The Pitfalls of Relying Only on Full-Time Employees
If you say “we only want to hire full-time employees,” then you’ve probably been burned by temp staffing or aren’t aware of all the options for finding workers to get work done in your facility. Keeping your labor capacity at the right level is a big problem to solve, and if you expect better results, you’re going to need to change your methods.
At Veryable, we enable manufacturers and distributors to build a labor pool of on-demand workers through our on-demand labor marketplace. We want to share what we’ve learned from these companies and our team members with real-world operations experience about relying only on full-time employees (good and bad) so that you can make an informed decision on how you will manage your labor capacity.
In this article, you will learn the pros, cons, and alternatives to only hiring full-time employees.
What is the goal of hiring?
When you set out to hire people for your facility, it’s important to keep in mind why you’re doing this. It sounds elementary, but people often overlook the reason why they’re hiring, and they end up making costly decisions based on tradition or intuition.
Hiring is supposed to match your labor capacity to the demand for your product or service. So if you’re hiring to keep six roles filled because your workers produce 20 units per day and you consistently need to produce at least 120 units per day, that’s the correct approach. It’s based on the needs of your business, and you’ll consistently have enough work for those six people.
However, if you’re hiring because you’ve always had six employees, so you have to get back up to six employees, that’s not the right way of looking at it. Likewise, if you’re hiring because you feel like you’re running behind constantly, that’s not the right way to approach solving your problem. These are the equivalent of throwing spaghetti at the wall and seeing what sticks.
With this in mind, you might have noticed that if you’re aiming for the ultimate goal of hiring, the traditional approach of only hiring full-time employees is average at best. We will explore the pros and cons of this approach in detail below, although we warn you now that the cons outweigh the pros for traditional staffing in most cases for manufacturing and logistics companies.
Why do some people only hire full-time employees?
When you hire full-time employees only, you will get the same people every week. This gives workers the opportunity to get familiar with your operations and specialize or move up in your facility. Note that you can get the same benefit when using on-demand staffing or on-demand labor companies that have a “favorite” feature or allow you to build your own labor pool.
Only having full-time employees means you have a clear way to hold workers accountable. If your full-time employees know they have to keep coming into the same place, they know their coworkers and supervisors will keep them accountable. They’ve put all their eggs in one basket, so they will likely be very careful with that basket.
Cons of hiring full-time employees only
When you only have full-time employees, you do not have the flexibility to meet increased or decreased demand on a daily or weekly basis. Onboarding FTEs takes too long to respond to a daily or weekly increase in demand, and then there would be excess labor capacity as soon as the variation swings the other way. Likewise, when you have a slow week, giving employees less hours (and less pay) is a quick way to lose the workers you’re reliant on.
Exclusively hiring full-time employees is slow. When employees leave and you are shorthanded, it could take weeks or months to find workers to replace them. You become reliant on your FTEs with no real backup plan or if something doesn’t go according to plan.
Having only full-time employees is inefficient from a cost perspective. When you need to output more volume for the week but you only have FTEs, you will have to pay them overtime to accomplish this. It’s expensive to pay time and a half, but even more expensive when these employees turn over and you’re spending more resources to backfill the attrition. In the case of lower demand for the week, you’re paying people who have less work to do, or sending people home with less hours than they want or need. This upsets employees, causing costly turnover yet again.
Finally, only relying on full-time employees when you have variation in demand can be downright unfair to employees. The inconsistent and unpredictable scheduling, the pressure to work overtime, and the pressure not to use their time off because the facility is running behind are all problems that will grind employees down until they quit. Nobody likes to be jerked around, and in a tight labor market, employers who do this will face consequences as workers choose to find greener grass.
Alternatives to only hiring full-time employees
There are multiple alternatives to only hiring full-time employees. Many companies attempt to gain flexibility via other strategies, such as temp staffing, on-demand staffing, and on-demand labor. The most viable of these for manufacturing and logistics companies is on-demand labor.
Many companies use temp staffing, but are often unsatisfied with their results from temp staffing because it’s not addressing the root problems with an FTE-only strategy.
Others use on-demand staffing to fill the gaps in their headcount, but this approach also does not differ much from traditional staffing methods. Adding technology to inherently restrictive methods do not fix the root problems with those methods.
The best alternative to an FTE-only labor capacity is to combine a baseline of FTEs with on-demand labor. This isn’t a revolving door, although it might seem that way on the surface if you are used to dealing with temp staffing agencies and other less-than-ideal approaches to managing your labor capacity. You have control over who works in your facility, and you can continue inviting the same people time after time if they perform up to your expectations.
The best alternative: on-demand labor for manufacturing and logistics
Remember what the goal of hiring should be: matching your labor capacity to the work at hand. You should match your labor capacity to demand on a daily basis.
Traditional hiring has typically failed to achieve this, and cannot achieve this because of the bureaucracy and lack of transparency involved in the hiring process.
On-demand labor solves the problems that traditional staffing and an FTE-only approach to labor capacity couldn’t. With on-demand labor, you pay for workers when you need them, and you maintain control over who comes to work in your facility. Read our blog defining on-demand labor and its benefits to learn how you can improve efficiency with on-demand labor.
