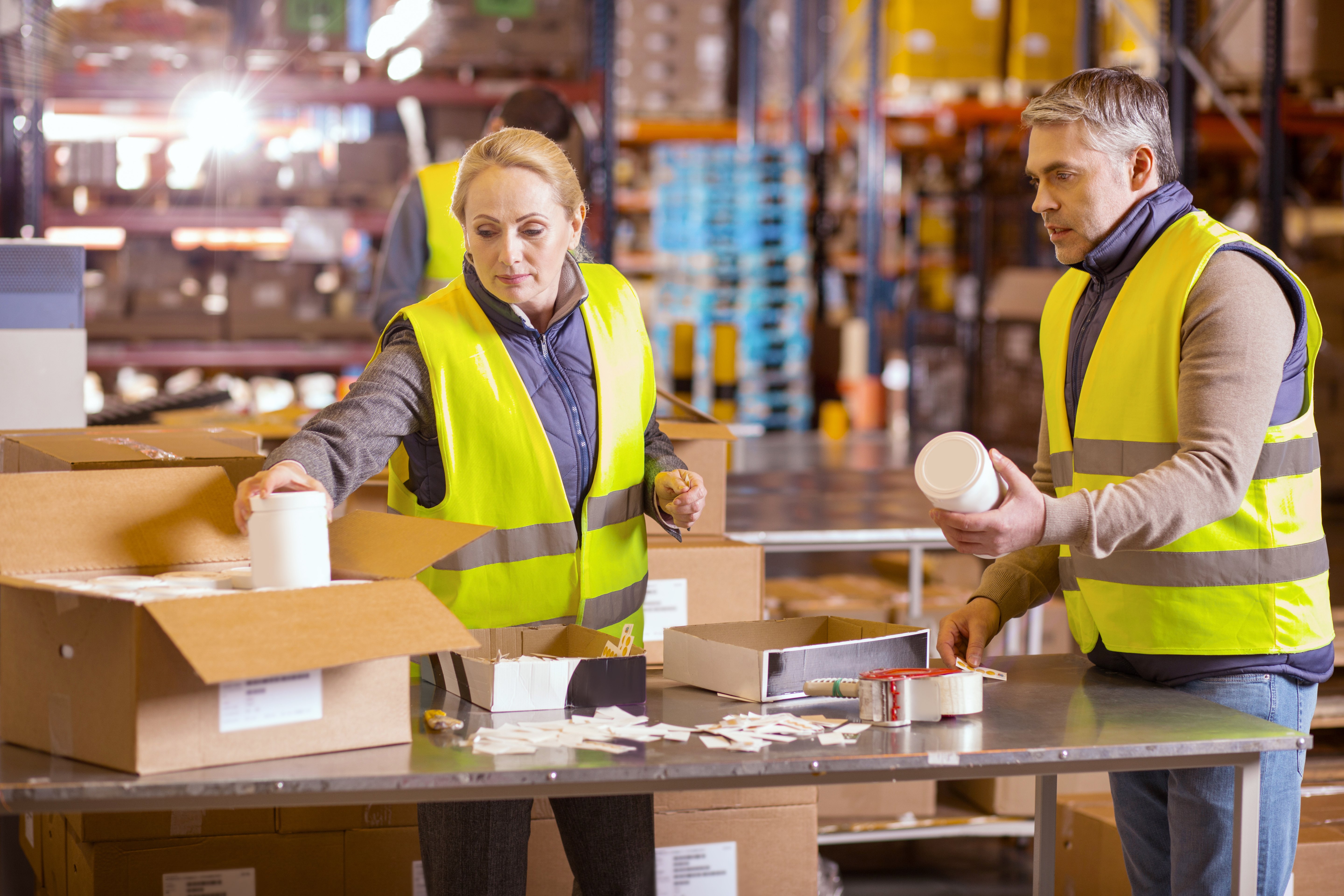
Managing consistent labor hours
Targeting consistent labor hours means to have a certain number of people in your workforce available the same amount of hours week over week, while the productivity rate varies based on demand. The job function can be production, picking, assembly, or inspecting units. By the numbers, this looks like the following table:
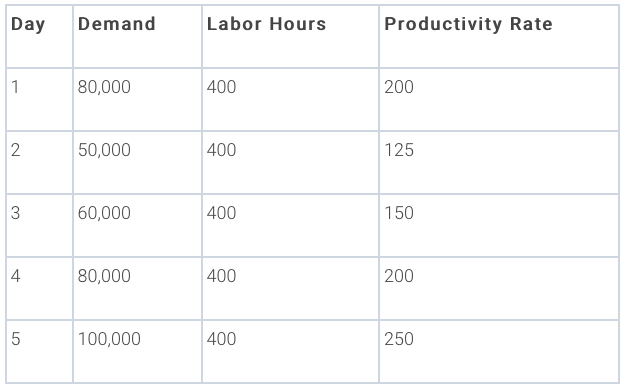
The table contains sample data to depict a work week at a production facility. Demand indicates the anticipated daily production. Labor hours represent the available labor capacity at the production facility, and productivity rate is the pace of the work. The demand is divided across the labor hours to find the productivity rate since the labor hours are being held constant.
