The Five S Methodology: A Powerful Lean Tool
One of the first steps toward adopting the Lean methodology is implementing the five S’s. You might have heard of these before, but we’re going to make it clear what these terms are, what they mean, and how you can use the 5S methodology to set a strong foundation for future operational improvements.
Veryable helps companies uplevel their operations by matching capacity to demand with on-demand labor. Advanced approaches like infinite flexible capacity are supported by building blocks such as the 5S methodology, and together they can make your operations hum.
In this article, you’ll learn about each of the 5S’s, when you should use them, and how to get started with the 5S methodology to set you up for success.
What are the Five S’s in the 5S methodology?
The five S’s in the 5S methodology come from Japanese words that all begin with the letter “S” and have to do with organizing and standardizing. The 5S’s can also be represented with English words.
Why should you use the 5S methodology?
The 5S’s form a foundational practice that makes your workers more efficient by reducing wastes, such as time spent searching for tools. This can translate into faster cycle times, a reduced error rate, improved safety, and the opportunity for better data collection and subsequent process improvements.
Beyond these operational results, this is also a powerful tool for cultural change. The mindset a proper 5S implementation can instill in workers will not only benefit your company, but each individual who participates in cultivating a systematic continual improvement mindset. The cultural shift truly begins when supervisors value what employees have to say about their processes, and each individual takes ownership of their work and its improvement.
How do you know if you need the 5S methodology?
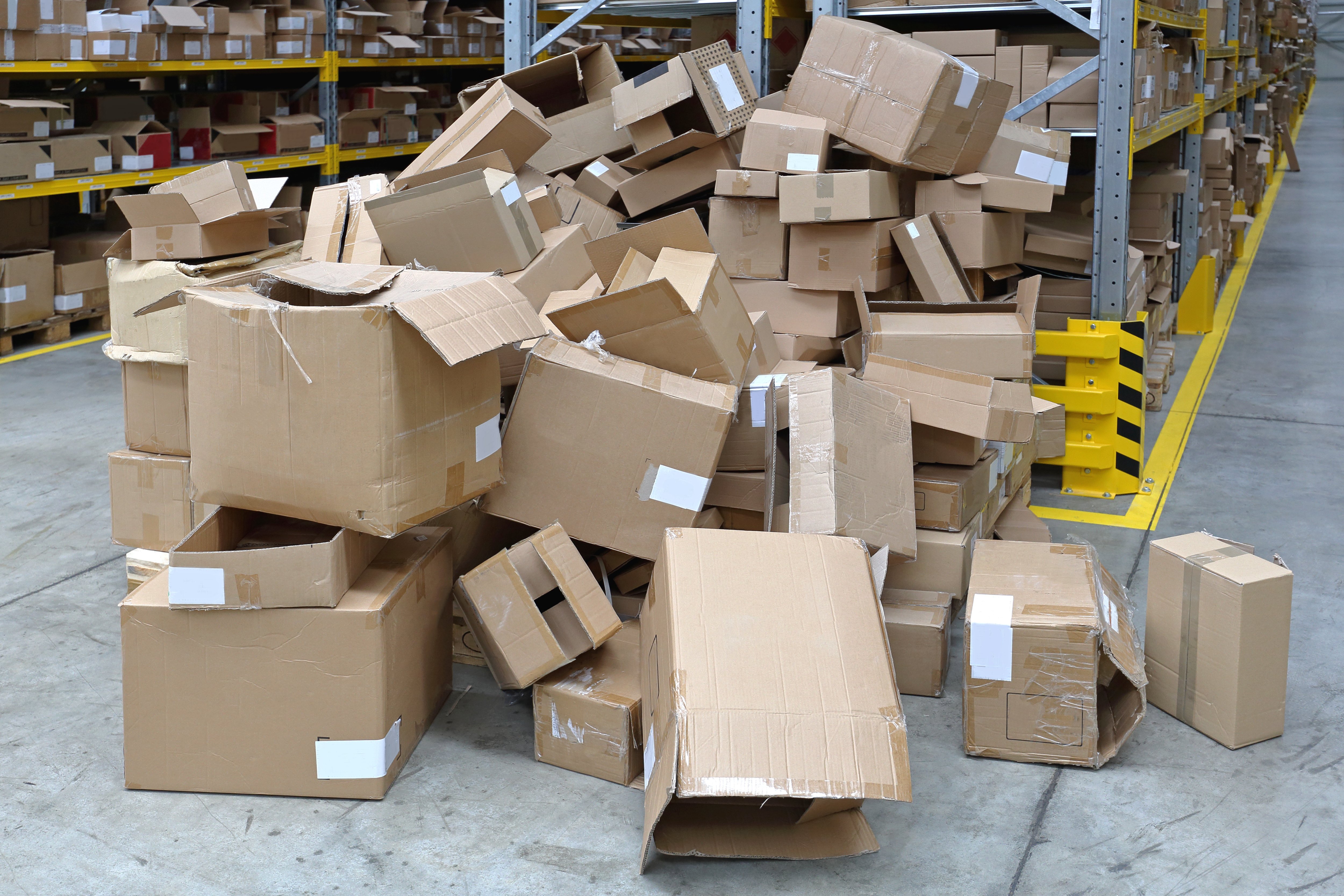
If you see messy looking workstations or storage areas, then you need to implement 5S. If your workers frequently ask where something is, that’s another sign that you should be using 5S.
It is generally a good idea to implement 5S if you work in manufacturing or logistics. Building quality into your processes will come much more easily if you have a strong foundational practice like 5S.
