The Future of Manufacturing: Additive Manufacturing
The future of manufacturing is localized, agile, asset-light, and focused on customization to meet each customer’s preference.
A key enabler of this shift is additive manufacturing. Additive manufacturing is a method of production that selectively adds materials to create a product, rather than removing material from a block to form the product. It is commonly referred to as "3D printing," although additive manufacturing is the preferred term because there are other methods besides 3D printing which are considered additive manufacturing.
The data supports this growing trend toward additive manufacturing: the industry grew 19.5% in 2021, according to a Wohlers Associates press release announcing their comprehensive annual report.
This relatively new method of production could spur step-level changes in localization and customization by reducing the need for specialized machinery for each part of a product. It thereby removes the reliance on far-flung companies to produce one particular part that could hold up production for weeks.
This article is part one of a series called “The Future of Manufacturing,” in which we’ll explore the technologies and ideas that will be used in the next manufacturing revolution. We will share a high-level view of these technologies and concepts, acknowledging that these articles are just a starting point for your journey to a deep understanding of each technology and idea.
While nobody can know everything about these and predict the future perfectly, we’ve drawn on the years of experience from the experts on our team to form a perspective that we are certain is directionally correct.
Pros of Additive Manufacturing
The benefits of additive manufacturing over other manufacturing methods include:
- Customization of each widget without requiring additional processes
- Rapid iteration on product design as a result of inherently customizable production
- Less manual labor required to produce widgets
- Material efficiency gains compared to subtractive processes
- Waste reduction and leaner inventories
- Complex and previously unachievable designs are possible
- Reduced setup time
- Batch size one at no cost
- Decentralization of manufacturing
These benefits will enable the decentralization of manufacturing when the machinery becomes sufficiently advanced in its capabilities such that manufacturers will not have to purchase specialized machines for each part they wish to produce at scale. This will allow the further localization of the supply chain by removing the reliance on distant suppliers who have the machinery needed to produce something.
An end-to-end additive manufacturing solution and subsequent localization would result in a shift in international trade from intermediate or finished goods to raw materials. This would simplify trade and related logistics.
Cons of Additive Manufacturing
The benefits are clear, but there are also drawbacks with additive manufacturing due to the current state of the technology.
The cons of additive manufacturing include:
- Mass production of widgets is slower than traditional methods
- Print jobs require supervision
- Immature market for additive manufacturing materials
- Limited talent availability for additive manufacturing machine operators
- Transition from current suppliers to additive manufacturing would highlight inadequacies in product blueprints that were previously addressed with undocumented changes to the production process
- Post-production processing requirements that differ with each piece (example)
Most of these drawbacks are the result of vendors needing more time to iterate and advance the technology. Some of these, like limited talent availability, are problems that equipment vendors cannot solve by themselves. There will certainly be progress towards more user-friendly machines, and in the meantime there will be less training-intensive supporting roles that must be filled.
But during this transition, there will be a (potentially long) period in which a skills gap presents a major obstacle. One possible solution is migrating CNC machinists to the new machinery, considering the skill overlap between the two roles. CNC machinists could easily translate their skills from their previous role into blueprint reading for the 3D print files to ensure quality and finishing processes for the printed products.
The problem of labor for additive manufacturing is one that Veryable is particularly interested in solving. The support roles that require less training are great candidates for on-demand labor, and the more training-intensive roles created by additive manufacturing will be a new challenge for all of us in the manufacturing industry to solve together.
What Should You Know Before Adopting Additive Manufacturing?
While it might sound exciting, there are plenty of reasons that not everyone has adopted additive manufacturing. There are questions around how to implement the technology, what the costs are, and whether it will replace or coexist with established production methods.
Below we will explore each obstacle to adopting additive manufacturing and offer the information and solutions we could find for each.
Equipment availability and costs
Additive manufacturing machinery has come a long way in the past few decades, and the list of quality machines to choose from has grown. Notable options for commercial-grade additive manufacturing include:
- https://www.aon3d.com/
- https://www.3dsystems.com/
- HP multi-jet fusion
- EOS selective laser sintering (SLS)
- ExOne binder jetting
- Stratasys
- Markforged
- Velo3D
The costs of these systems vary. You should expect to spend starting around $2,500 for a small-scale professional model, but costs can quickly get into the $100k+ range to purchase large industrial machines that print using metals. See the table below for a breakdown of a few different types of 3D printers and materials available on the market today.