As the trend in the table indicates, the productivity rate fluctuates as the demand changes each day. The workforce is staying consistent with an available 400 hours while the productivity fluctuates daily to match demand. You can see in the chart that this number of labor hours is capable of producing up to 250 units per hour (UPH), but only accomplishes this on one day out of the five.
Positives of consistent labor hours
This approach builds extra labor capacity into the daily available workforce to absorb demand volatility. A good analogy for this model is insurance. Just like with insurance, you’re paying for something you might not have to use. When you maintain consistent labor hours, you’re paying people to be available for the peak capacity that may or may not come later on.
Trade-offs of reaching consistent labor hours
On days when your demand isn’t high enough that workers need to work at their highest productivity, your labor cost per unit increases. In the example scenario, when the volume indicated by demand is not high enough to require your set number of workers working set labor hours to reach the 250 UPH, the workers slow down accordingly, and the time and cost invested in each unit increases. This increase in production cost reduces or eliminates the profit margin for each unit.
If you aim for consistent labor hours, the peaks and valleys of the demand schedule create slow days and high-paced days, and this up and down can wear on a workforce as they are starved for work one day and overwhelmed the next.
Achieving Consistent Productivity Rate
Aiming to achieve consistent productivity means to run the operation at full capacity during production hours. From the previous table, we’ve brought down the highest operating capacity achieved, and this becomes the target productivity rate for each day.
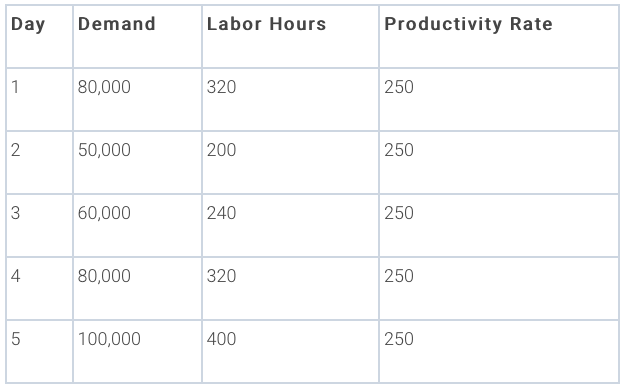
With a fixed productivity rate target, the labor hours become the dependent variable of operations execution. In this way, the operation is primed to run at the engineered productivity rates each day.
Positives of achieving consistent productivity rate
Scaling the labor to meet the demand removes the wasted productivity from the operation and maximizes the full potential of the available labor. This ensures that designated productivity rates are met or exceeded, which means that you operate in the black.
Trade-offs of achieving consistent productivity rate
This is a new labor model and requires a period of adjustment to build into your daily operations. With your daily labor fluctuations, the quantity of workers will vary day to day, which can create some growing pains for your business as it adjusts to a dynamic workforce.
Cost comparison between optimizing for consistent labor hours vs consistent productivity rate
The rubber meets the road when comparing unit labor cost because the consistent productivity wins on this metric by 25%. It wins by this metric because it removes the “insurance” labor premium carried throughout the week or month as a safety net to meet demand spikes.
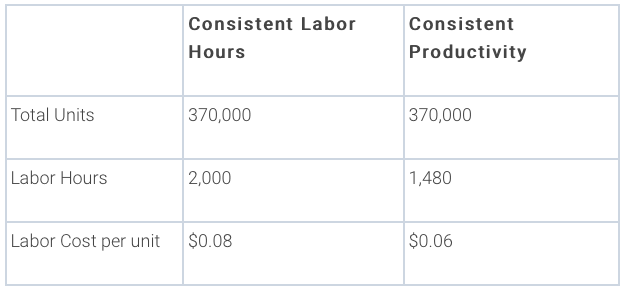
The total production units from the two approaches are the same at 370,000 units for the sample week. Labor hours are summed for each approach, and the consistent productivity rate scenario executes the work in less hours. The Labor cost per unit is the assumed labor hour cost of $15/hr multiplied by the labor hours. This labor cost is then divided by the total units to reach the labor cost per unit.
Which is right for my operation?
