Veryable's October 2023 Automotive Industry Updates
In our October 2023 automotive report, we present essential insights regarding the ongoing strike led by the United Auto Workers ("UAW") and its ramifications for automotive suppliers. We also delve into the industry's current landscape, highlighting both the obstacles and prospects it offers, aiming to provide valuable guidance for legal and operational decision-making in response to these challenges and opportunities.
Notable Developments
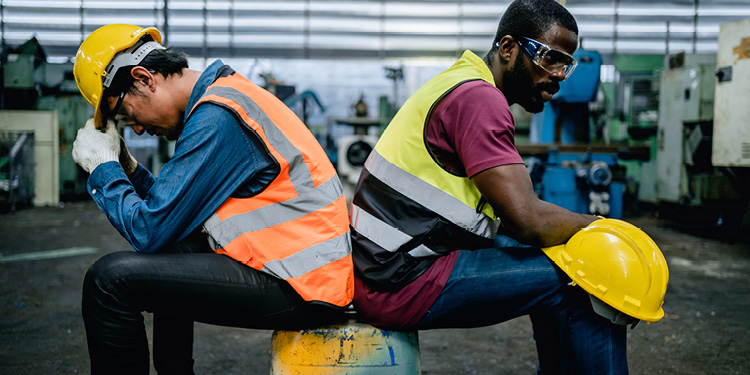
UAW Strike Continues: Since our last update in September, the United Auto Worker ("UAW") strike has intensified, with the number of auto workers on strike at Ford, Stellantis, and General Motors increasing from 13,000 to an estimated 34,000 (encompassing six automotive assembly plants and 38 parts-distribution centers). The most recent walk-out occurred on October 11 when 8,700 workers at Ford's truck plant in Louisville, Kentucky (its largest facility), walked off the job. The strikes have cost the three automakers, suppliers, dealers, and workers a total of $7.7 billion through October 12, as estimated in a new report by Anderson Economic Group of East Lansing, Michigan. The UAW insists that the automakers' offers still fall short of their demands, despite substantial offers from Ford, GM, and Stellantis, including wage increases exceeding 20% over four years, cost-of-living allowances, faster wage progression, extra paid holidays, and more.
Shift in Union Tactics: Previously, UAW President Shawn Fain had announced strike expansions on Fain's weekly Friday updates. But now, as part of the union's strategy to keep the automakers off balance, Fain said strike expansions could happen on any day of the week at any time. "We're entering a new phase of this strike, and it demands a new approach," Fain said. "We're done waiting until Fridays to escalate our strike."
Uncertainty in Ford and GM's Financial Strategies: The strikes have cost GM and Ford more than $500 million, as estimated by a JP Morgan analyst. With plans already in place to spend billions on developing new electric vehicles and the mounting costs, one must wonder if that's at risk. Ford, in particular, took a huge hit, as mentioned with the Kentucky Truck walkout. To put it in perspective, that plant generates $25 billion in revenue per year—or $48,000 per minute.
Layoffs Mounting: Approximately 550 employees from Ford have been asked not to report to work beginning October 16 -- including the Sharonville Transmission Plant, the Dearborn Stamping Plant, the Dearborn Diversified Manufacturing Plant, the Rawsonville Components Plant, the Sterling Axle Plant, and the Chicago Stamping Plant. This brings Ford’s total to approximately 2,480 employees impacted by strike-related layoffs. Ford has also cautioned that there may be 4,600 more layoffs within the next few weeks at nine other plants due to reduced production at the Kentucky Truck Plant.
Meanwhile, Stellantis has announced an additional 700 layoffs at two plants in Kokomo, Indiana, one specializing in transmissions and the other in castings. These plants supply parts to the Toledo Assembly complex, which has been on strike since September 15. Stellantis has now reached a total of 1,340 strike-related layoffs, while GM has 2,330 employees on layoff status.
The automakers argue that they have no alternative but to lay off workers who would otherwise have no work due to strikes at other plants. Stellantis explained that the recent layoffs were necessary because the two Kokomo plants had reached maximum inventory levels for parts used in the production of the Jeep Wrangler and Jeep Gladiator in Toledo. Unfortunately, most of the laid-off workers are not eligible for unemployment benefits, as they would be in other situations.
MEMA Survey on Layoffs: A recent survey conducted by the Motor & Equipment Manufacturers Association ("MEMA") has shown a nearly 10% increase in layoffs compared to the previous week. About 39% of surveyed vehicle suppliers have laid off some of their direct labor employees. Of those suppliers who haven't laid off workers yet, half intend to do so starting the week of October 30. Additionally, over 30% of the surveyed suppliers anticipate that it will take them more than one to over three weeks to restart their idled production. Labor and material availability challenges are the primary obstacles they face. Furthermore, nearly 80% of the suppliers express concerns about the financial viability of their sub-suppliers, and 30% of these suppliers are somewhat concerned about their own internal financial stability.