Previous Posts
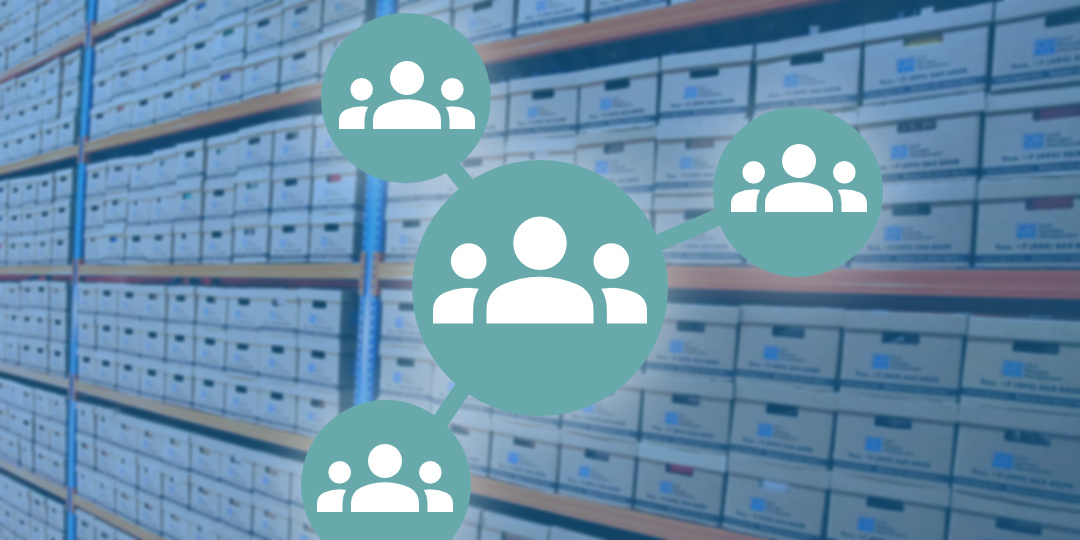
What is Staff Augmentation?
The Future of Manufacturing and Logistics
Create a free business profile today to explore our platform.
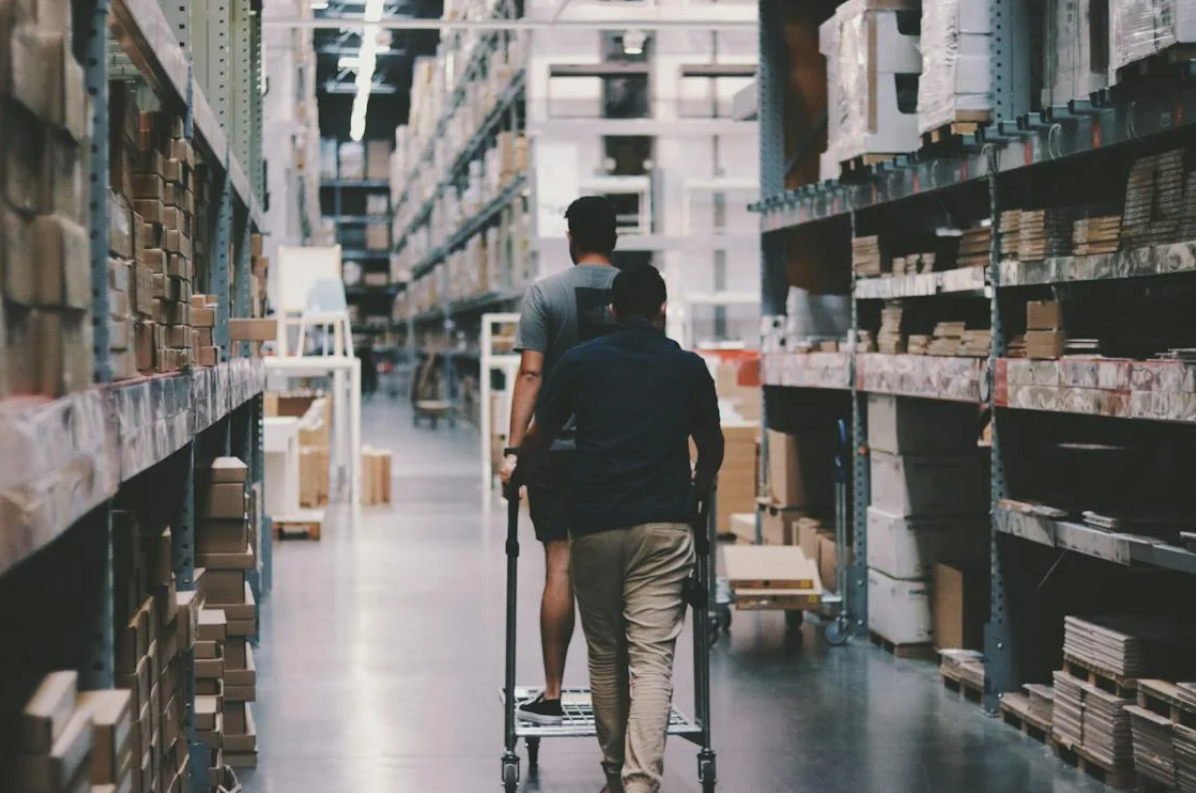