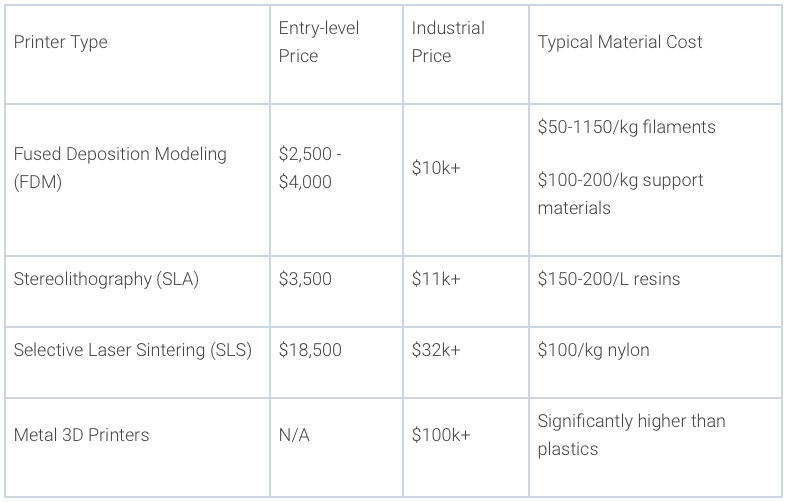
Source: Form Labs
Are there on-demand options?
You can also send your designs to 3D printing farms (sometimes called a “cloud manufacturing” service) or find a local 3D printing company specializing in quick turnaround for industrial-grade additive manufacturing.
Can you lease 3d printers?
There are options available for leasing 3D printers and additive manufacturing devices. In some cases, printers are available to lease directly from the machine manufacturer. In other cases, you will have to do some legwork to arrange a lease through a third-party provider.
Read more about leasing or renting 3D printers here.
Capabilities of Additive Manufacturing
One important question to answer is whether additive manufacturing can be used to produce what you need.
If popular culture is any reflection of how far the technology has come, you could reference the 2001 blockbuster film Jurassic Park III, in which a basic sort of printer was shown (slowly) making a velociraptor resonating chamber. The technology has evolved since then, and we are living in a world with more advanced tech than many sci-fi authors foresaw.
So let’s dive into whether today’s additive manufacturing technology can be the primary method of production or just a way to prototype and make small batches.
There are many different methods for additive manufacturing, including:
- Binder jetting
- Material jetting
- Material extrusion
- Powder bed fusion
- Sheet lamination
- Directed energy deposition
- Selective laser sintering
- Area printing
The most recent, cutting-edge approach is called “area printing,” which Seurat technologies recently raised $41M in funding to bring to market.
The new method seeks to address the main limitation of current additive manufacturing methods, which stem from the tradeoff between accuracy and speed inherent to the currently available machines. 3D printing is either fast or accurate, but to date has not been capable of both.
Considering these limitations, the most common use cases for additive manufacturing today include:
- Rapid prototyping
- Small batches of customized metal parts
- Full-scale production of small plastic items
- Small batches of products with complex designs
Despite the limitations, the following industries are increasingly adopting additive manufacturing:
- Medical device manufacturers
- Aerospace engineers
- Auto parts designers
- Dental practitioners
- Architects and designers
- Home construction companies
What Materials Are Used in Additive Manufacturing?
Popular materials include:
- Resins
- Powders
- Plastics
- Woods
- Concrete
- Metals
Supporting materials required might include argon gas, compressed air, printing materials for support structures, coolants, and polishes.
These materials are becoming more widely available, and there are some established suppliers in the space. For example, Stratasys sells many types of materials on its marketplace, and GE sells metal powders.
Product Designs for Additive Manufacturing
The good news is that most additive manufacturing machines will accept the common file types you’re accustomed to using in CAD programs.
If you’re confident in your designs, you can start production or send the files to your additive manufacturing supplier right away. Revisions will be faster when you receive a prototype, because you can just edit the file locally and send it back right away.
It’s important to ensure that your suppliers document any changes they’ve made to your product designs so that you can pass those along to the additive manufacturer or use them in your own machine. It is critical that you avoid losing the tribal knowledge you’ve accumulated between your company’s designers and your supplier.
Additive manufacturing has its own quirks, just like working with any other manufacturing machinery. Your operators will need to learn the machines and make adjustments to designs as they go. Ensure that you have a system in place for documenting these changes, especially if it has been a long time since you last checked on your documentation practices.
How does Additive Manufacturing Enable the Future of Manufacturing?
As mentioned above, additive manufacturing will one day remove the need for reliance on far-flung suppliers of specific parts by allowing a company to make any part they might need in their own facility.
