A Plan for the Unplanned Shutdowns
Diving into the heart of the automotive industry, this blog post looks at the core fundamental aspects of the automotive supply chain. As the lifeblood of vehicle manufacturing, any disruption can send shockwaves through the value stream. Highlighting the repercussions of an unplanned shutdown, we will review the challenges faced by stakeholders at each step and propose strategic solutions. With disruptions becoming an inherent challenge, our focus is on equipping industry players with strategies of resilience. This ensures they do not merely survive but rather thrive in this ever-changing landscape.
The Automotive Supply Chain
The supply chain of any industry is a complex machine. Regardless of the product, the process shares a common flow and structure. Looking specifically at automotive, it is composed of an intricate network comprised of procurement, assembly, and delivery of vehicles and vehicle components. The integration of sourcing raw material, manufacturing, transportation, and sale of final goods ensures vehicles are produced and delivered efficiently. Given the global reach and extensive list of complex parts and components, it demands precise coordination. Any disruption at any stage of the process can immediately impact operations both upstream and downstream. This level of complexity and interdependence highlights the importance of precise management and planning.
Taking this into account, let’s look at a simplified overview of what comprises the different areas.
- Tier Suppliers - Provide raw materials, components, and sub-assemblies required to build vehicles. They ensure the availability of high-quality, precisely engineered components essential for the various stages of the manufacturing process.
- Original Equipment Manufacturers (OEMs) - Utilize the supplied raw materials and components to assemble and produce the final vehicle. This is where the actual transformation of parts into final products takes place.
- Logistical Providers - Responsible for the safe and timely shipment of materials and finished vehicles to assembly plants or distribution centers and dealerships. Doing this allows the precise movement of products, mitigating delays and disruptions in the supply chain. This is critical for time-sensitive vehicle deliveries.
- Distributors and Warehouses - Manage inventory of finished vehicles and automotive parts until they are needed by retailers/dealers or assembly plants. They are the buffer, adjusting the supply and demand to protect against market volatility and uncertainties.
- Dealerships and retailers - Facilitate the sale of the finished product (vehicles) to the consumer, providing various options, and ensuring consumer satisfaction. They represent the brand and act as the final touchpoint with the consumer. They have a direct influence on the purchasing decision and brand loyalty of the customer.
- Consumers - The ultimate buyer of the finished vehicle, whose preferences, needs, and feedback drive the entire automotive market industry and trends. Their purchasing decisions and usage patterns shape the market dynamics. Their influence can impact automotive design, production, and supply chain strategies.
The Bullwhip Effect of an Automotive Shutdown
Unplanned shutdowns have a ripple effect that cascades through the entire supply chain. One key plant or site producing a high-volume, well-selling vehicle unexpectedly shutting down will not be an isolated event. It will start to impact every step involved with any part of the vehicle. This starts with the raw material being dug from the ground and goes all the way to the individual that eventually purchases the vehicle.
Tier suppliers face challenges in delivering materials and components due to disruptions in production schedules and logistics. There may be an accumulation of materials intended for delivery, leading to storage and obsolescence issues. Contracts may need to be renegotiated due to inability to meet delivery timelines, possibly creating financial instability. Demand can evaporate overnight, and releases will change drastically from forecast.
OEM assembly lines stop, causing delays in vehicle production and this leads to financial losses. Workforce management becomes a challenge, with a direct impact on employee morale, productivity, and, potentially, employment status. As unplanned shutdowns go on, short-term layoffs then become more prevalent. The sudden halt might compromise the quality of products in the production line, creating additional checks and balances once production resumes. This will inevitably result in incremental costs.
Logistical providers see a drop in orders, causing a ripple effect on delivery schedules and transportation contracts. With no goods to transport, vehicles and the workforce are left idle, affecting operational productivity and incurring costs.
Distributors and warehouses may face capacity constraints and limitations due to the accumulation of undelivered inventory. Effective management of incoming and outgoing goods becomes critical to avoid losses due to damage or obsolescence.
Dealerships and retailers with a lack of new stock see an impact on sales. This leads to potential losses and strained relationships with customers. They may look to realign prices and offers in response to product scarcity or abundance, impacting profitability.
Consumers encounter delays and potential unavailability of vehicles or specific customer order configurations, which can have a negative impact on satisfaction and brand loyalty. An increase in demand with a decrease in supply often leads to price hikes, i.e., market adjustments. This then can influence the choices of prospective buyers. Subsequentially, this deteriorates brand loyalty and has a negative effect on current and future purchases. Modern day consumers tend to have a lower level of brand loyalty when compared to those in the past, because of this, buyers are more susceptible to having their opinions influenced by price.
Stabilize
Automotive companies need to act strategically during an unplanned shutdown to mitigate impact and facilitate recovery. There is an extensive list of things that can be done but there are two key areas directly related to the supply chain.
First, assess your overall supply chain, look to better optimize the value stream, and start working your way back through the entire process. Look at reviewing inventory levels and regularly assessing raw material, WIP, and finished goods. Then review obsolescence to identify materials or products that are or are about to become obsolete. Then focus on in-transit inventory management, value stream mapping, logistics for route optimization.
Second, look at strategic supplier(s) and customer communication. Engage the appropriate contacts to maintain open lines of communication to better understand potential disruptions and adjust delivery expectations accordingly. Consider updating expectations or renegotiating contracts as needed to address delivery delays and other disruptions.