Ultimately, the decision is going to come down to operational factors of your business, industry, and culture:
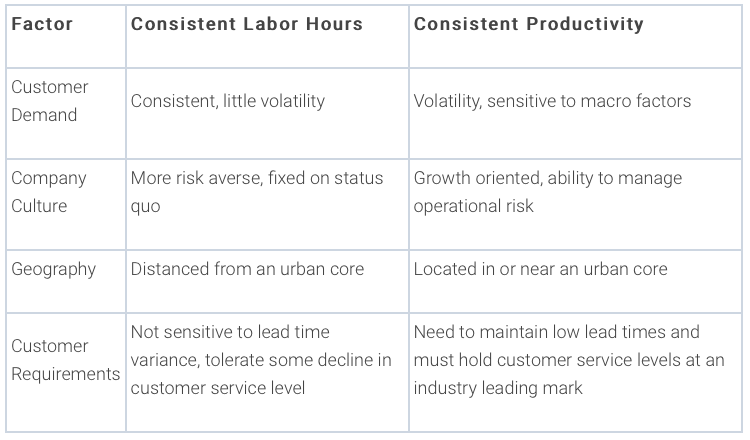
As a business leader, you will have to pick the path that better suits your company and industry.
Driving for the consistent productivity rate is the harder path because the labor hours have to be dynamically managed daily. We believe this path is worth it, though, because it is the path to growing revenue and earning high customer satisfaction. When you optimize for a consistent productivity rate, your operation becomes centered around meeting the customer need in that moment rather than scheduling it out into the future to maintain a consistent workforce level or equipment utilization.
Building to meet a productivity target is the better approach as a strategy to counter uncertain demand and forecasting challenges.
Does focusing on constant productivity sound right for you?
If you plan on optimizing for a constant productivity rate, read about on-demand labor and how it gives you flexibility in your labor capacity so you can orient around customer needs instead of holding labor constant.
Previous Posts
Old Roles, New Realities - Who Owns Agility?
The Future of Manufacturing and Logistics
Create a free business profile today to explore our platform.
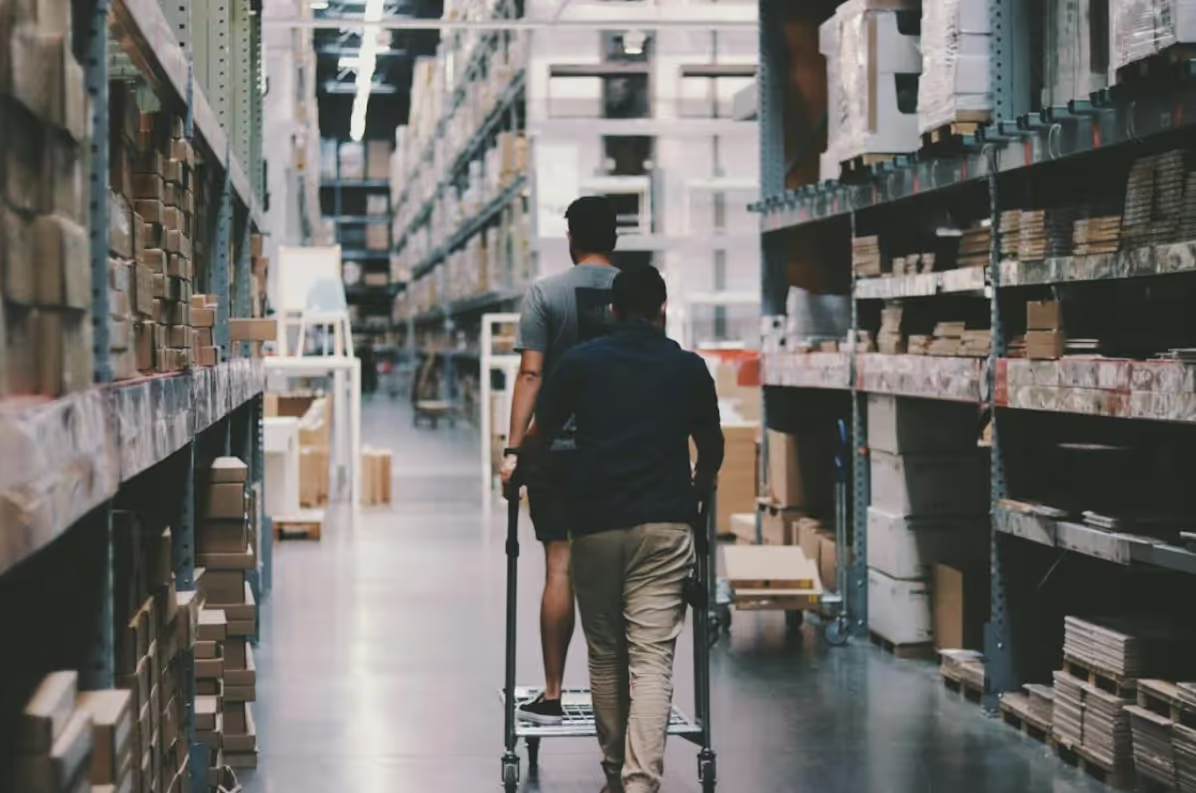