UAW Workers Face Challenges with Strike Pay: The challenges experienced by striking workers were covered in a recent Detroit Free Press article. Union workers on strike are currently earning $500 per week -- further reduced after taxes. The moral of the story -- striking isn't easy on anyone.
Supplier Guidelines and Preparing to Resume: Brief Commentary
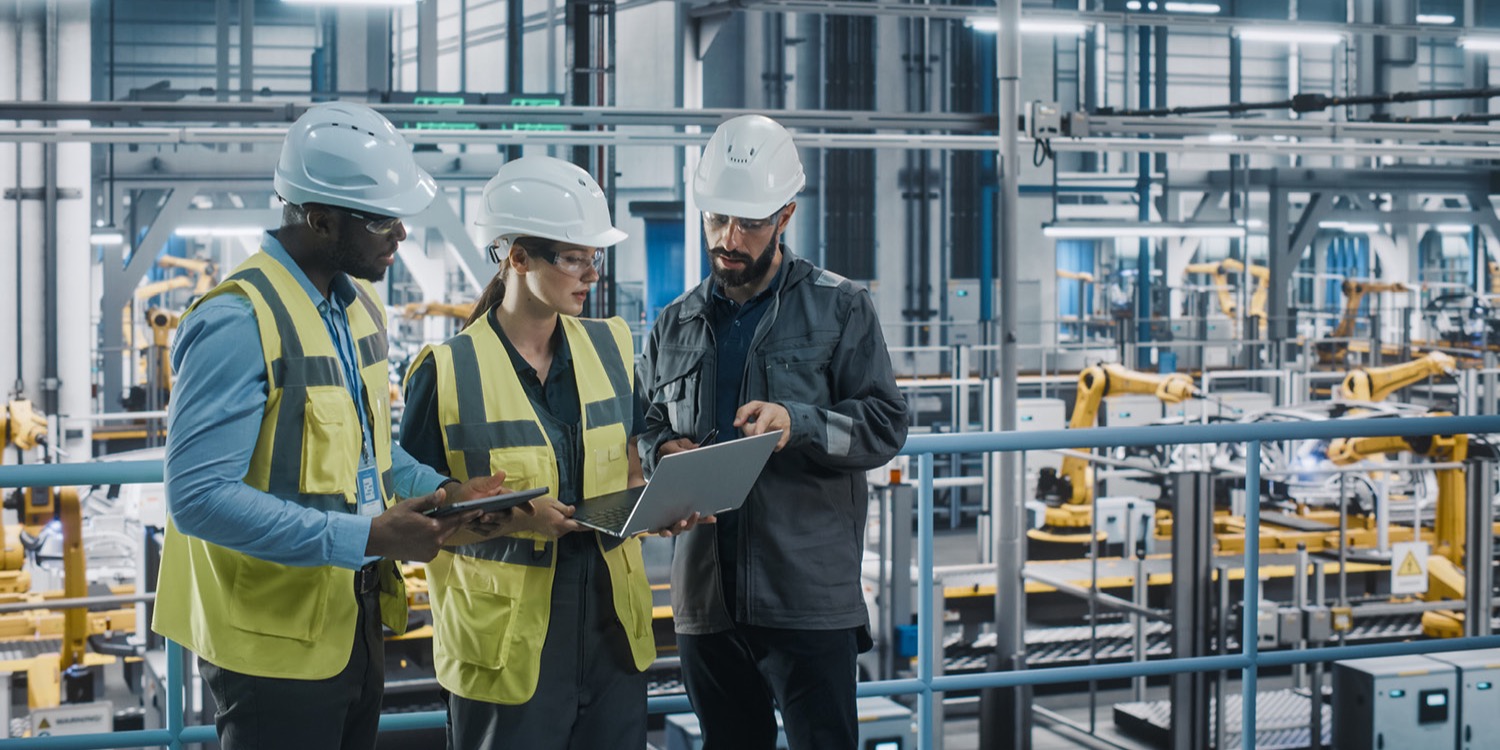
Suppliers must take into account various factors and prepare for a potential restart amidst the ongoing strike. The longer the strike persists and the deeper its impact, the more it will negatively affect the demand for parts and materials, causing cash flow issues for automotive suppliers. In this context, suppliers should consider several strategies:
- Speeding up the collection of receivables, which may involve options like factoring.
- Shipping finished goods inventory to convert working capital assets into cash, including exploring whether customers are willing to accept excess finished goods beyond EDI releases.
- Deferring payables when it makes sense and maintaining clear communication with lenders and customers to ensure they are informed about your financial situation and needs, thus avoiding significant distress.
Furthermore, the duration and severity of the work stoppage will determine the specific actions and adjustments needed for the workforce. It's crucial to acknowledge the possibility of a permanent loss of workforce availability in the current competitive labor market when production resumes. Suppliers should evaluate how the UAW strike affects their labor force and consider the potential for the strike to extend over an extended period.