Safeguard
To safeguard against future unplanned shutdowns, manufacturers should strategically reinforce every part of their operational structure. Strengthening supply chain resilience is key and can be achieved through supplier diversification, optimized inventory maintenance, and leveraging advancements and initiatives. This includes the various aspects of Industry 4.0.
Start with developing robust contingency plans. These plans should be detailed, regularly updated, and reflective of varied emergency scenarios. This will ensure swift and coordinated action during disruptions. Update documentation accordingly and be sure to audit it annually to align with your IATF 16949:2016 certification.
Invest in technology solutions is pivotal. Look to leverage advanced analytics and software for precise demand forecasting, inventory optimization, and early identification of potential supply chain disruptions. Implement a flexible capacity strategy to boost operational agility and productivity. Lastly, focus on enhancing your workforce resilience through cross-training and upskill progression to ensure continuity during disruptions.
With 40% of Intertech’s business being services to Tier 1 and OEM suppliers, they experience significant swings in production schedules. Often running day-to-day scheduling, Veryable has been instrumental in lowering costs.
Conclusion
Your supply chain is a critical, intricate component of your business. It takes an unparalleled complexity within any industry, especially the automotive sector. There are a multitude of components and systems that must come together to bring a vehicle from concept to reality. This framework requires meticulous management and streamlined operations to prevent and navigate disruptions, particularly during unplanned shutdowns.
Times like this throw a proverbial wrench in the works, leading to mounting issues in logistics, production schedules, workforce management, quality assurance, customer expectations, etc. Such disruptions require immediate strategic response to minimize the impact of cost, optimize supply chain components, maintain open and constructive communication, and reassess inventory levels and logistics.
As we look to the future, proactivity and strategic fortification of operational structures is important. It is what sets businesses apart. Investing in contingency plans, technology driven solutions, and workforce resilience will shine a light on the industry leaders. Veryable specifically addresses these areas and works to drive operational excellence. By embracing this new way of operating, the automotive industry has become our fastest growing market. This is driven by the mutual goal to not only survive or sustain but to thrive and innovate in an ecosystem marked by its constant state of perpetual motion. Doing this will steer the industry toward a future marked for success.
Click here for more information on Veryable, case studies, customer videos centered on the work we are doing specifically in the Automotive Industry.
Previous Posts
Trump 2.0 Week 27 In Review: New Trade Deals with Japan & Indonesia, Stalled Talks with Canada & India, and Tense Negotiations with the EU
The Future of Manufacturing and Logistics
Create a free business profile today to explore our platform.
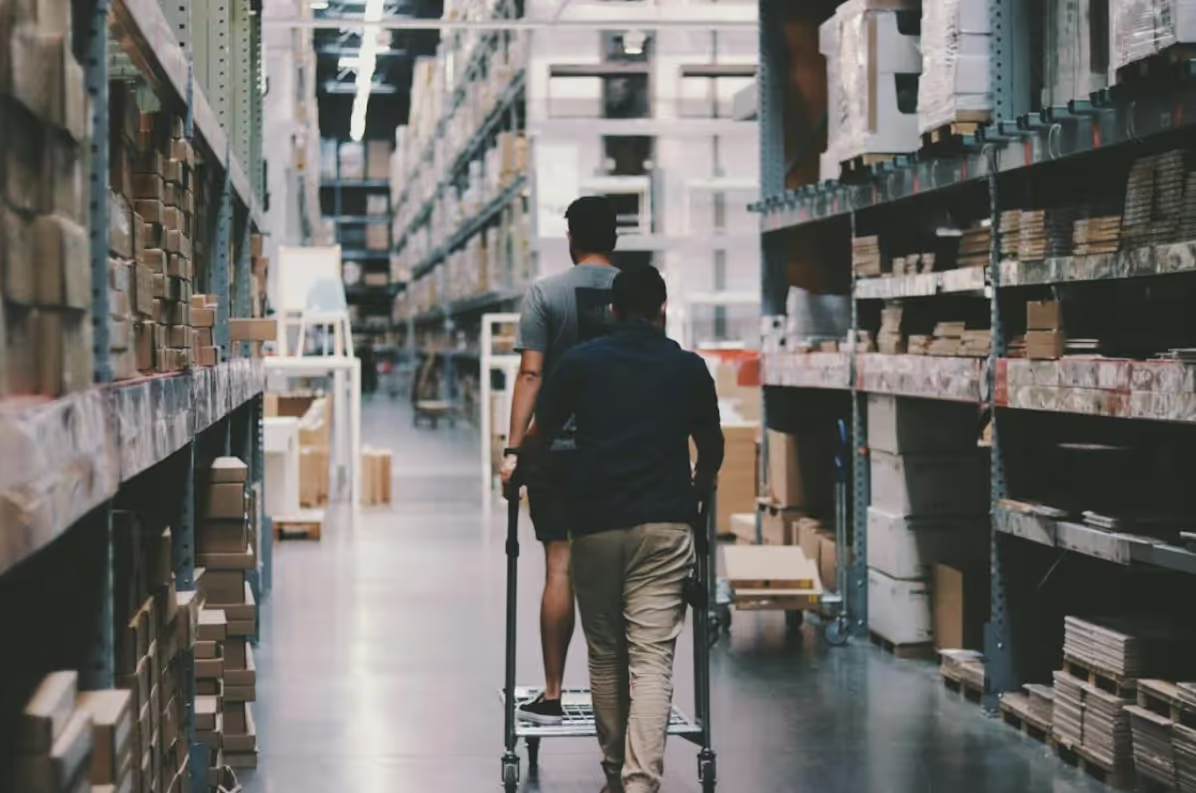