Beyond localization, additive manufacturing also enables customization of each widget. Customers could place orders for small batches or even individual products at a negligible transaction cost.
Localized manufacturing would have the added benefit of being a better choice for the environment. While there are wastes specific to additive manufacturing, such as the necessity of support structures or the powder byproducts of SLS machines, the overall environmental impact of additive manufacturing would be an improvement. By reducing the travel time needed to deliver products, improving material efficiency, and recycling support structure materials and flawed products onsite, additive manufacturing operations would reduce waste.
It is hard to overestimate the impact that additive manufacturing will have on the future of manufacturing. However, the workforce will have to adapt to this revolution. That is where flexible work models will come into play.
The customized, localized nature of the future of manufacturing will require the workforce to be flexible because it cannot use the same leveling methods that centralized mass manufacturing has relied on for decades. To do so would undermine the entire premise.
On-demand labor can address this exact problem, just like it does for existing manufacturers. A flexible workforce will allow manufacturers to respond to the fluctuations inherent to a localized production footprint that emphasizes just-in-time and customization.
Learn more about how on-demand labor works to prepare yourself for the future of manufacturing.
Previous Posts
How Veryable Addresses The Top 5 Challenges Highlighted in the NAM's Q2 2025 Survey
The Future of Manufacturing and Logistics
Create a free business profile today to explore our platform.
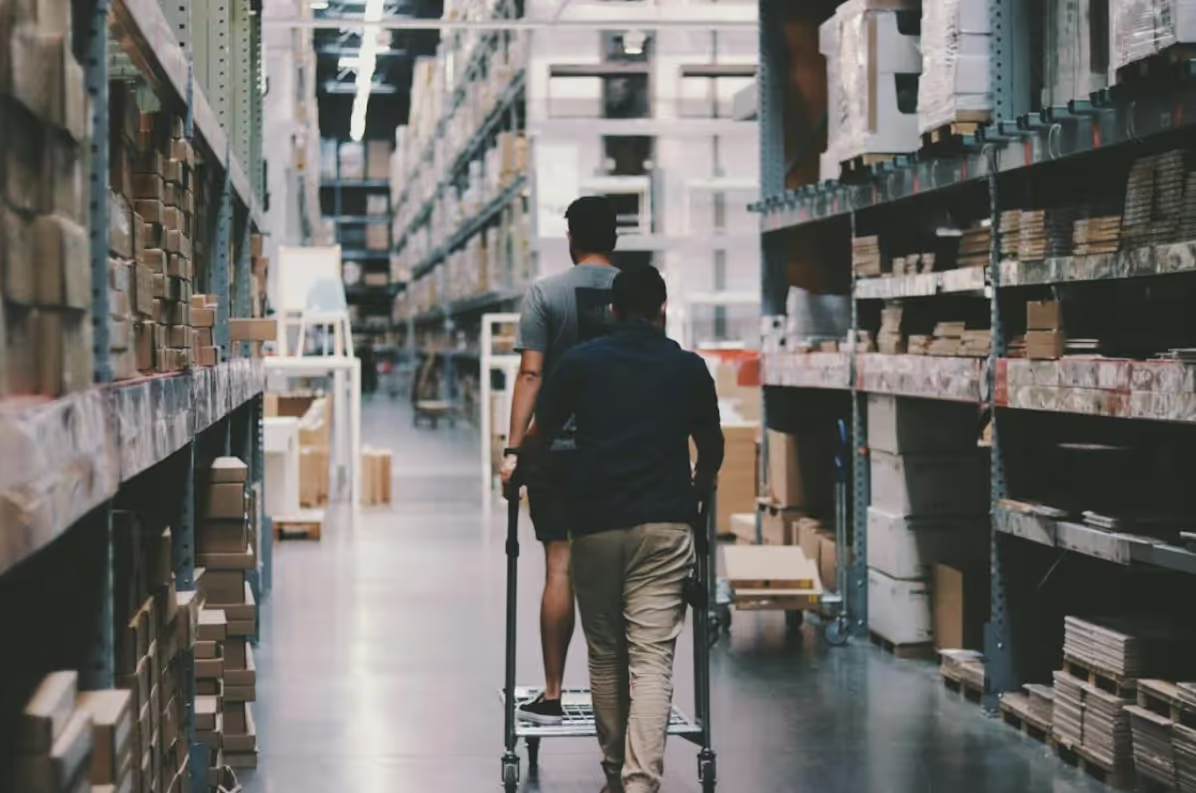