The ripple effects of the UAW strike are already being felt, with supply lines outside the three main targets being impacted and, in some cases, completely halted. Suppliers should carefully manage their output to prevent an oversupply of obsolete or soon-to-be outdated parts when Original Equipment Manufacturer ("OEM ") production eventually resumes.
Suppliers should also be vigilant in distinguishing between projected forecasts and firm orders, as the strike may lead to significant variations between the two. They should adjust their production capacity and lead times for sub-suppliers accordingly, based on the terms governing when projected forecasts become firm orders.
In preparation for a production restart after the strike concludes, suppliers should be aware that OEMs are likely to demand an aggressive production schedule to compensate for the downtime. Given that production shutdowns and restarts can result in substantial costs, suppliers should devise strategies to minimize material and labor expenses once production resumes. Additionally, they need to allocate their resources fairly to meet customer demand and should communicate clearly with customers regarding lead times and costs required for the restart after a shutdown.
The Impact of Veryable
Since the onset of the UAW strike, Veryable has received inquiries from and forged partnerships with numerous businesses. As the trailblazers in on-demand labor, we stand ready to provide assistance, be it in maintaining crucial supply lines or gearing up for the expected surge in demand from OEMs after the strike's resolution. To learn more, please explore our homepage dedicated to on-demand labor in the automotive industry and get in touch with our automotive lead.
Previous Posts
Trump 2.0 Week 25 In Review: July Deadline Extended, 50% Copper Tariff Announced, and Higher Tariffs for Canada, Brazil, and BRICS
The Future of Manufacturing and Logistics
Create a free business profile today to explore our platform.
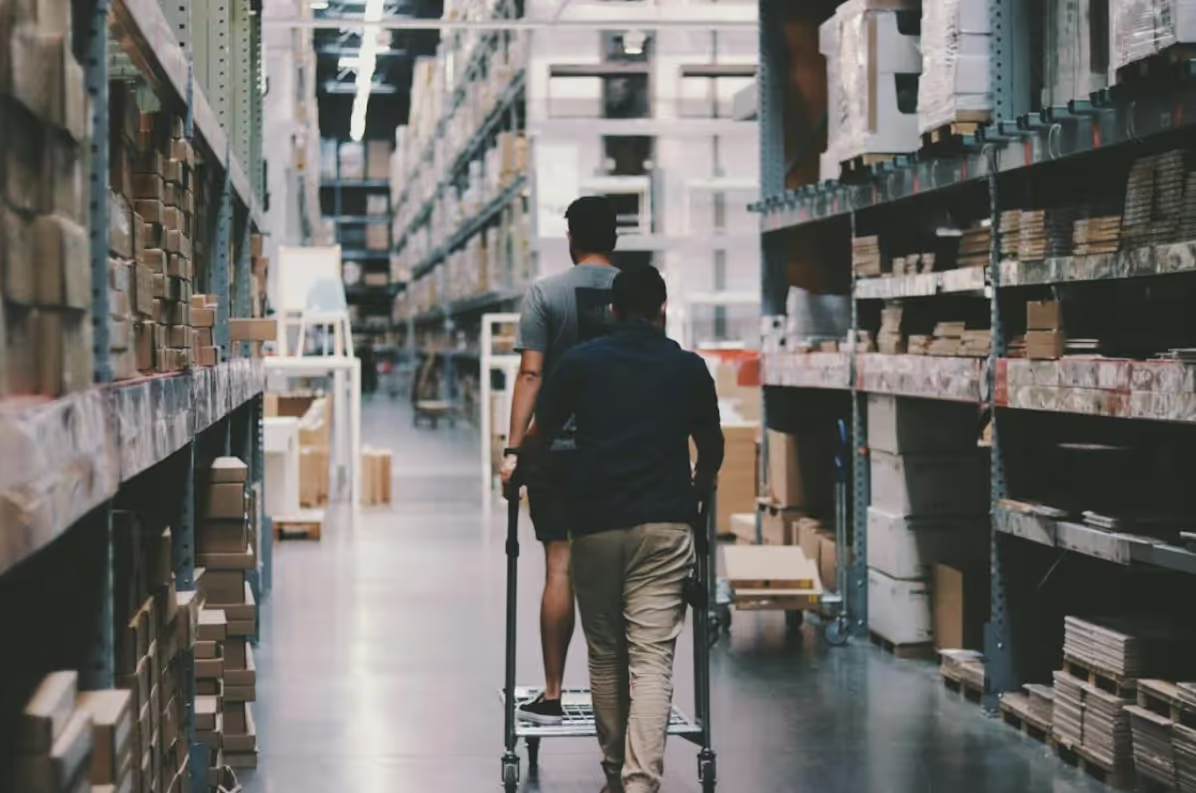