You can liken practicing the 5S methodology to having the discipline to keep your house clean. It might look fine day to day, but if you don’t clean it habitually, you might start losing things. Plus, you’ll have to clear your calendar for a whole day to clean the next time guests are coming over. It’s easier to keep it clean than it is to clean up a mess. It’s also easier if each member of the household takes pride in keeping their area clean, and each other member trusts them to do so.
What is 6S? (5S plus safety)
Some practitioners of the 5S methodology like to add a sixth S for safety. They aim to make vigilance in safety a daily habit and design processes with safety in mind.
Where does the 5S methodology fit with all the other Lean tools?
5S sets the foundation for other Lean tools such as kaizen events by establishing the basics of organization and a mindset of maintaining order and efficiency.
How do you implement the 5S methodology?
At a high level, implementing 5S should begin with establishing the expectation that everyone participates. Then, you should set up training that walks through all of the five S’s.
At the individual workstation level, each of the 5S’s should be applied in order.
Sort
Establish a clear definition of what should be discarded from workstations. Workers should be able to sort items with ease, based on the established guidance.
Set in order
Create shadow boards for items or equip your team with the tools necessary to create their own shadow boards.
Shine
Establish what “clean” looks like and make it easy to tell whether or not a workstation meets this standard. The shadow boards from the “set in order” step will be the first part of this. The next part of shining is to keep the area around the tools clean, for which there needs to be specific guidance or a rule of thumb at the very least.
Standardize
It is important to codify the standards that you set for sorting, setting in order, and shining. This could be as simple as a one-page checklist, or as involved as a digital work instruction flow with these steps built in. Whichever you choose, be sure to make the standard physically present near workstations so that workers are constantly reminded of the standard.
Sustain
Management should be responsible for monitoring the ongoing application of the previous four S’s. This means that each team member is holding up their end of the bargain and maintaining their workstation and shared spaces appropriately. You should create accountability for your managers so that there are clear expectations for upholding the 5S methodology in your workplace.
Next steps in the Lean journey
The improvements you make while implementing the 5S methodology will benefit you in your Lean journey tremendously. This jumping off point will build the habits and mindset of continuous improvement and waste elimination that are central to the Lean methodology.
For more information, visit our Lean Center of Excellence Homepage or our homepage for Continuous Improvement, Operational Excellence, and Lean Professionals.
Previous Posts
Trump 2.0 Week 30 In Review: Discussing The China Deadline Extension, The Potential For Even Higher Tariffs on India, and More
The Future of Manufacturing and Logistics
Create a free business profile today to explore our platform.
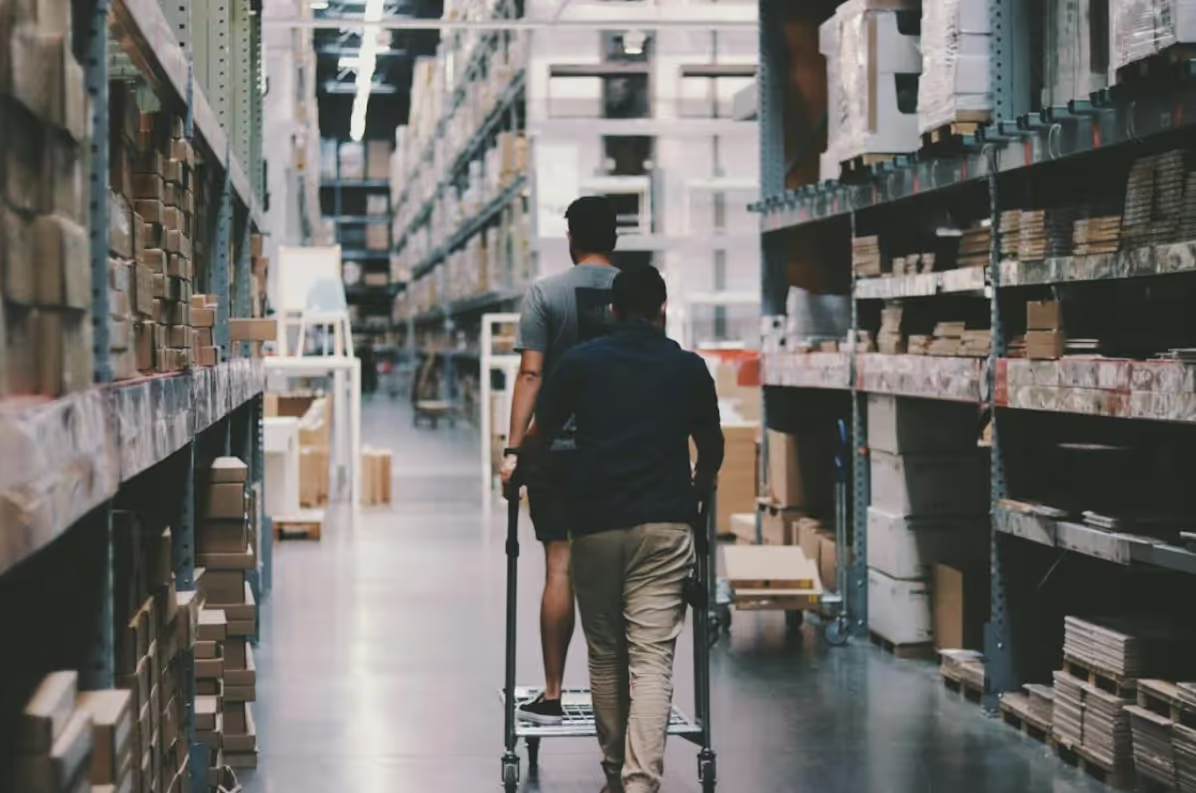